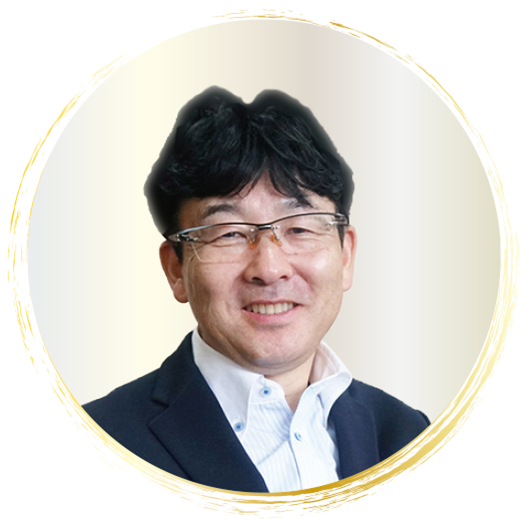
金田氏
本日はよろしくお願いいたします。
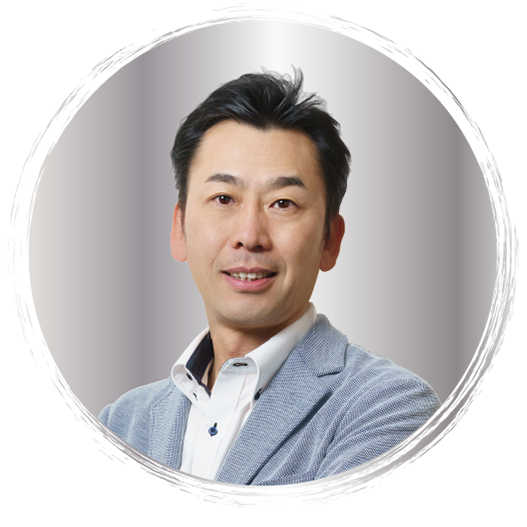
サイボウズ増田
(以下、増田)
(以下、増田)
本日はお話できること楽しみにしておりました。では早速、まず自己紹介と会社紹介をお願いいたします。
電気・電子機器分野の総合的コア技術の開発製造販売を行う東電工グループ
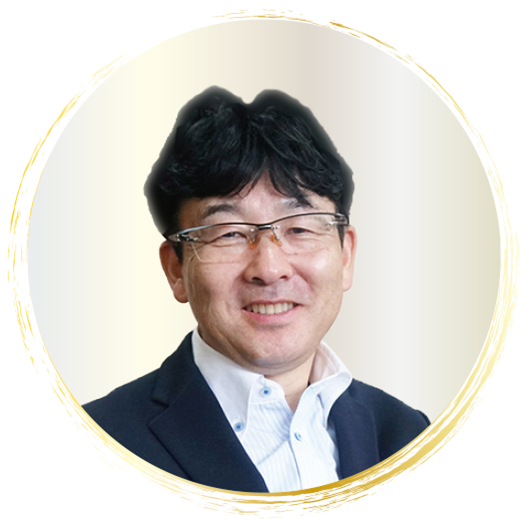
金田氏
東莞東電工電子有限公司総経理金田と申します。1986年に東京電線工業株式会社に入社いたしました。そこから、那須工場で電線とケーブルの製造に携わっておりました。2013年から2018年までタイ工場に出向しまして、ハーネス加工の製造にも携わり、改善等の取り組みも行なっておりました。それから昨年末12月末に現在の東莞東電工電子に出向となり現在に至っています。
趣味は釣りとゴルフですが、ゴルフに関しては中国に来てからまだ2回ほどしかプレイできておりません。釣りに関しましても、まだ3回ほどでして、予定はするのですが毎回雨でキャンセルになってしまいます...。時間を作りまして、釣りやゴルフの趣味にも取り組んでいきたいと考えております。
趣味は釣りとゴルフですが、ゴルフに関しては中国に来てからまだ2回ほどしかプレイできておりません。釣りに関しましても、まだ3回ほどでして、予定はするのですが毎回雨でキャンセルになってしまいます...。時間を作りまして、釣りやゴルフの趣味にも取り組んでいきたいと考えております。
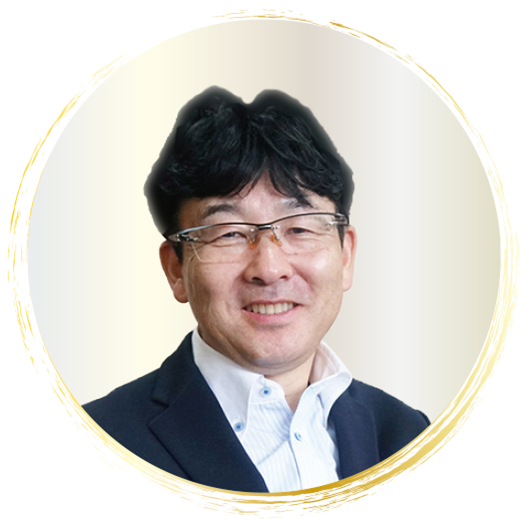
金田氏
それでは会社の概要と製品の説明をさせていただきます。
1998年に材料加工工場として設立いたしました。2011年2月に東莞東電工に名称を変更しました。工場の所在地は東莞市の樟木頭です。従業員数は若干の変動はありますが、6月末時点で310名となっております。
東電工グループはまず日本に二拠点、本社が東京都の狛江市、製造拠点が栃木県那須市にございます。その他海外は中国に四拠点とタイに一拠点です。
1998年に材料加工工場として設立いたしました。2011年2月に東莞東電工に名称を変更しました。工場の所在地は東莞市の樟木頭です。従業員数は若干の変動はありますが、6月末時点で310名となっております。
