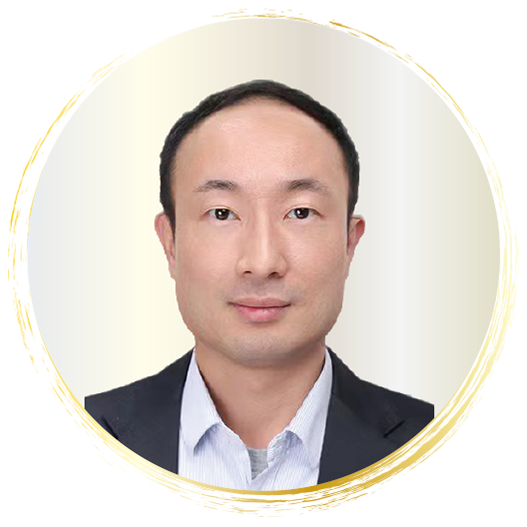
大山氏
富士ファイン電線の大山と申します。本日はよろしくお願いいたします。
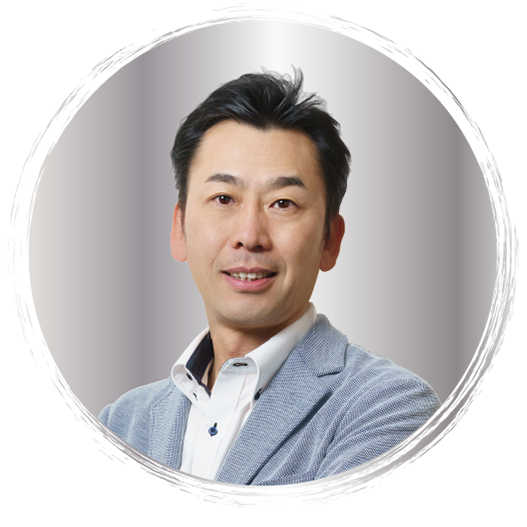
サイボウズ増田
(以下、増田)
(以下、増田)
よろしくお願いいたします。早速ですが、自己紹介と会社紹介をお願いいたします。
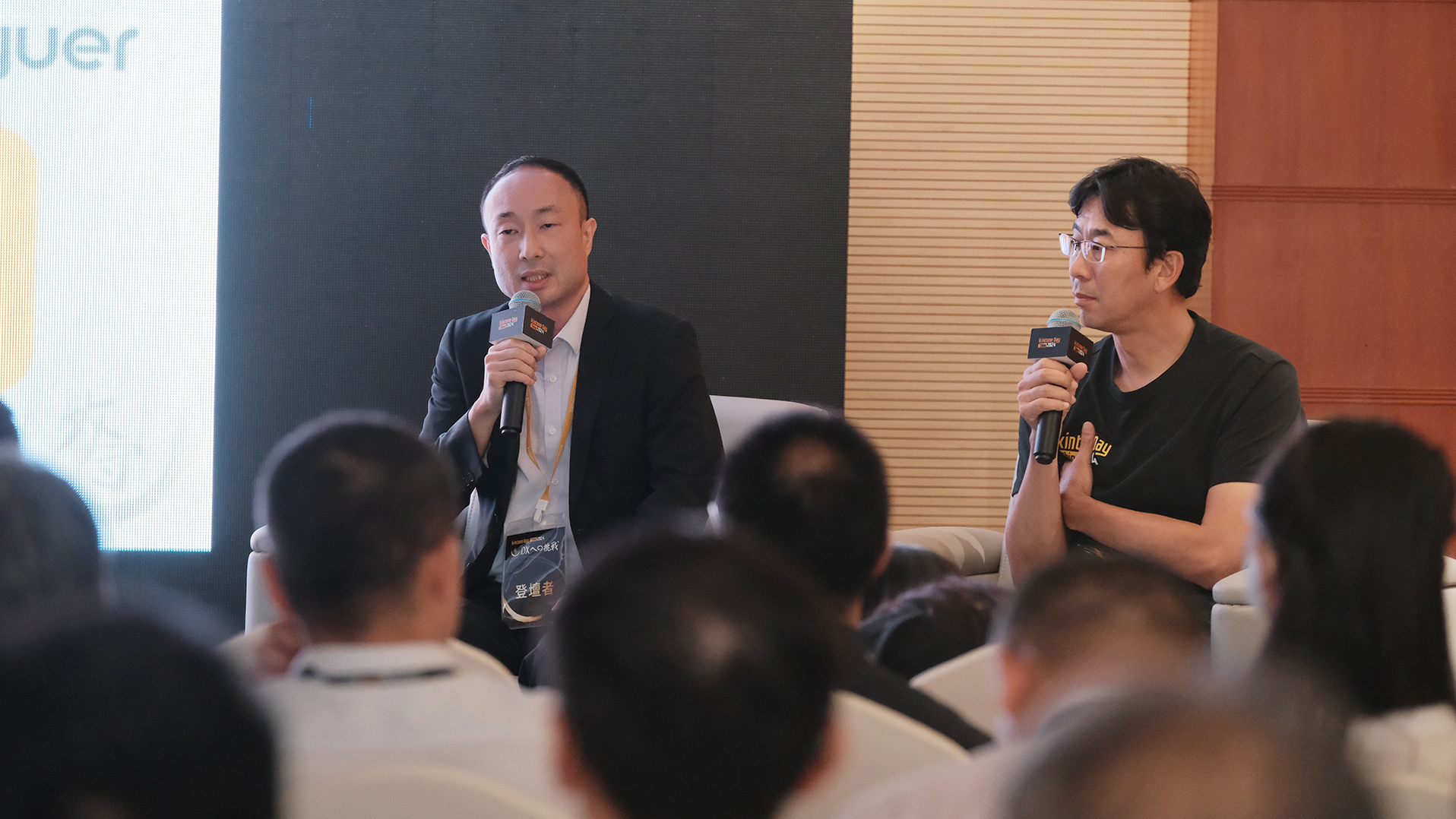
世界トップクラスの超極細電線製造企業、富士ファイン
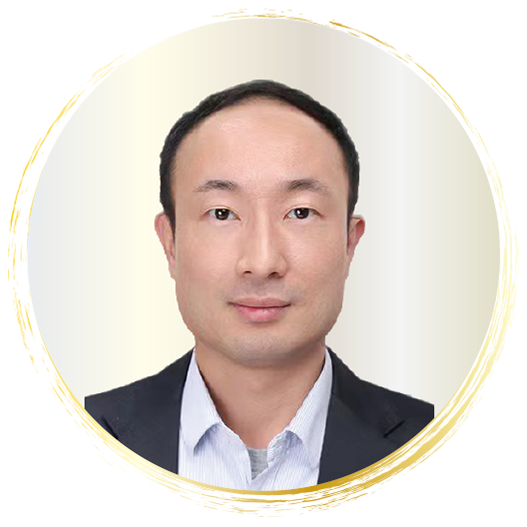
大山氏
簡単に自己紹介させていただきます。富士ファイン深圳の大山と申します。日本でソリューション営業を経験しまして、2019年に富士ファイン深圳に入社しました。そして今年現地中国人女性と結婚いたしまして、両足を中国に踏み入れました。
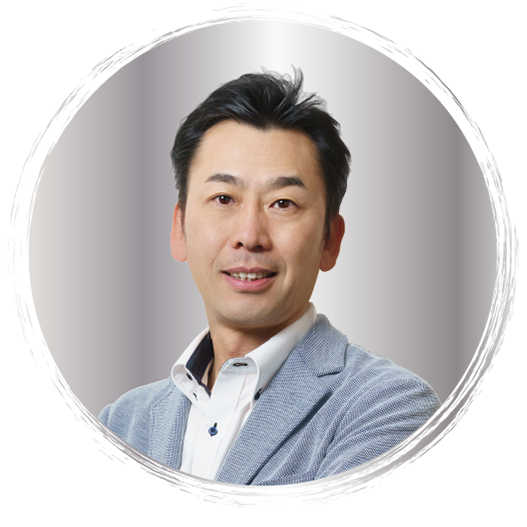
増田
おめでとうございます!!