東電工グループはまず日本に二拠点、本社が東京都の狛江市、製造拠点が栃木県那須市にございます。その他海外は中国に四拠点とタイに一拠点です。
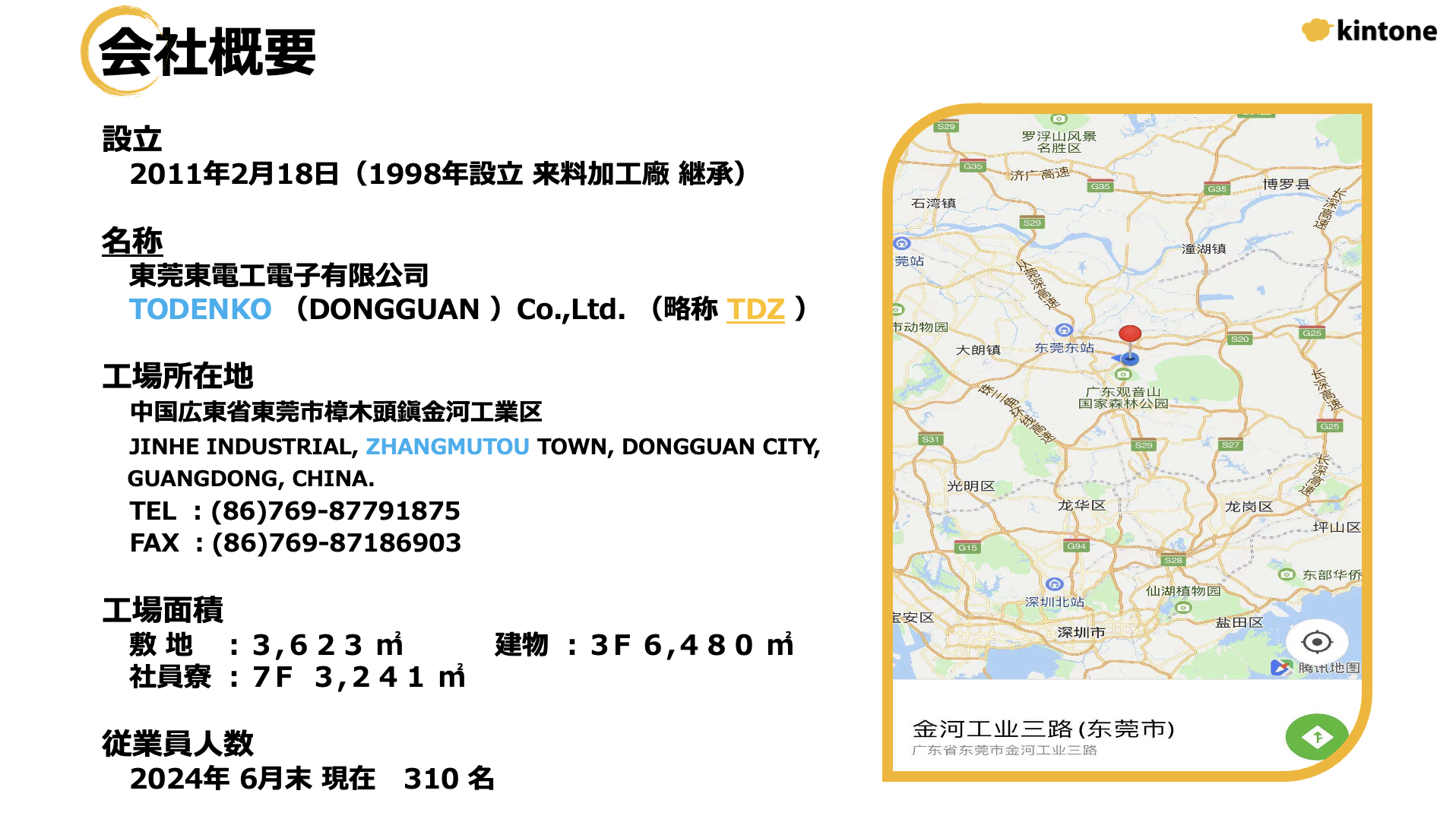
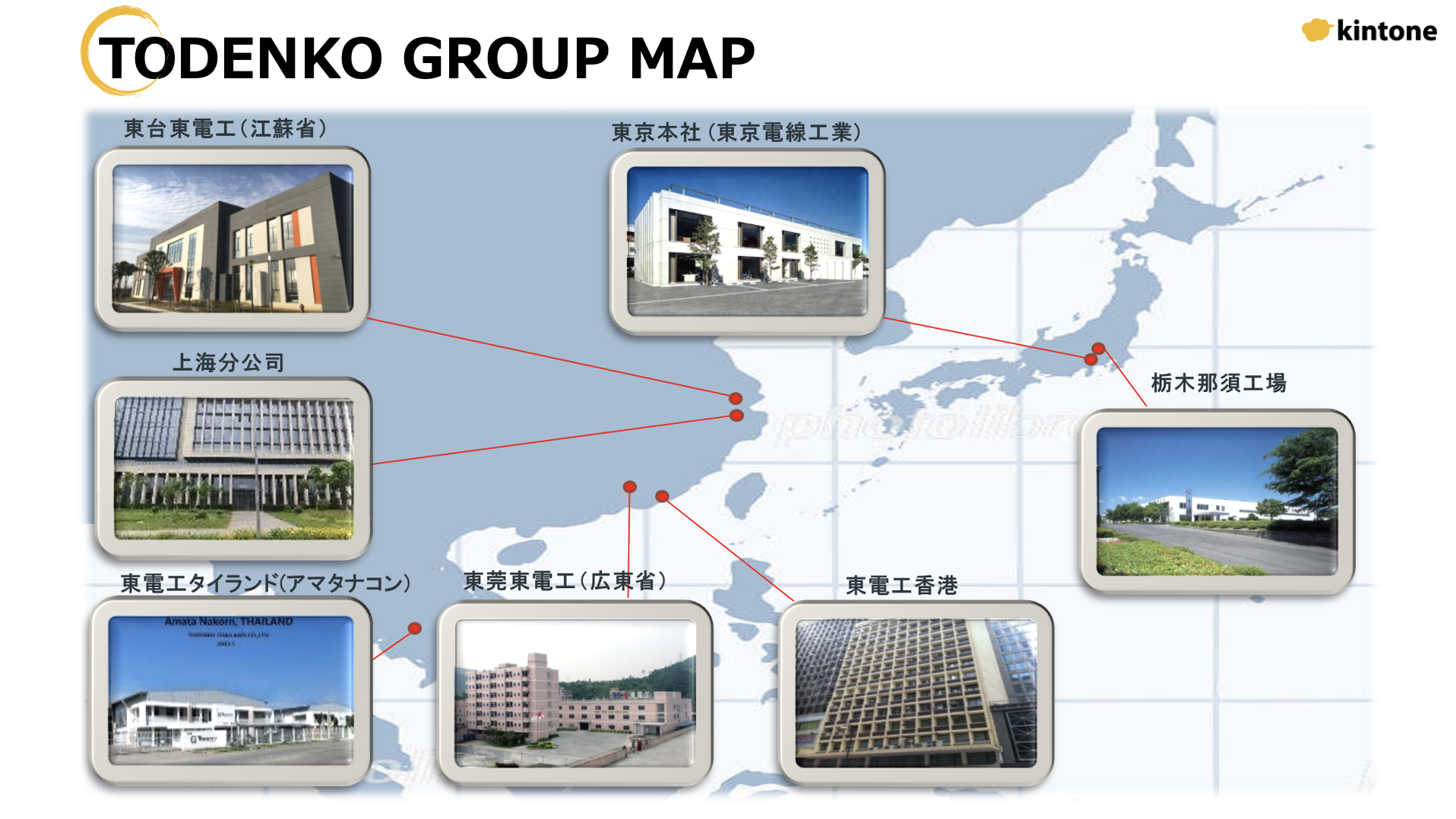
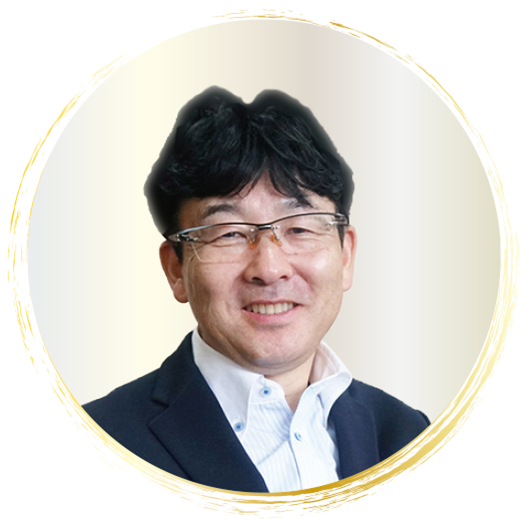
金田氏
業務内容につきましては、電線・ケーブルの製造とハーネス加工の製造となっております。
我が社が生産しているもの一つ目は、自動車用バックモニター、エアバック、シートベルト用のハーネスを作っております。そして、プリンターやATM、鉄道ホームドア用ハーネス、例えば日本ですと新幹線や山手線のホームドア用を作っています。また、エアコンの温度センサー用や固定電話、船舶の冷凍用やレーダー用など様々なところで使っていただいています。
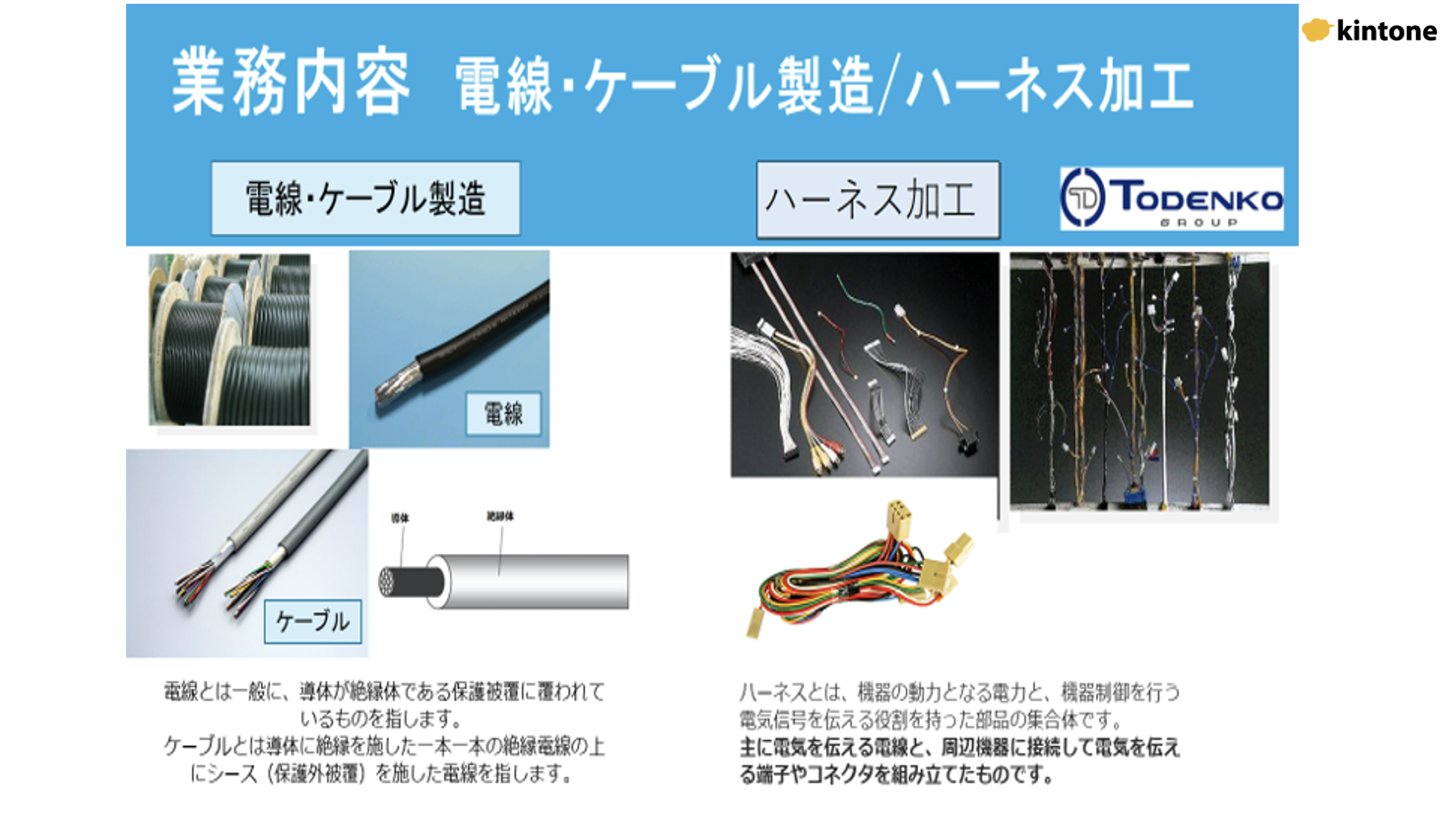
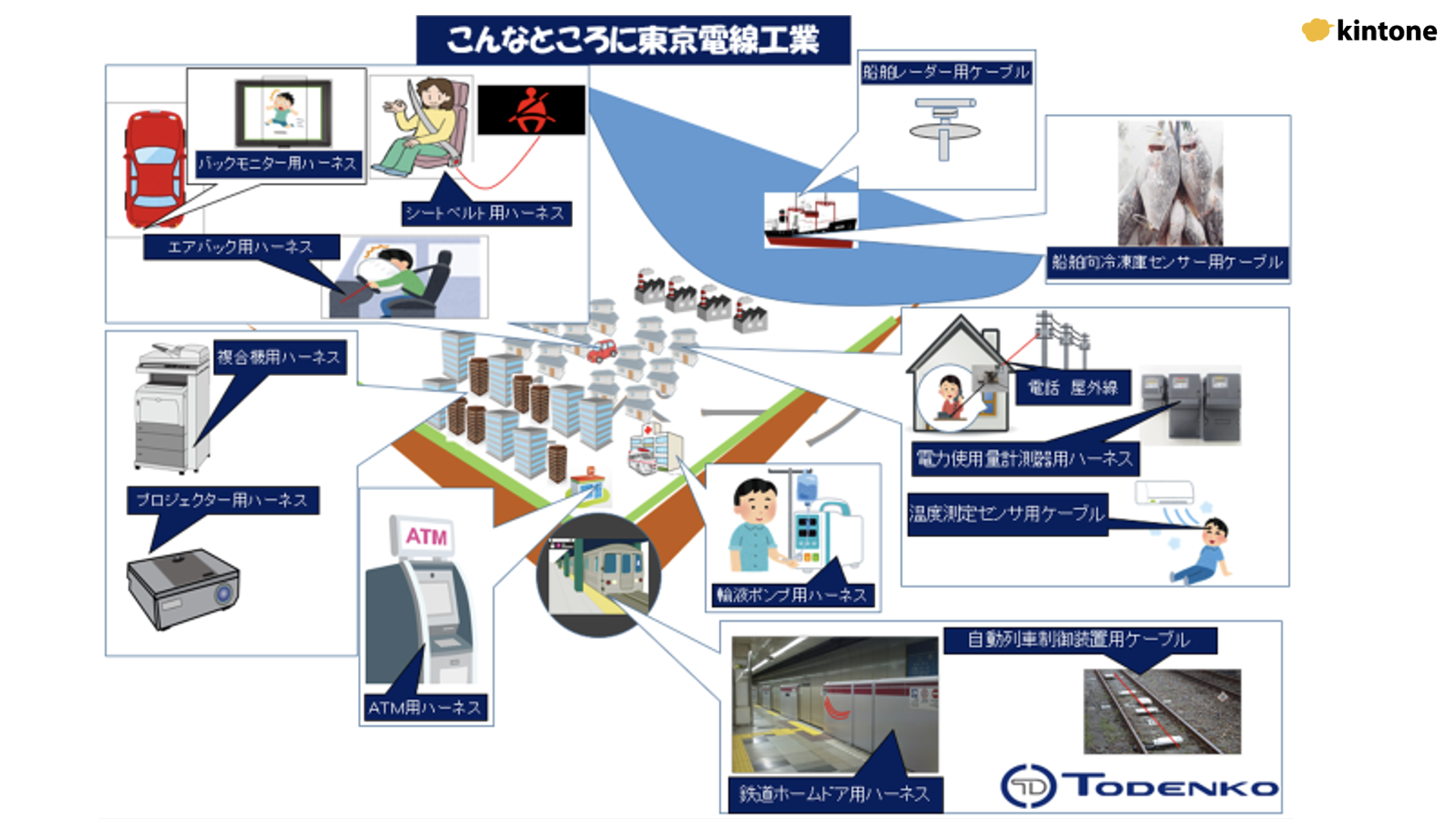
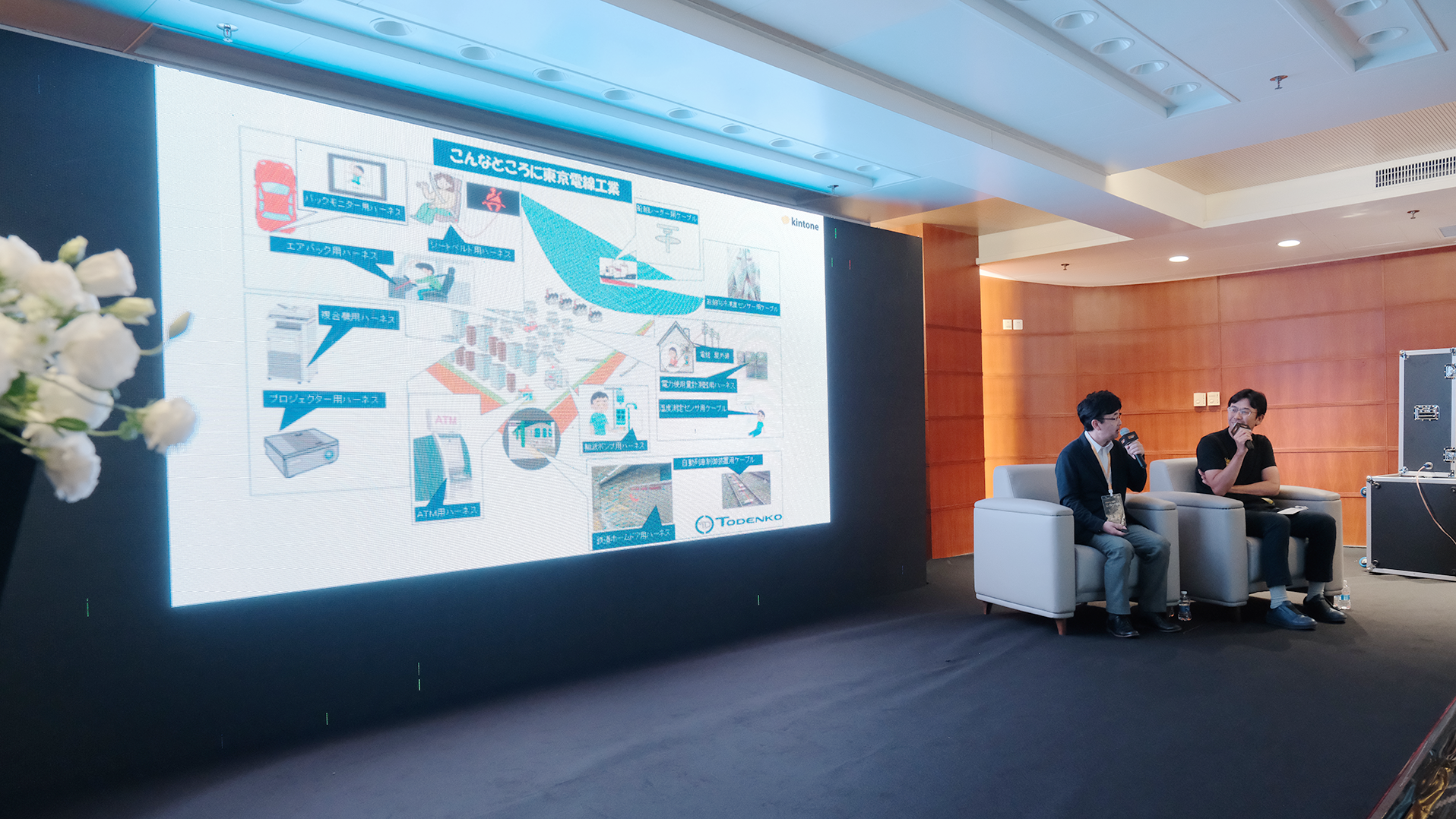
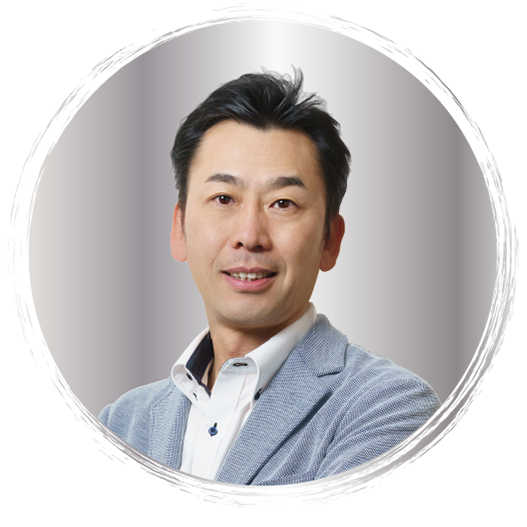
増田
ありがとうございます。以前はタイ工場にいらっしゃり、八ヶ月前に東莞工場に着任されましたが、工場の雰囲気などの何か大きな違いはありますでしょうか?
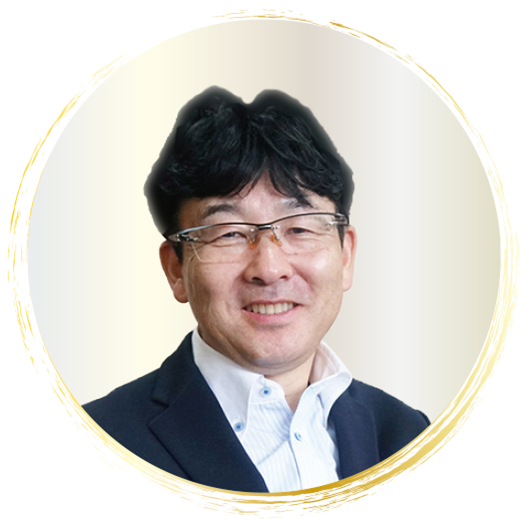
金田氏
違いといたしまして感じるのは、タイ工場は中国の方と比べると少し手が遅いな、という印象があります。中国では何か問題が発生すると皆で集まってワイワイガヤガヤして解決し、品質にはこだわっている印象があります。逆に日本はもっと違っています。日本はそもそも人が少ないですし、滅多に不良も出ませんので、黙々と手を動かして作っている印象です。
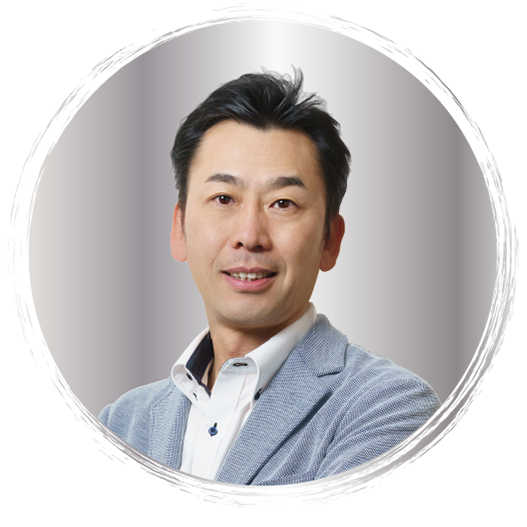
増田
なるほど、ありがとうございます。製造されている製品は輸出向けと国内向けでいうと、どれくらいの比率で展開されているのでしょうか?
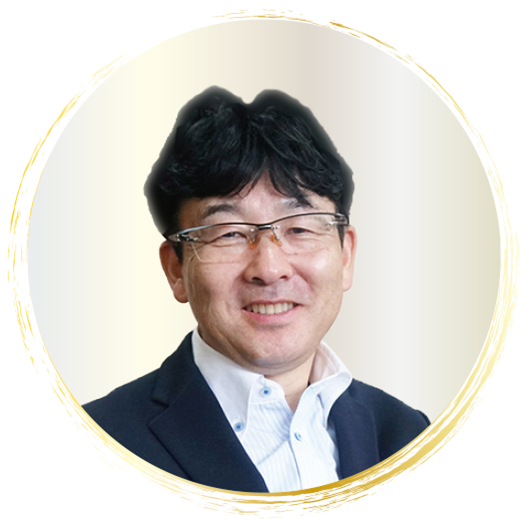
金田氏
だいたい輸出が6割で、国内が4割という形になっております。
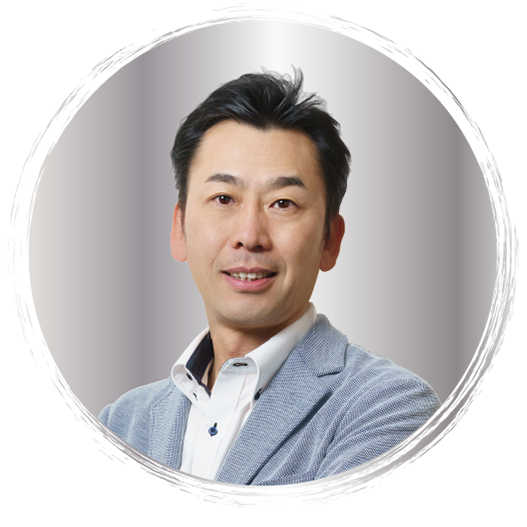
増田
やはり今は国内向けが伸びているのでしょうか?
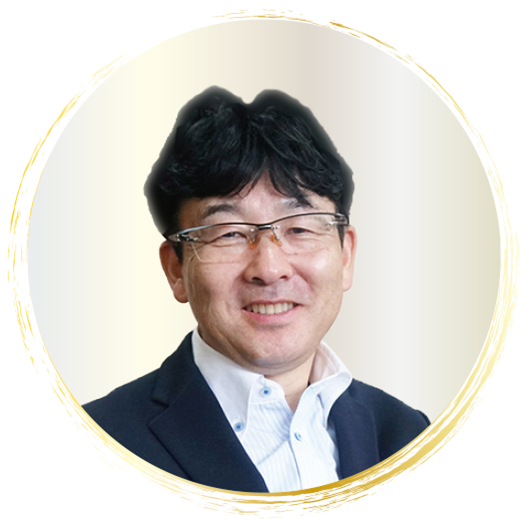
金田氏
いや、昨年まではよかったのですが、現在は計画に関しては横ばいだなという印象です。
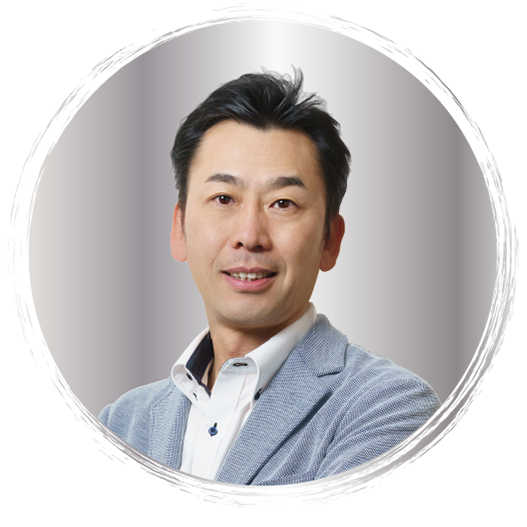
増田
ありがとうございます。そんな東電工様ですが、kintoneは2021年から活用いただいております。導入前の課題をお聞かせいただけますでしょうか。
効率的だと思っていたExcel管理が、想定以上の移動と動作の無駄に繋がっていた
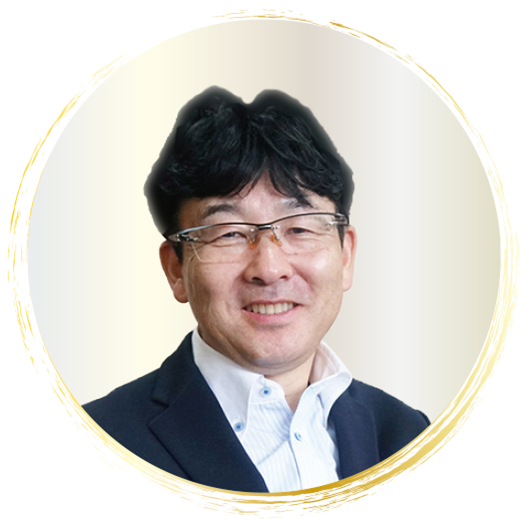
金田氏
導入前の課題といたしましては、三つの業務で課題がございました。
一つ目は工程内不良の管理、二つ目は5Sパトロールで指摘された内容をまとめ、改善案や改善結果をまとめた資料を作り上げる作業、そして三つ目は電線に端子を取り付ける時の圧着作業の金型ショット数管理業務です。これらの業務では以前はエクセルを使って管理をしていましたが、想定以上の移動のムダ・動作のムダに繋がっていました。
一つ目は工程内不良の管理、二つ目は5Sパトロールで指摘された内容をまとめ、改善案や改善結果をまとめた資料を作り上げる作業、そして三つ目は電線に端子を取り付ける時の圧着作業の金型ショット数管理業務です。これらの業務では以前はエクセルを使って管理をしていましたが、想定以上の移動のムダ・動作のムダに繋がっていました。
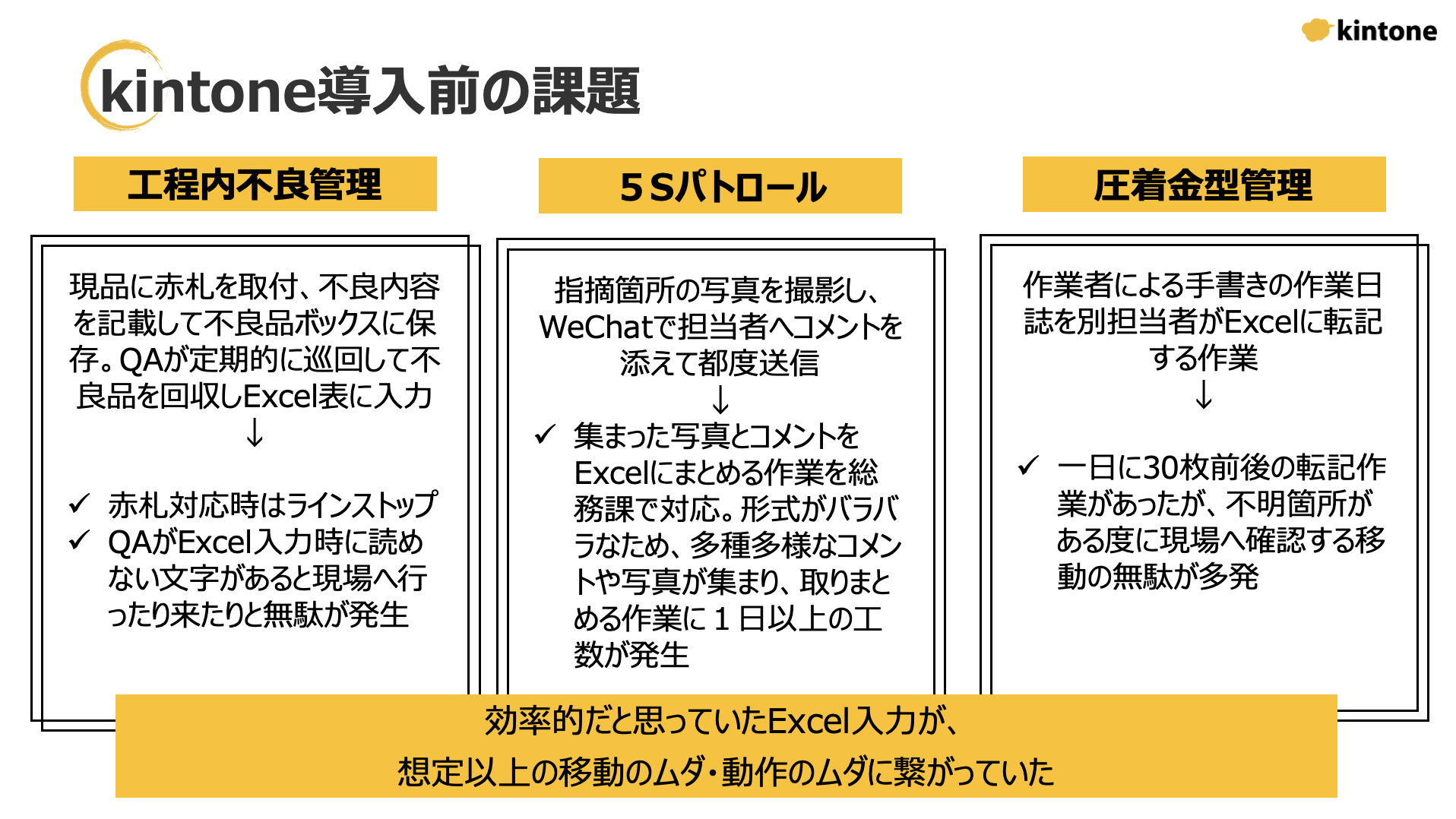
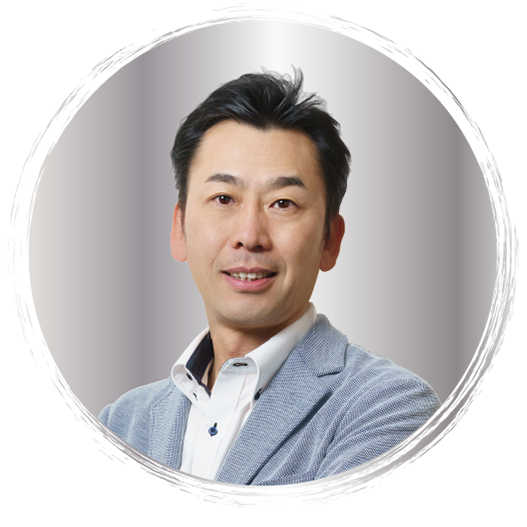
増田
これらは深圳エリアのお客様へ訪問するとよく伺う課題なのですが、専門システムみたいなものはやはりないものなのでしょうか?
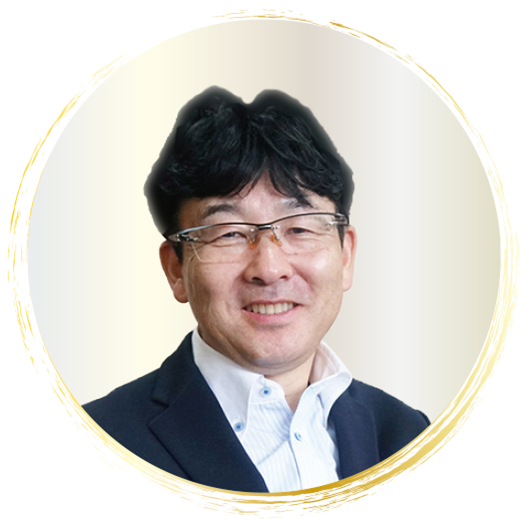
金田氏
そうですね、やはり製造工程に直接関わる部分やお客様からの受発注に関わる分野では独自のシステムが存在しますが、なかなか売上に貢献できないような部分につきましては、エクセル運用になってしまっていることがあると思います。
着任時にはすでに導入を進める段階、現場からの声をきっかけに一念奮起
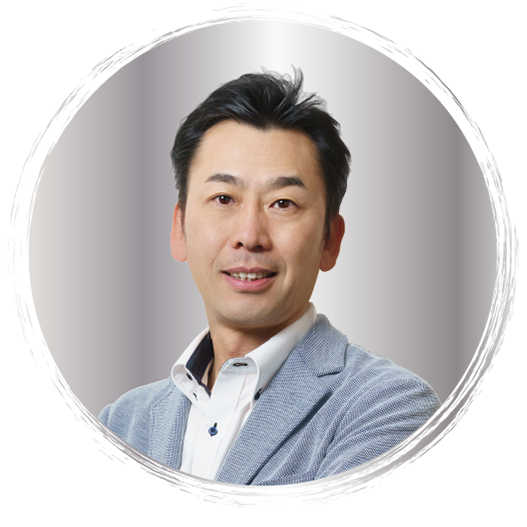
増田
このような課題がありkintoneを導入されましたが、着任時にはすでに導入されていたんですよね。
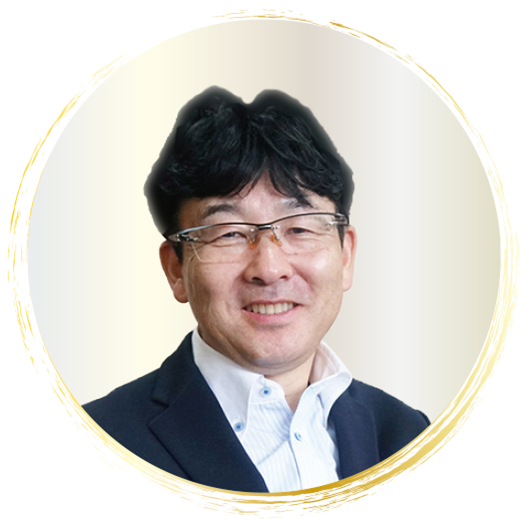
金田氏
そうなんです。前任の総経理がトップダウンで導入を決定し、導入を進める段階でした。
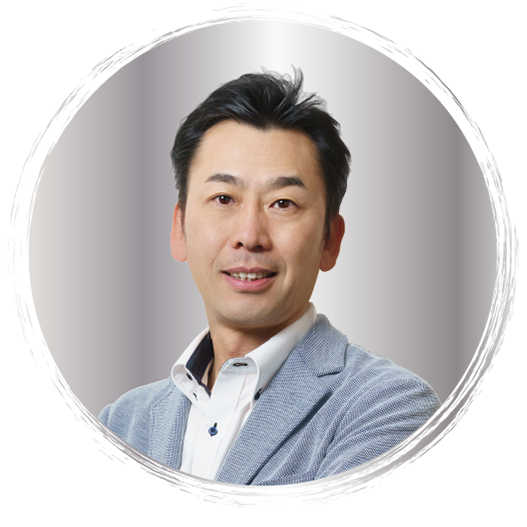
増田
金田さんはそれをみてどういう印象を受けられたのでしょうか?