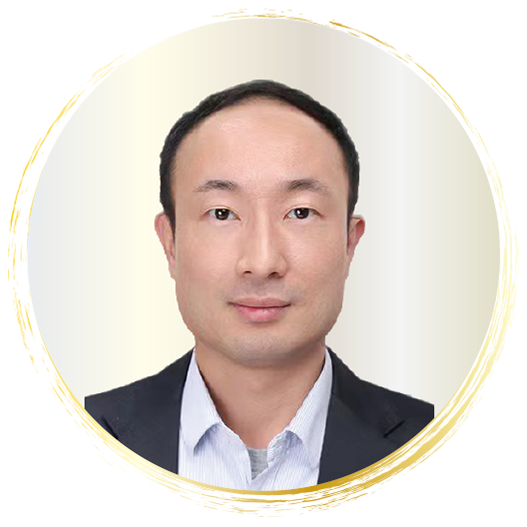
大山氏
ありがとうございます。そして事業紹介です。大きく三つの事業を行なっております。一つ目は、マグネットワイヤー製造です。細い銅線の表面に絶縁の皮膜を施したものになります。世界トップクラスの超極細電線を製造する企業でして、製造拠点は日本と大連です。
二つ目は各種電子部品を製造しています。電線からコイルまでの生産を一貫して行なっています。こちらは大連で製造しています。
そして三つ目は、現在私が所属しております撚線事業です。深圳と大連で製造しておりまして、電線から撚線、各種被膜加工までの生産を自社で一貫しております。もし何かございましたら、お気軽に弊社へご相談ください。