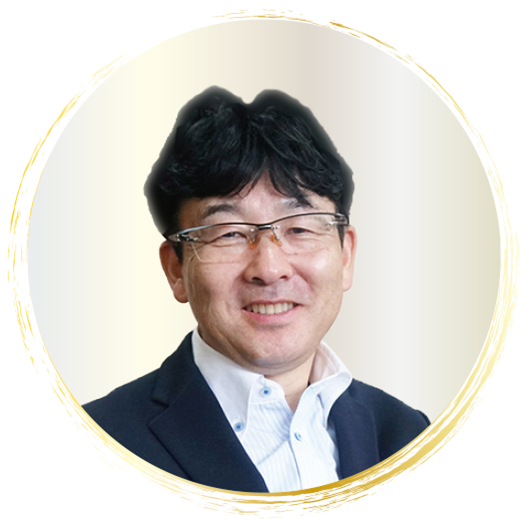
金田氏
日本にいる時に、kintoneのテレビCMをよく見ていまして、カスタマイズできる業務管理システムなのかな、面倒くさいな...という印象が正直ありました。しかし中国のスタッフより、今のエクセル運用では人員削減や間接部門の工数削減に繋がりませんという声が出てきました。そこでもう一度、サイボウズさんに現在問題になっている内容を相談し、改善していこうということで、私自身も勉強しながら現在に至っています。
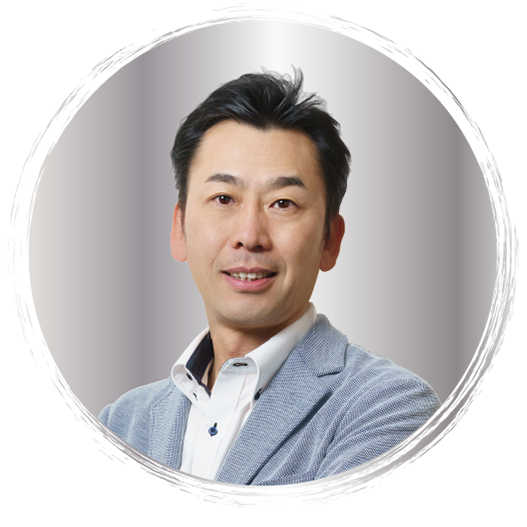
増田
素晴らしいですね。通常、導入したトップが変わると仕組みも定着せずにだんだん使われなくなってしまうことも多いのですが、御社の場合は会社のメンバーからもっと使いこなしたいという意見が上がってきたということですね。素晴らしいです。
それでは早速、実際のkintoneアプリの活用をご紹介いただきます。
それでは早速、実際のkintoneアプリの活用をご紹介いただきます。
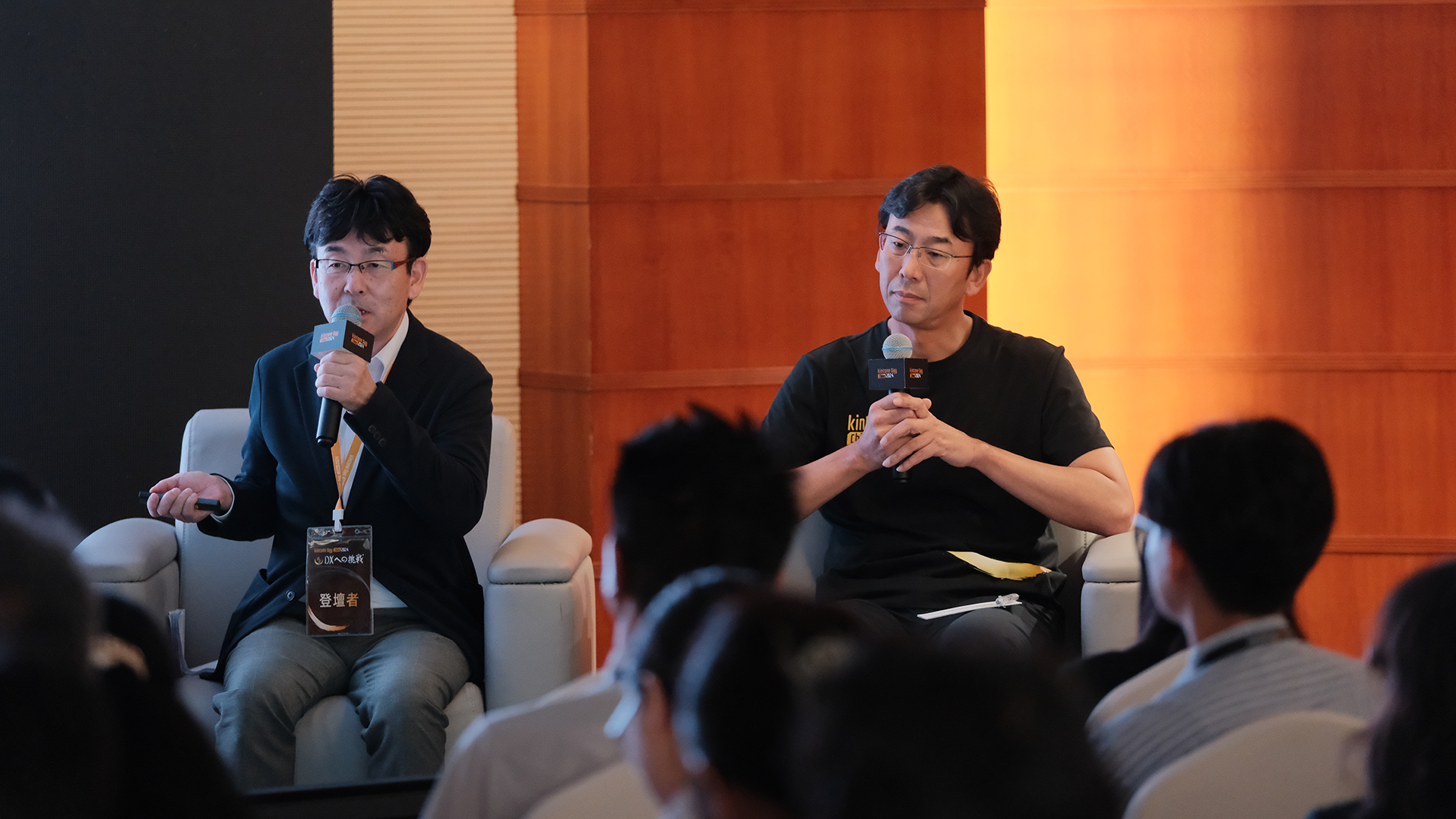
作業員の作業は極力シンプルに、タブレット及びスマホの操作で完結
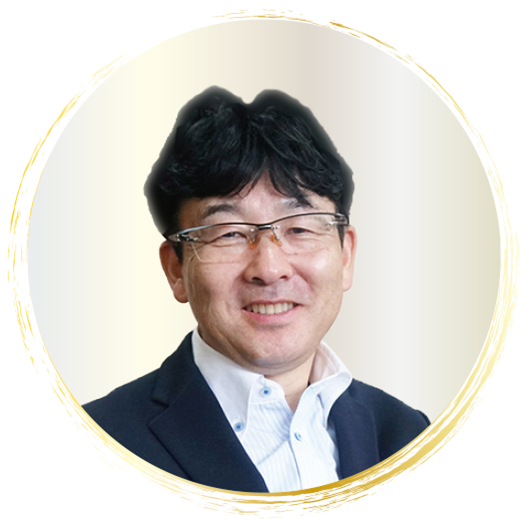
金田氏
まず不良品管理です。kintone導入前は不良品が発生すると、作業員は「赤札」に必要事項を手書きして現物に取り付け、不良品BOXに入れていました。それを品管のメンバーが定期的に巡回して回収し、赤札の内容をエクセルに入力する作業を行なっていました。その際には、読めない字があったりして現場を行ったり来たりして内容確認して入力するというとても煩雑な作業になっていました。毎日16時に不良品の対策会議を開催しているのですが、エクセルをまとめるのに時間がかかってしまい、開催時間の遅延が頻繁に起こっていました。
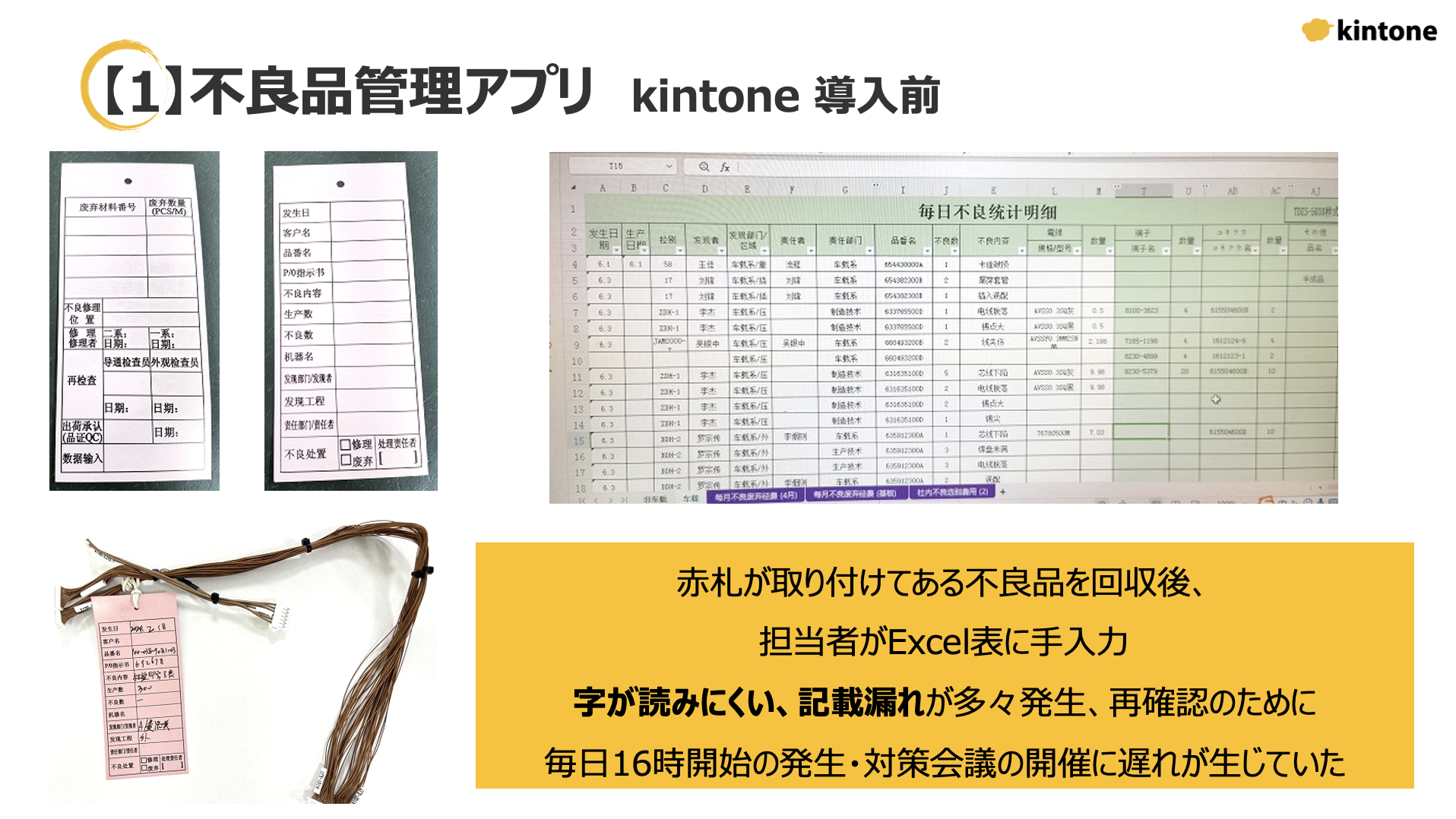
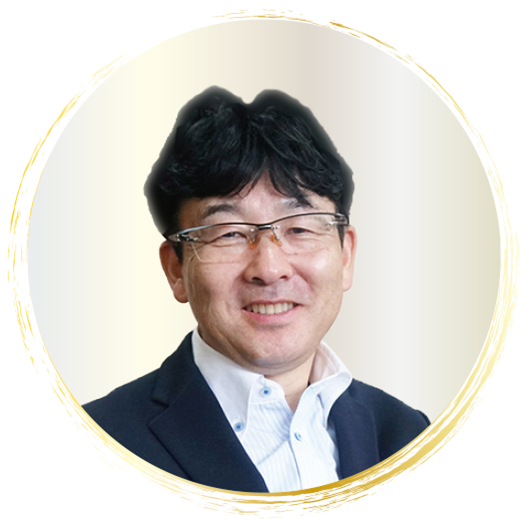
金田氏
不良品が発生すると、作業員はラインナンバーを入力、生産品、作業者番号、生産工程を選択して入力します。あと、異常が出た設備名を選択し、不良内容の選択、不良数を入力し、最後に保存ボタンを押します。これで登録は完了し、kintoneに情報が入ります。
そしてアプリの管理番号を白テープに手書きし、不良品の現物に貼ります。これを赤箱に入れます。作業員の作業は以上です。
そしてアプリの管理番号を白テープに手書きし、不良品の現物に貼ります。これを赤箱に入れます。作業員の作業は以上です。
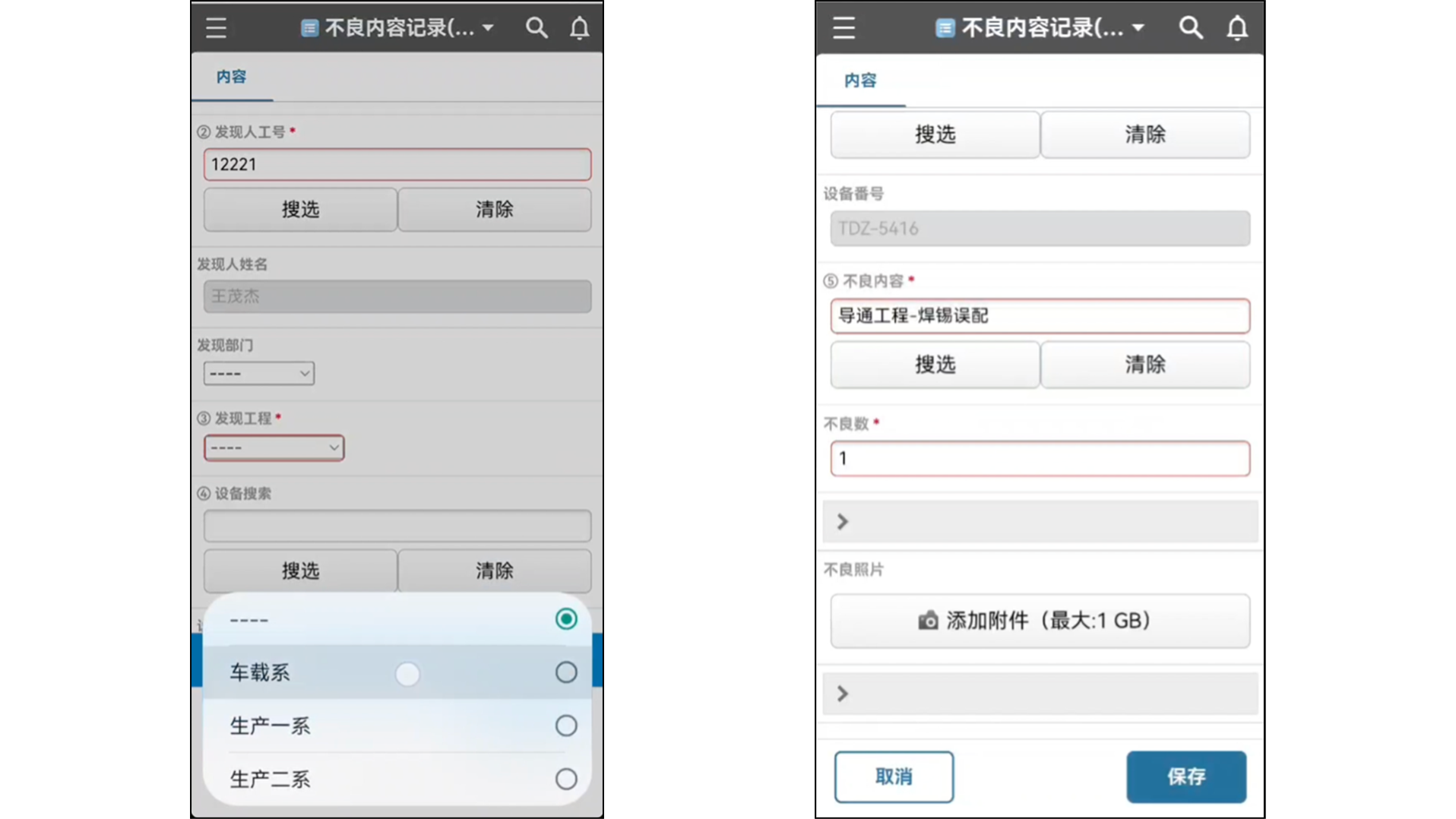
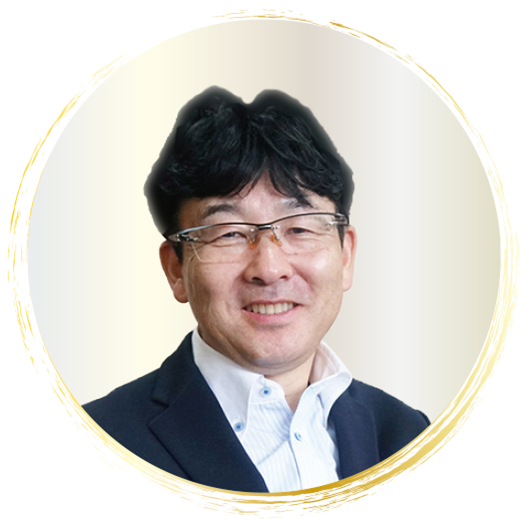
金田氏
品管のメンバーは巡回の際に不良品を回収し、白テープとアプリの管理番号を突き合わせるだけとなりましたので、16時開始の不良品対策会議は時間通りに毎日開催できるようになりました。
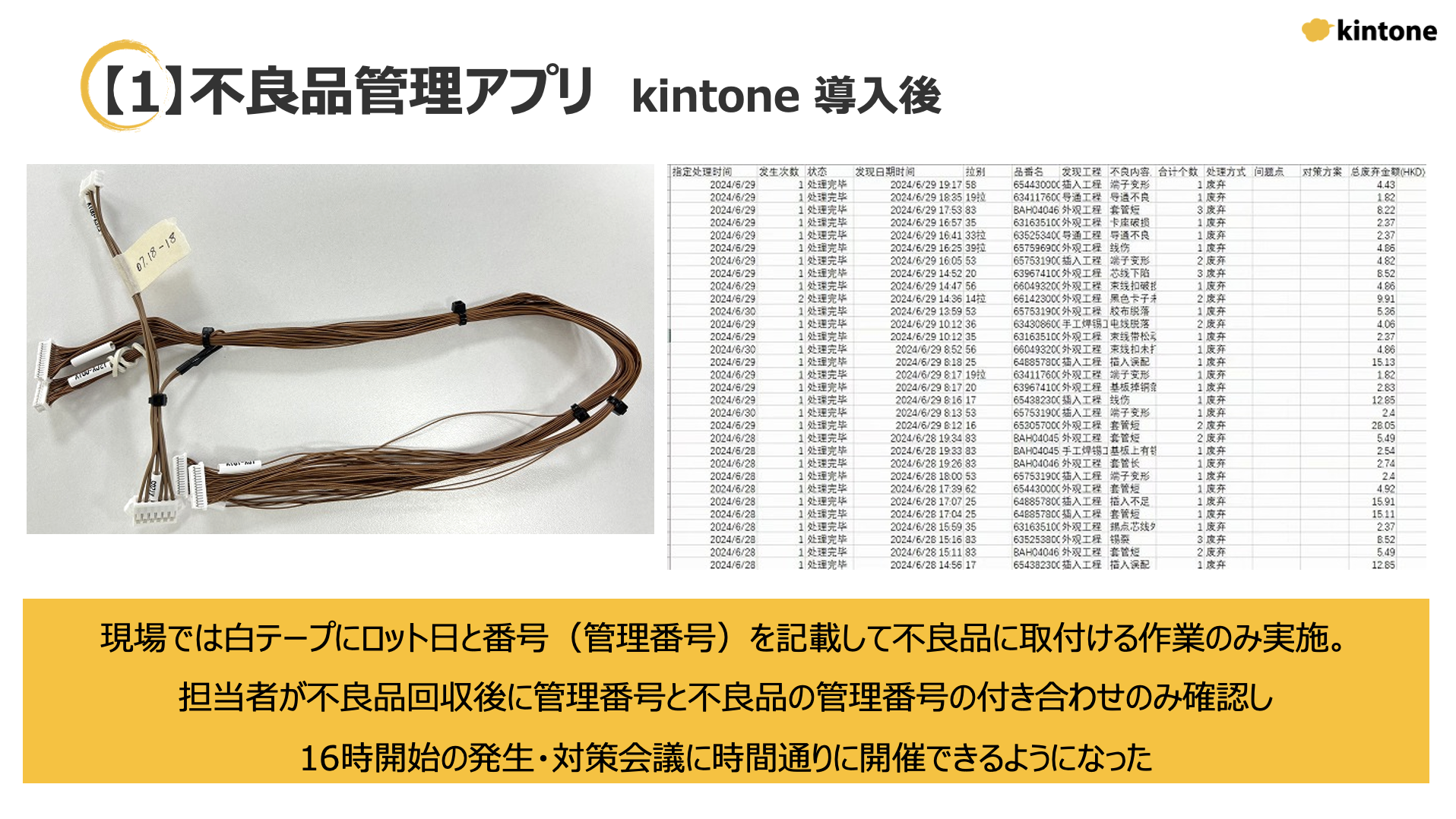
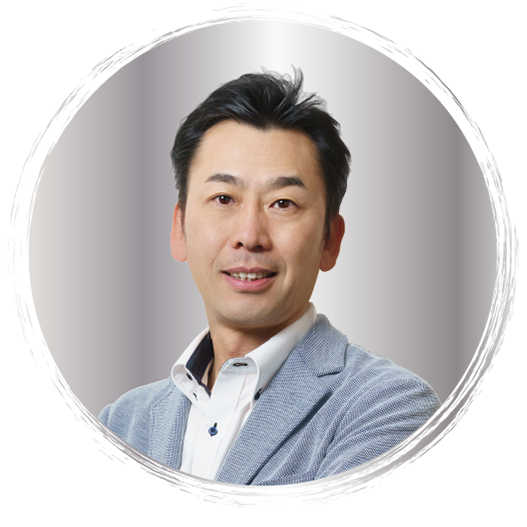
増田
やはり御社では優先順位が高く、日々の業務の中で現場が疲弊していた内容だったのですか?
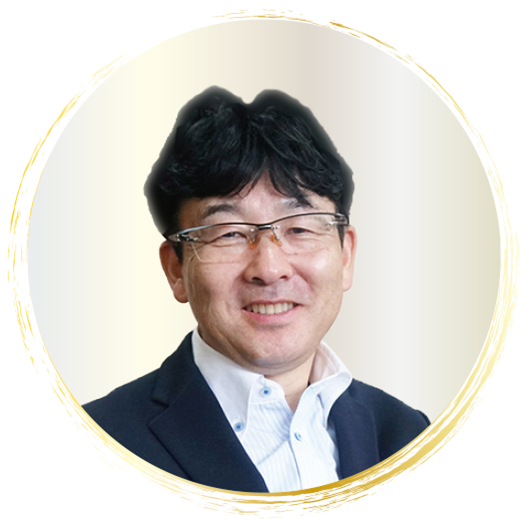
金田氏
そうですね。弊社では派遣社員の方も多くいらっしゃいますので、入社されたばかりの方ですと不良品を出しますので品管の負担がかかっておりました。
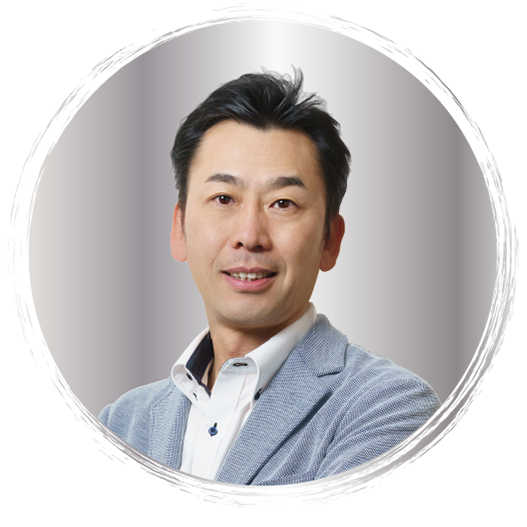
増田
kintoneを導入して不良が減ったというところまではいかないですか?
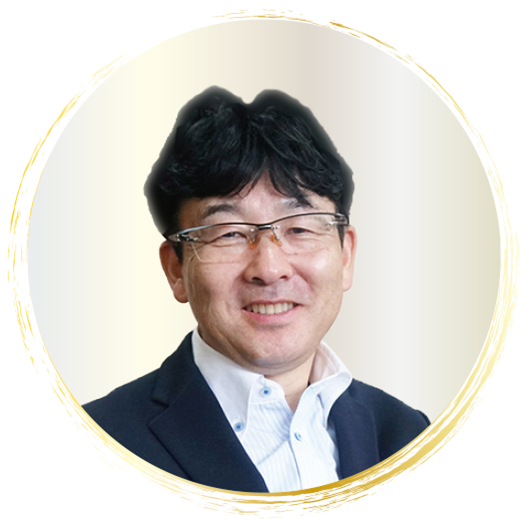
金田氏
不良も減っています。なぜなら、毎日の不良品対策会議を遅延なくタイムリーに開催できるようになったことで、設備に原因があるのか、人に原因があるのか、原因を速やかに共有し、対策を立てることができるようになりました。よって、若干ではありますが不良数減に繋がっています。
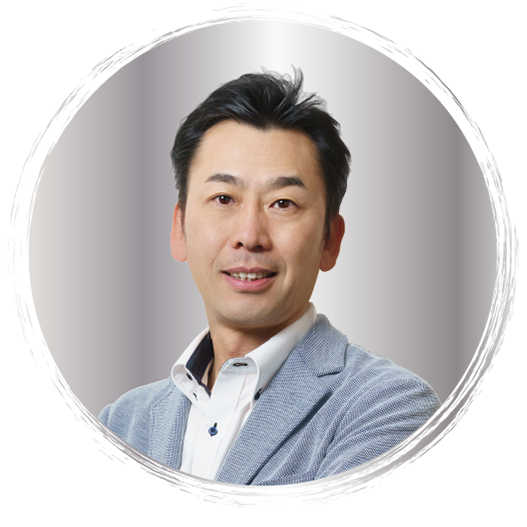
増田
なるほど、ありがとうございます。それでは二つ目のアプリをご紹介いただけますでしょうか。
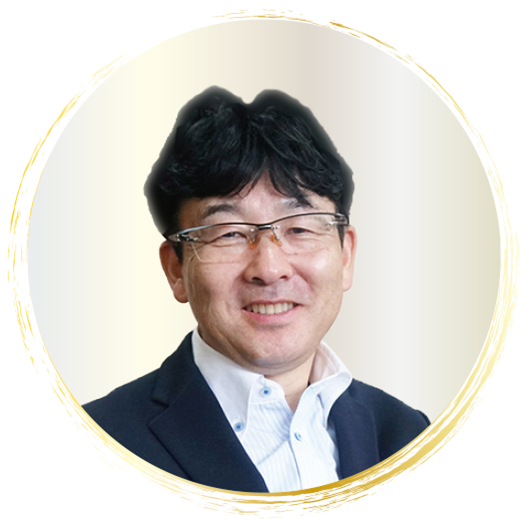
金田氏
5S管理アプリをご紹介します。導入前は週二回の巡回パトロールでは、問題点を写真に撮ってWeChatで総務へ個別送信していました。その届いたメッセージを総務メンバーがエクセルにまとめる作業を行なっていましたが、写真の容量が大きかったり、コメントがわかりづらく確認対応が必要になったりしていたので、5S一覧表を作るのに一日がかりで作成していました。

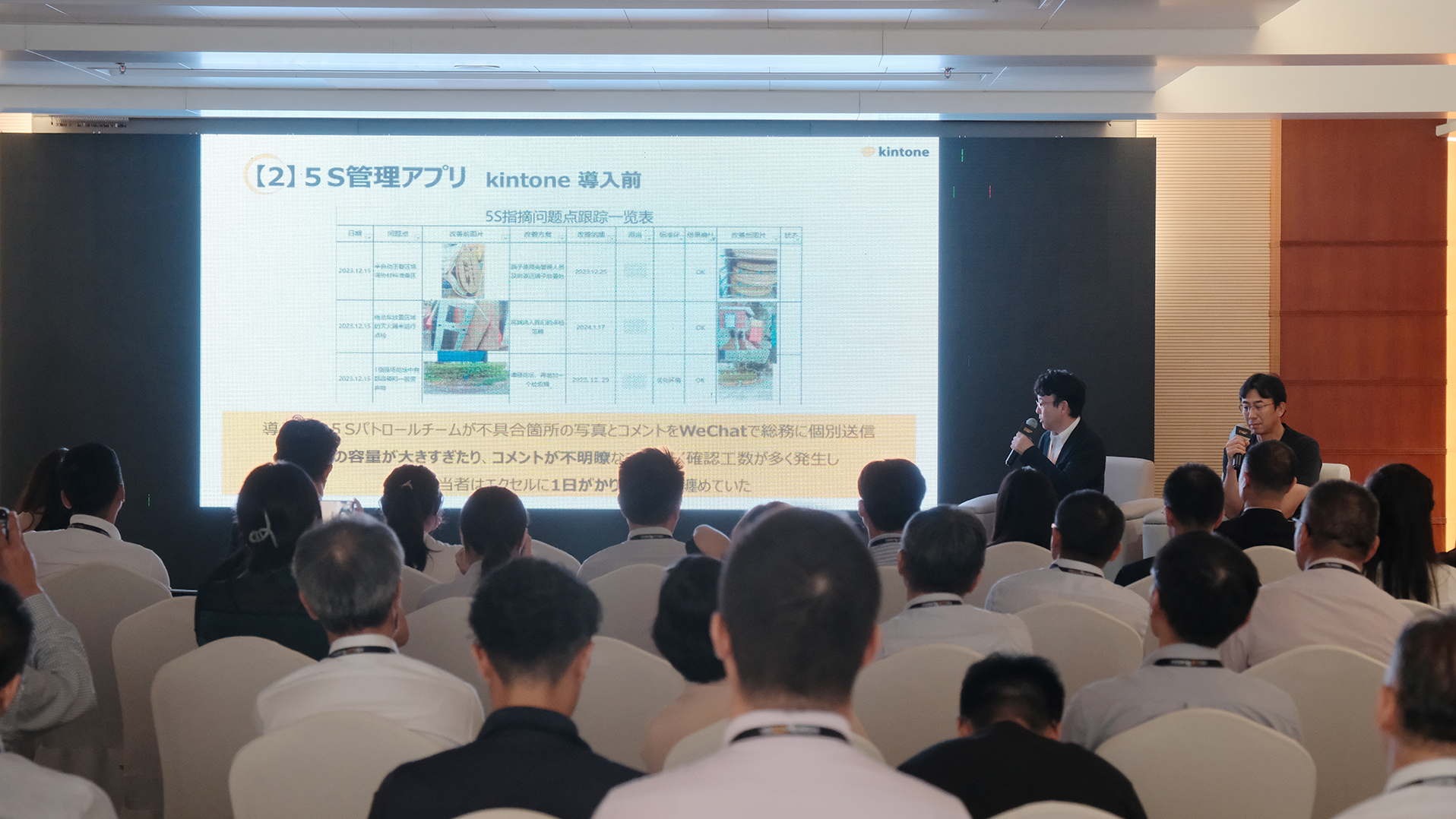
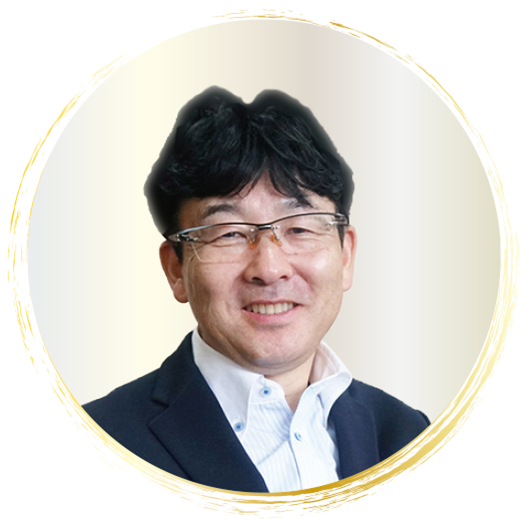
金田氏
それで5S管理アプリを導入しまして、登録はスマートフォンでできるようになりました。まず指摘者の流れです。作業者番号、巡回する生産部署、問題点を入力します。そして問題箇所の写真を撮影し、アップします。その後、完成を選択して保存します。これだけです。
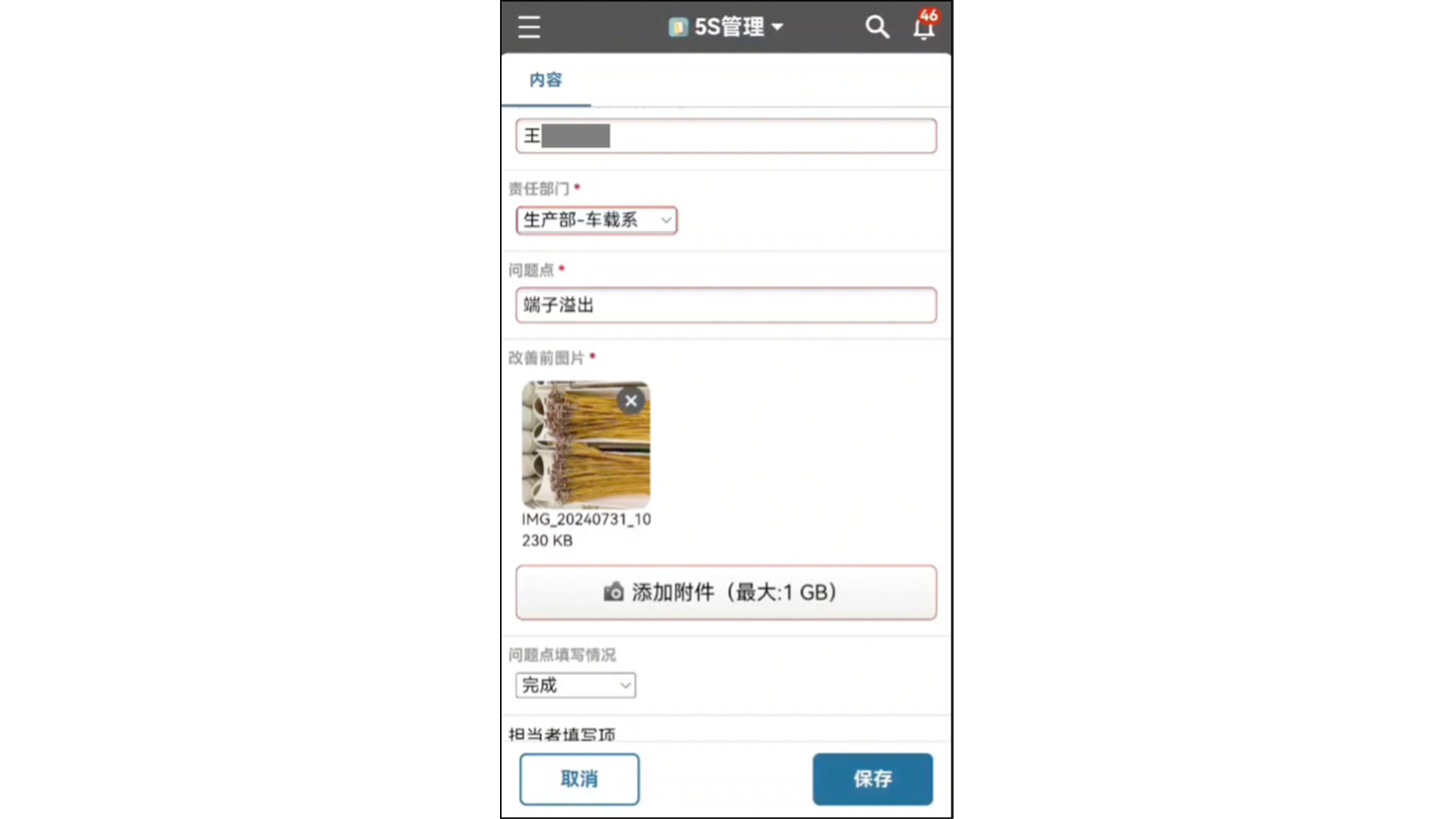
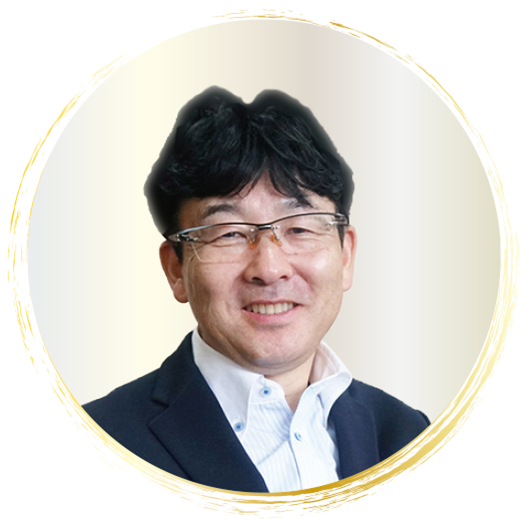
金田氏
そして次は指摘された部門です。未処理リストで該当のレコードを選択し、改善予定日と完了予定日を選択します。もし改善が終わっていれば、改善後の写真をアップします。そして最後に完成を選択して保存します。
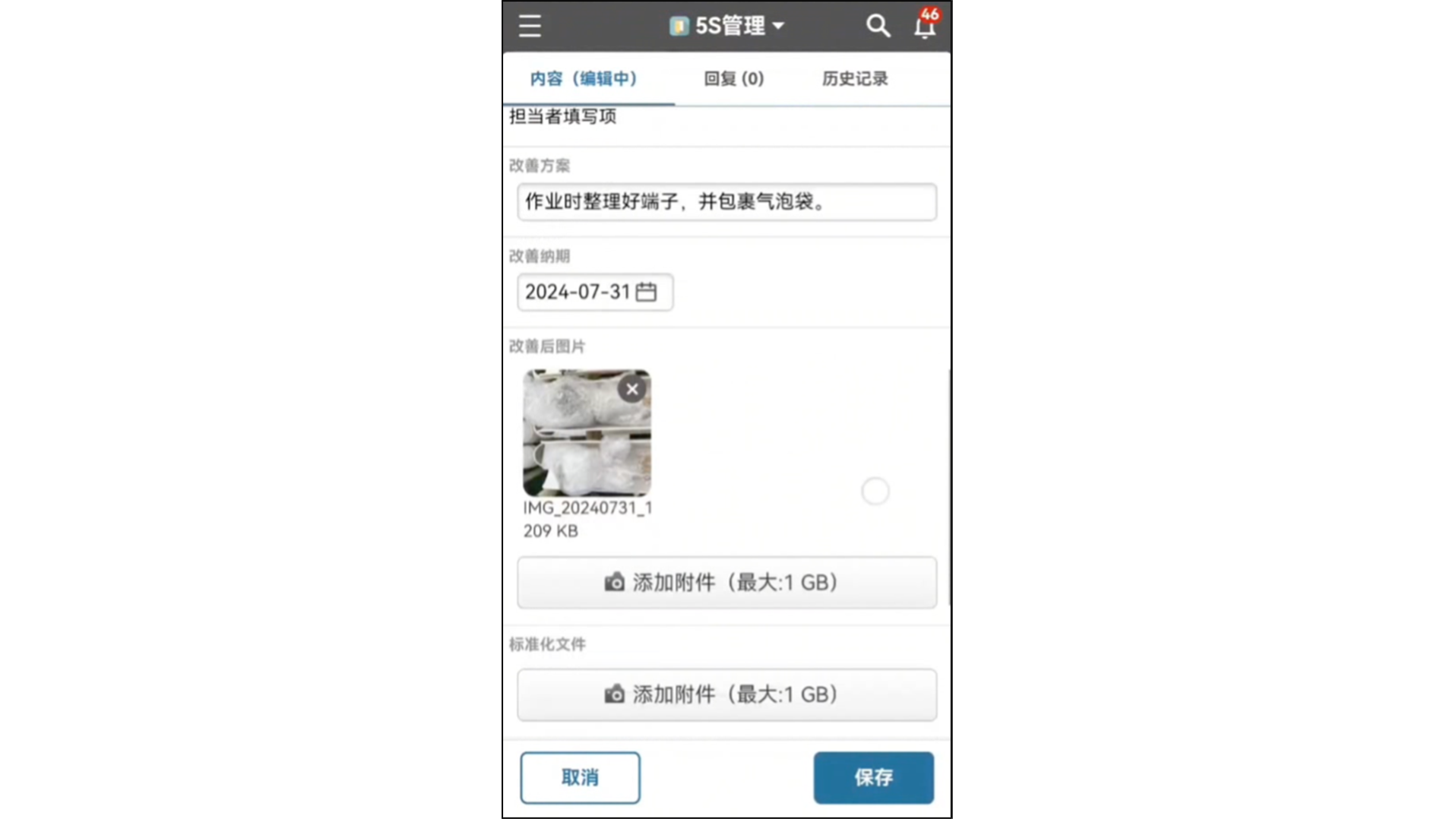
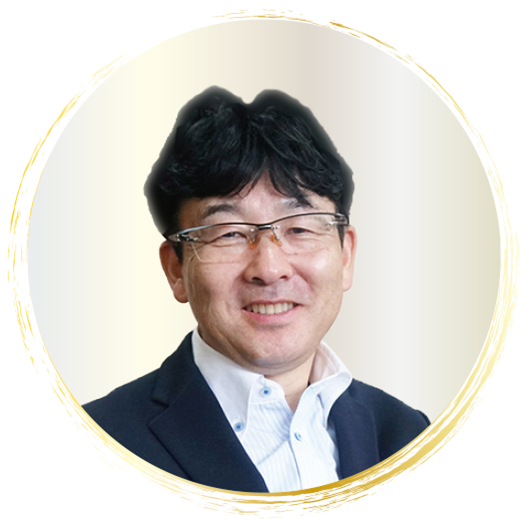
金田氏
最後に総務部門の最終チェックです。同じように未処理リストで該当のレコードを選択し、指摘された内容と写真、改善された内容を現場に行って確認します。そこで問題がなければ実行をクリックし、フローが完了となります。
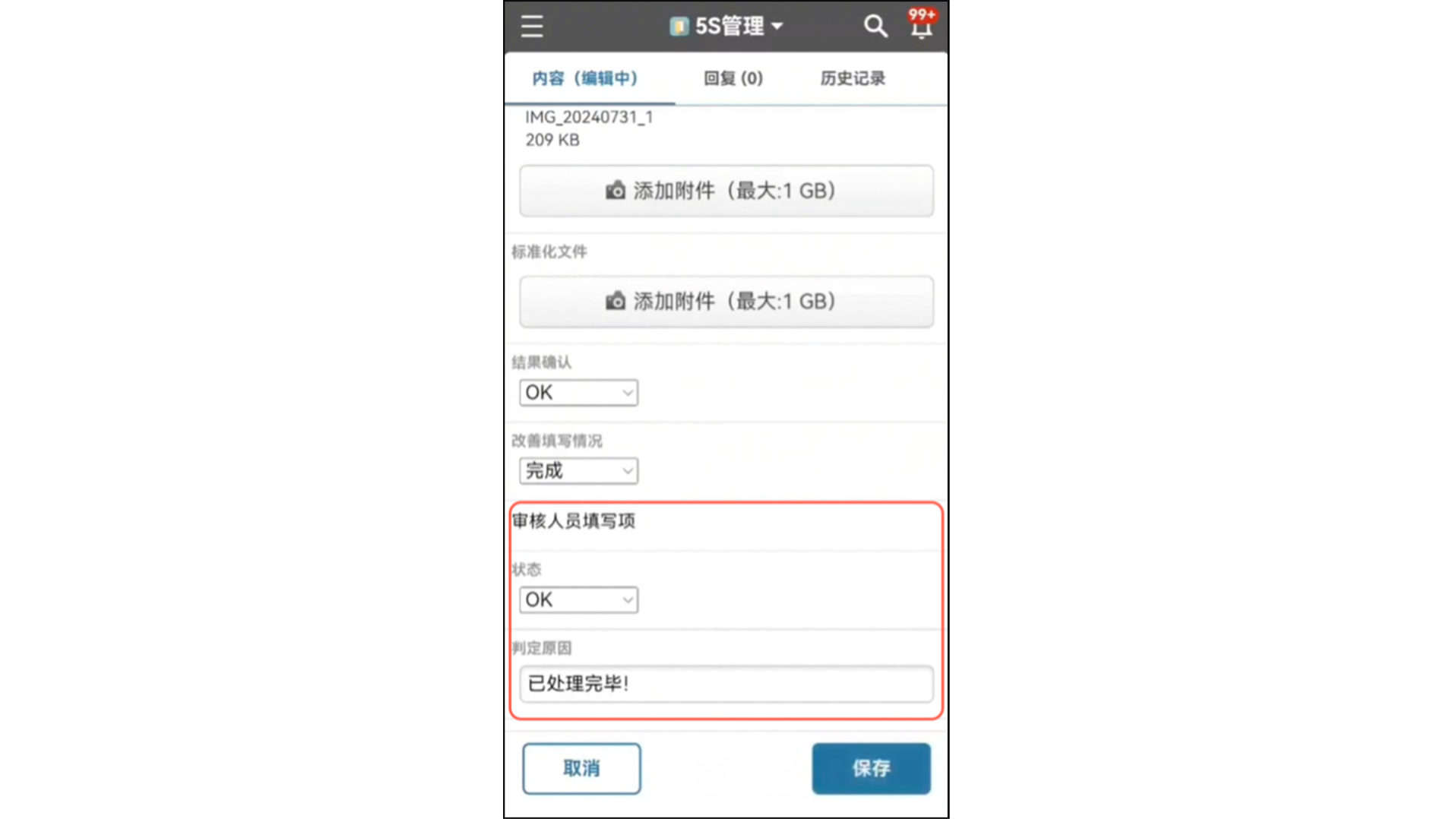
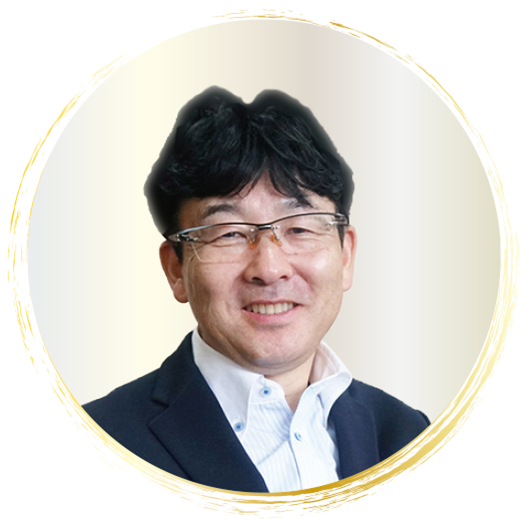
金田氏
結果、導入前は指摘事項や改善報告を即時に共有できなかったのですが、現在は総務課のエクセル取りまとめ作業もなくなり、情報をタイムリーに共有できるようになりました。指摘された部署も改善計画を速やかに実行することができるようになりましたし、総務課は最終の合否判定をするだけになりましたので、大変だった情報を取りまとめる作業がなくなって他の業務に時間を設けることができるようになりました。
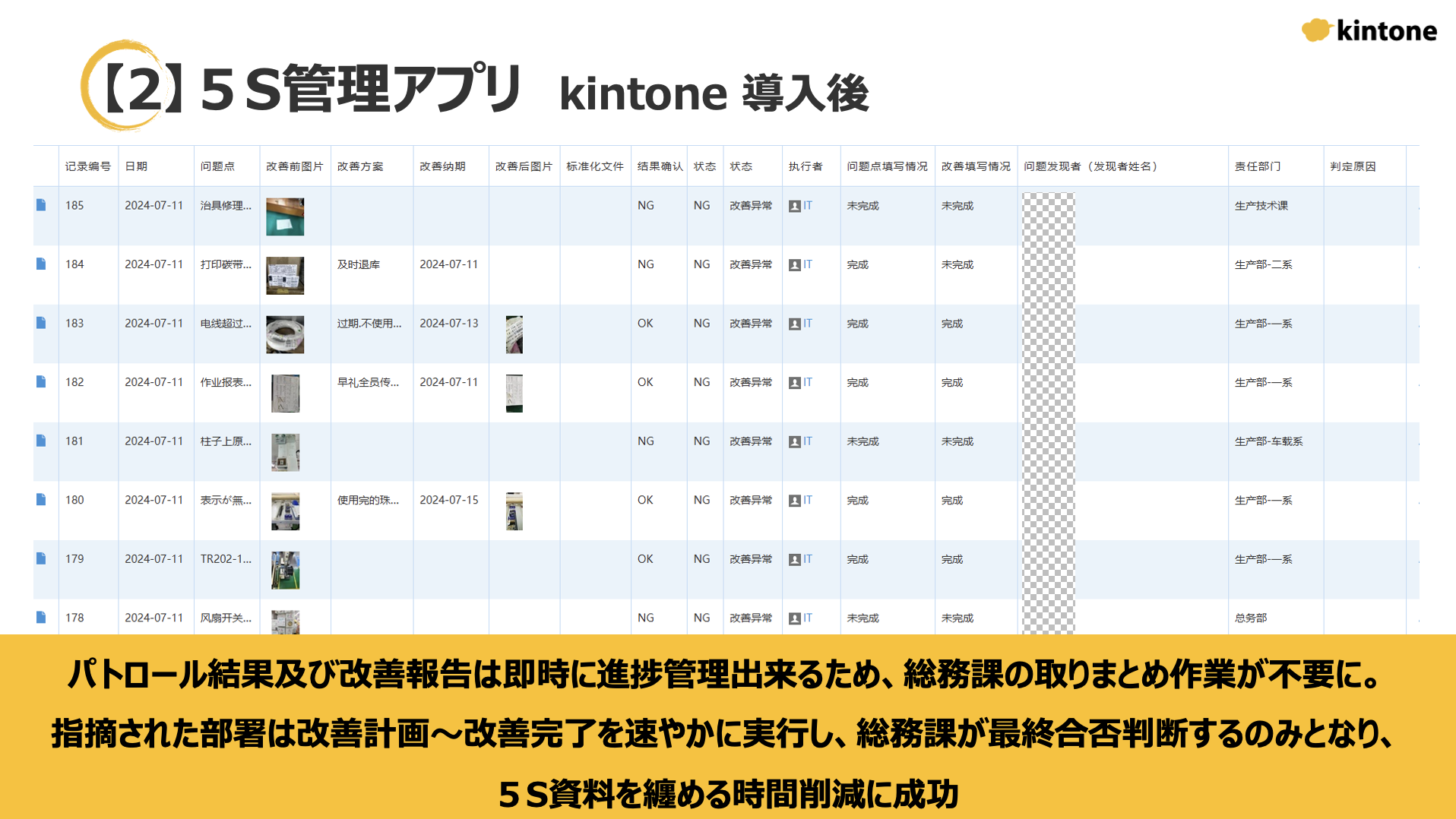
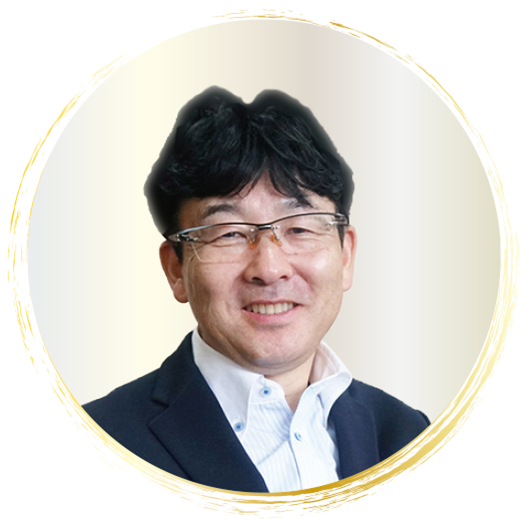
金田氏
続けて、圧着金型ショット数管理をご紹介します。これまでは手書きで何ショット打ったかを紙に書き、それをエクセルに転記して管理していました。設備が30数台ありまして、1台で4~5回使うこともありますので管理表だけで一日に40枚程度出ることがあり、この作業を専属で一名配置して行なっていました。
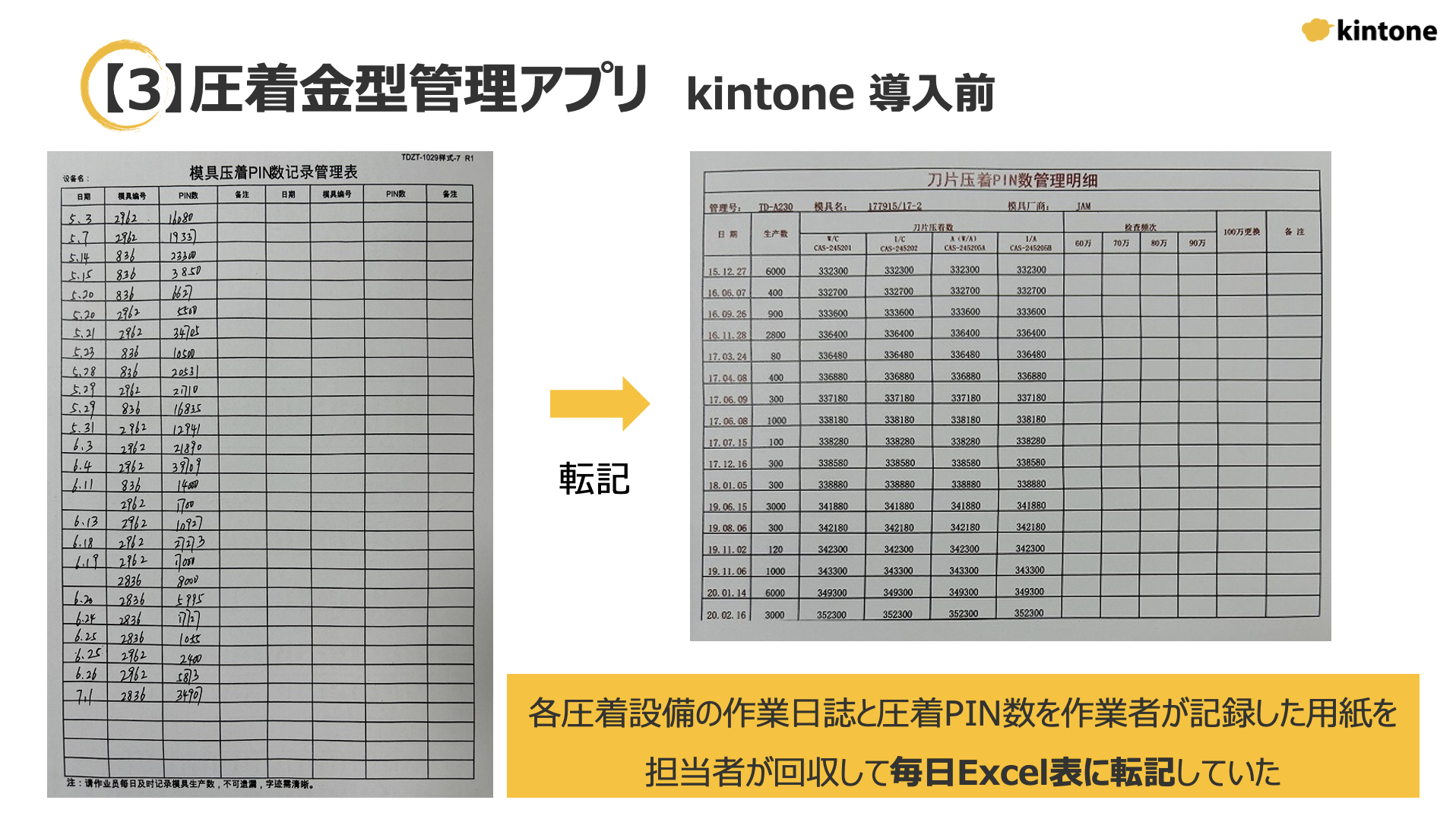
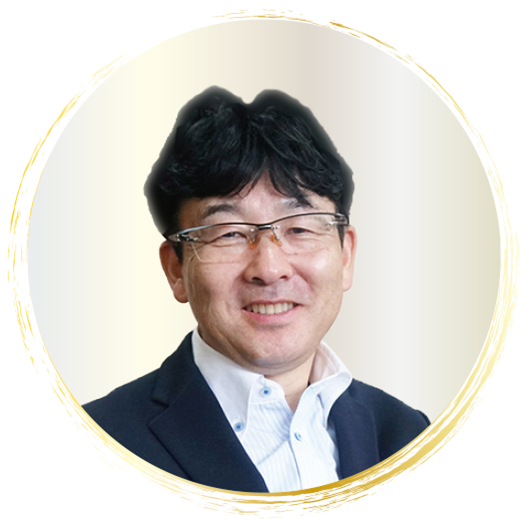
金田氏
それがアプリを導入して非常に簡単になりました。作業者は金型の管理番号、打ったショット数を登録するだけで完了です。
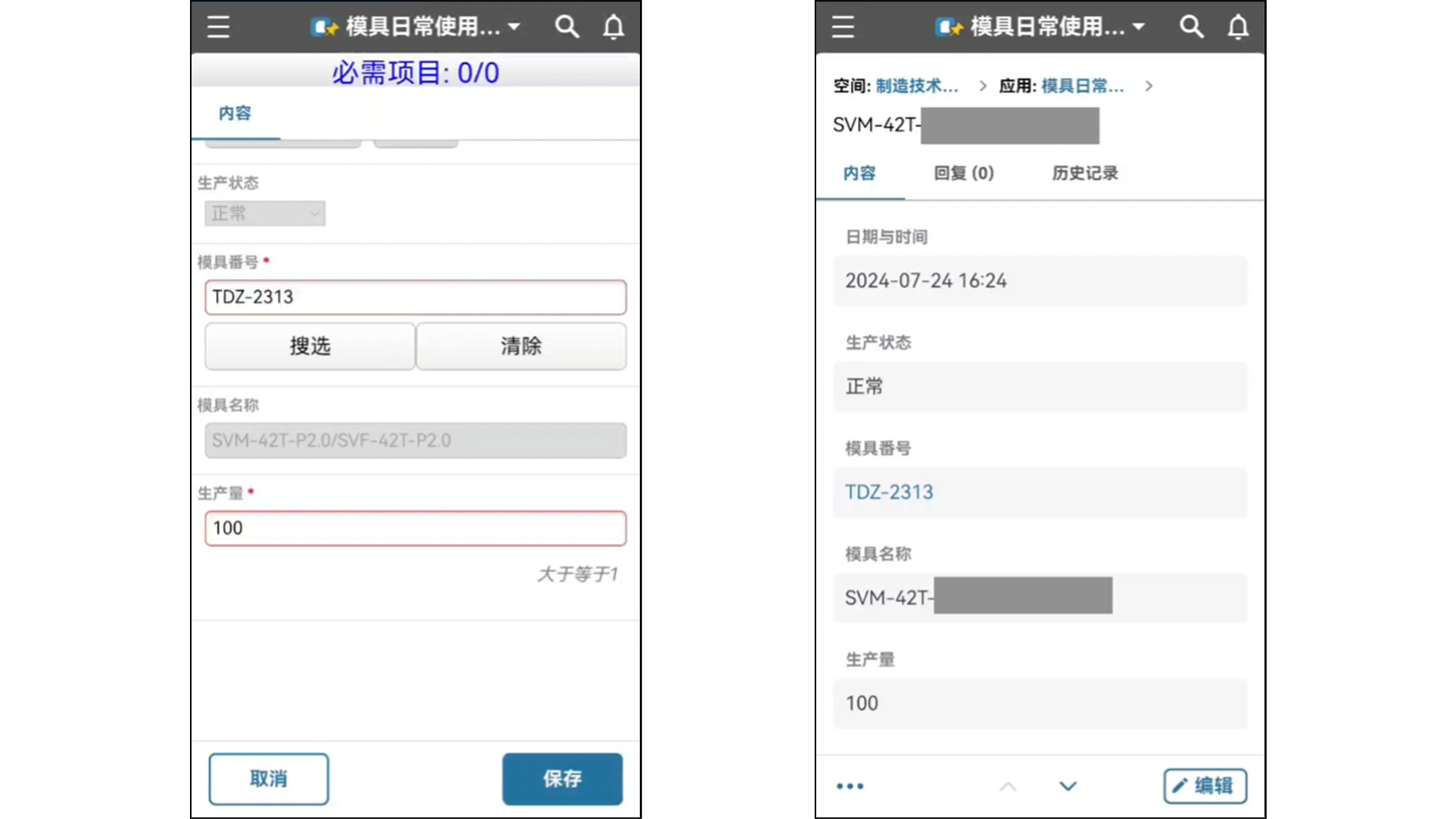
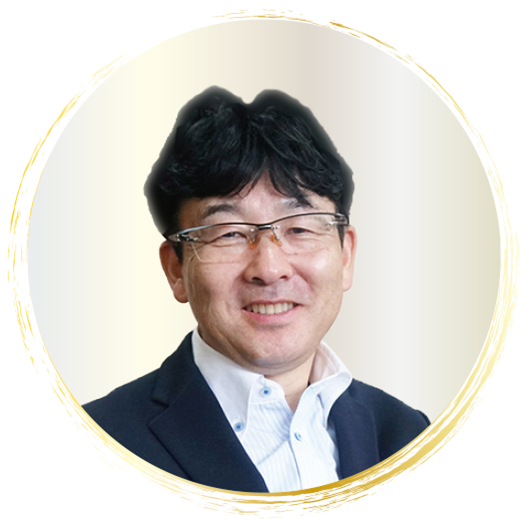
金田氏
導入後はエクセル転記をしていた作業員の工数がなくなりました。また、金型については半永久に使えるものではありませんので、60万ショット打ったら黄色のアラームが出るように設定しました。そのアラームが出ましたら、アプリで管理番号を確認し、刀型の摩耗チェックを行って管理をしています。100万ショットを打った時点で、無条件で刀型の交換を行います。
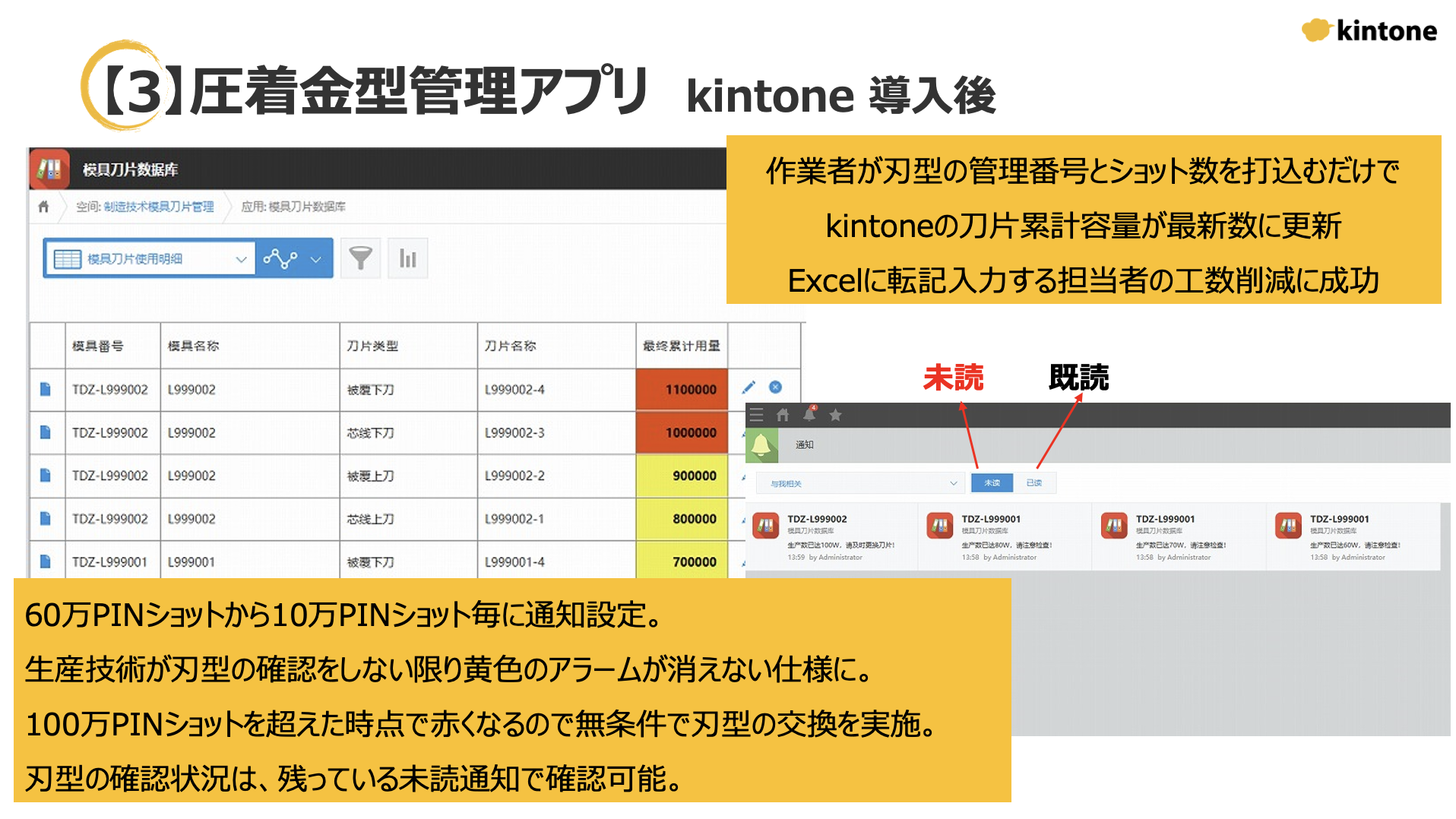
まずは話を聞く。推進担当者のモチベーションを保つ工夫とは
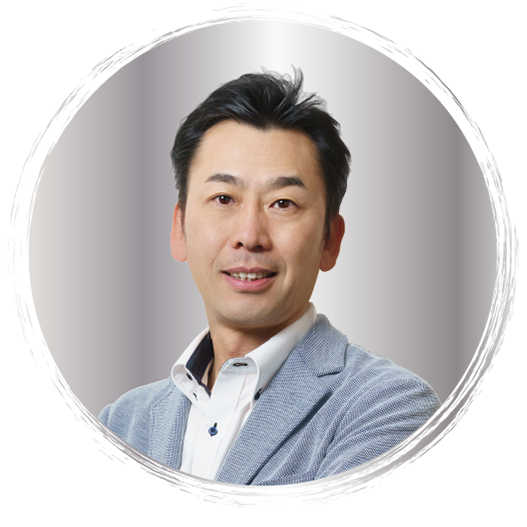
増田
非常にわかりやすい説明をありがとうございます。御社はこれらの開発を社内の担当者の方が対応されているのでしょうか?
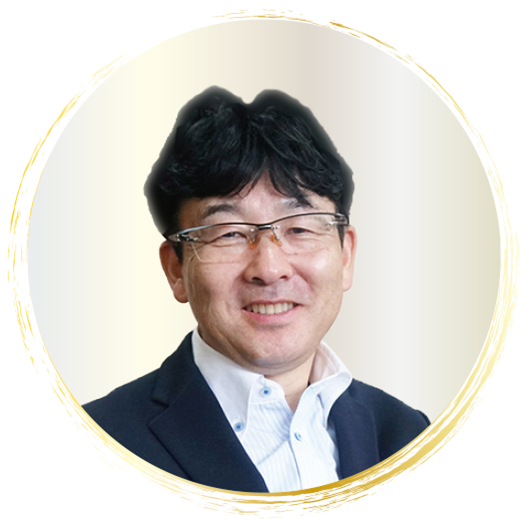
金田氏
はい、そうです。通常は技術が専門で、CADを使って図面を作成している社員です。彼をkintone担当に選任し、サイボウズさんと連絡をとりながら進めてもらっています。彼に作業員の教育も担当してもらっています。
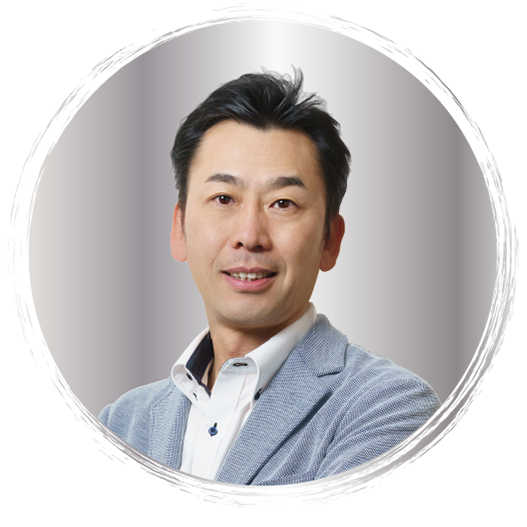
増田
まさに現場主導でどんどん業務改善が進んでいっている印象を受けます。中国ではジョブスクリプションがきっちり決まっていて、周りを巻き込んで仕事をするというのがあまり得意ではない印象を持っているのですが、その担当者にはどのようにモチベーションを保っていただいたのでしょうか。工夫があれば教えていただきたいです。
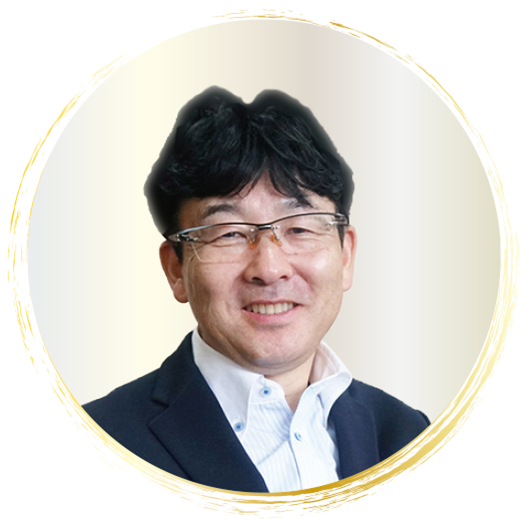
金田氏
副総経理と彼と面談を行い、まず彼の話を聞きました。やはり非常に大変だということで、アプリを構築するためにはマスタ作成を行わないといけないが、その作業がとても大変だという話でした。そこで労いの言葉をかけ、彼を評価しているということを伝え、給与もアップさせました。
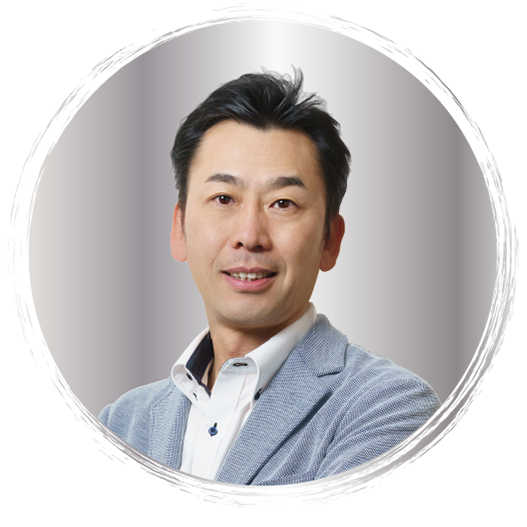
増田
ありがとうございます。まさにDX人材育成ですね。では導入効果について聞かせていただけますでしょうか。
大幅な時間削減に成功!効果金額はなんと年換算で14万元弱に
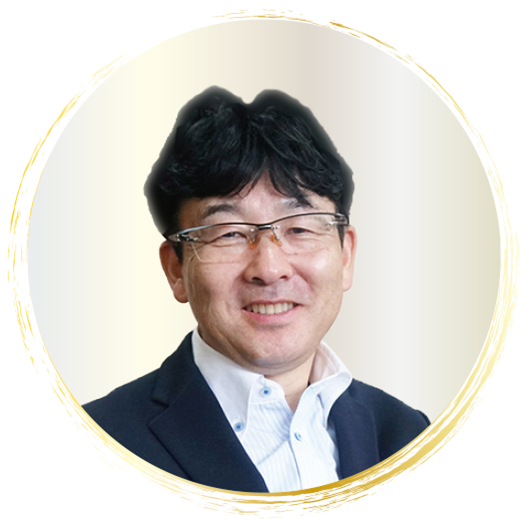
金田氏
工程内不良がこれまで一日5時間かかっていたのが20分に。5S管理は一日かかっていたのが0に。そして金型管理は一日かかっていたのが90分と大幅に時間削減できました。効果金額にすると14万元弱の効果となります。
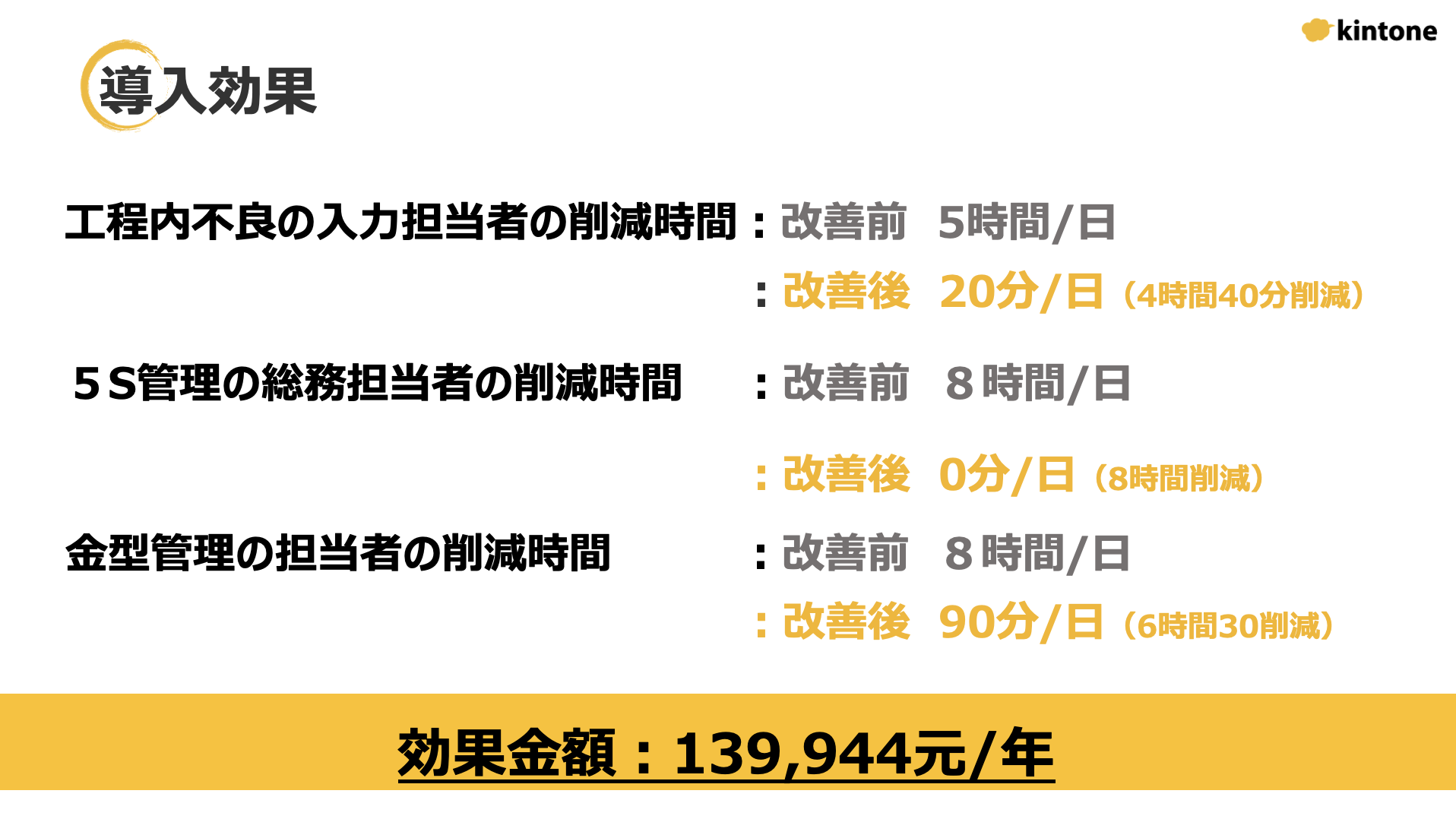
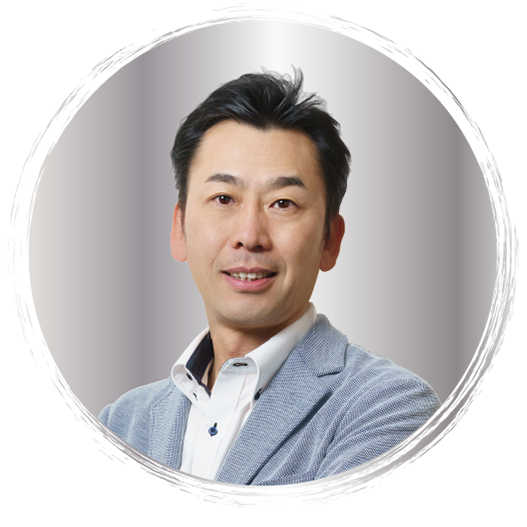
増田
すごいです。そしてさらなる展望があるとのことですね。
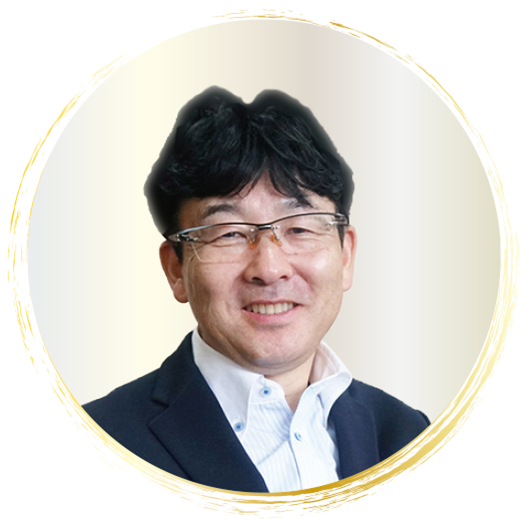
金田氏
はい。まずは設備メンテナンスの分野、そして作業日報の分野に着手したいと考えています。現在作業日報は手書きで管理していますが、やはり人によってはなかなか読みづらいことが多数あります。このような分野はお金を生みませんので、どんどん業務改善してトレーサビリティを取れるようにしていきたいと考えています。
また、現在の東莞モデルを他拠点の工場に展開していきたいです。弊社タイ工場でkintoneの導入を検討しておりまして、やはり手書き作業が多いようですので、kintoneで業務改善に取り組んでいきたいです。
また、現在の東莞モデルを他拠点の工場に展開していきたいです。弊社タイ工場でkintoneの導入を検討しておりまして、やはり手書き作業が多いようですので、kintoneで業務改善に取り組んでいきたいです。
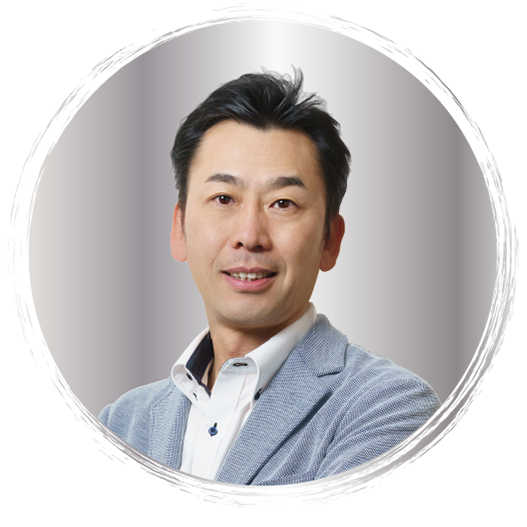
増田
ありがとうございます。弊社タイのメンバーに共有しておりますので、しっかりとご支援させていただきます。
以上で金田様との対談は以上となります。素晴らしい事例をありがとうございました。
以上で金田様との対談は以上となります。素晴らしい事例をありがとうございました。