二つ目は各種電子部品を製造しています。電線からコイルまでの生産を一貫して行なっています。こちらは大連で製造しています。
そして三つ目は、現在私が所属しております撚線事業です。深圳と大連で製造しておりまして、電線から撚線、各種被膜加工までの生産を自社で一貫しております。もし何かございましたら、お気軽に弊社へご相談ください。
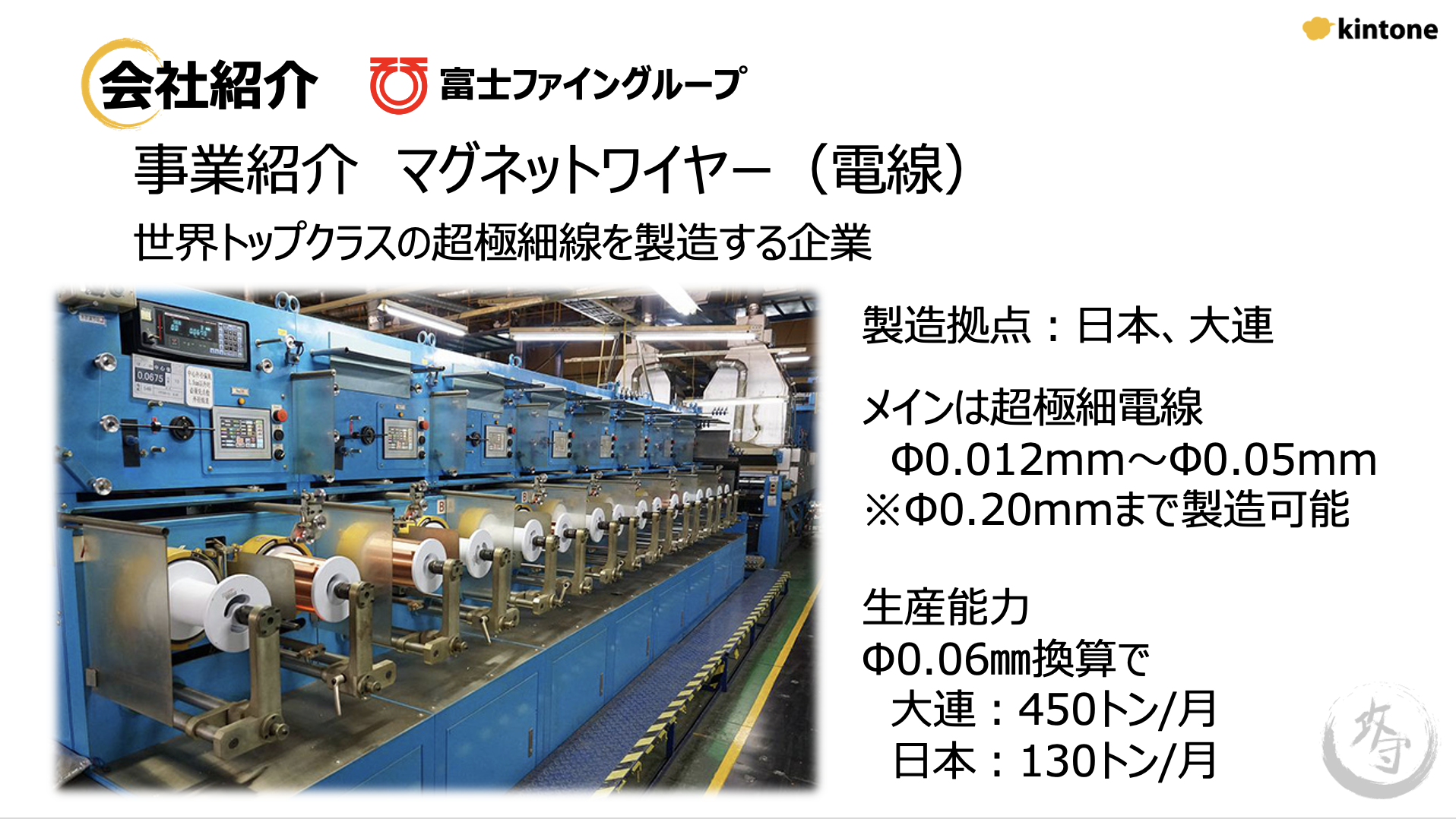
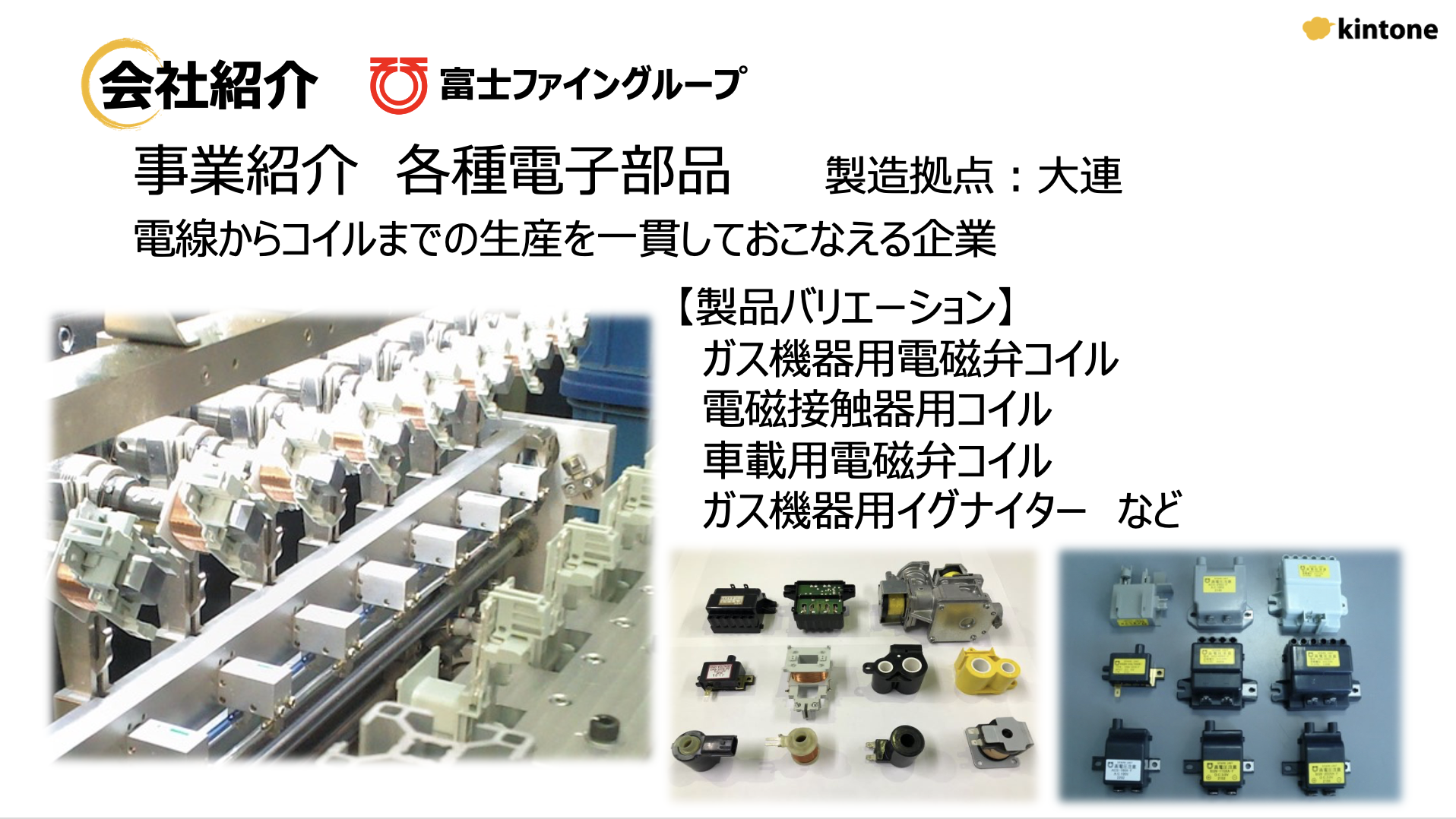
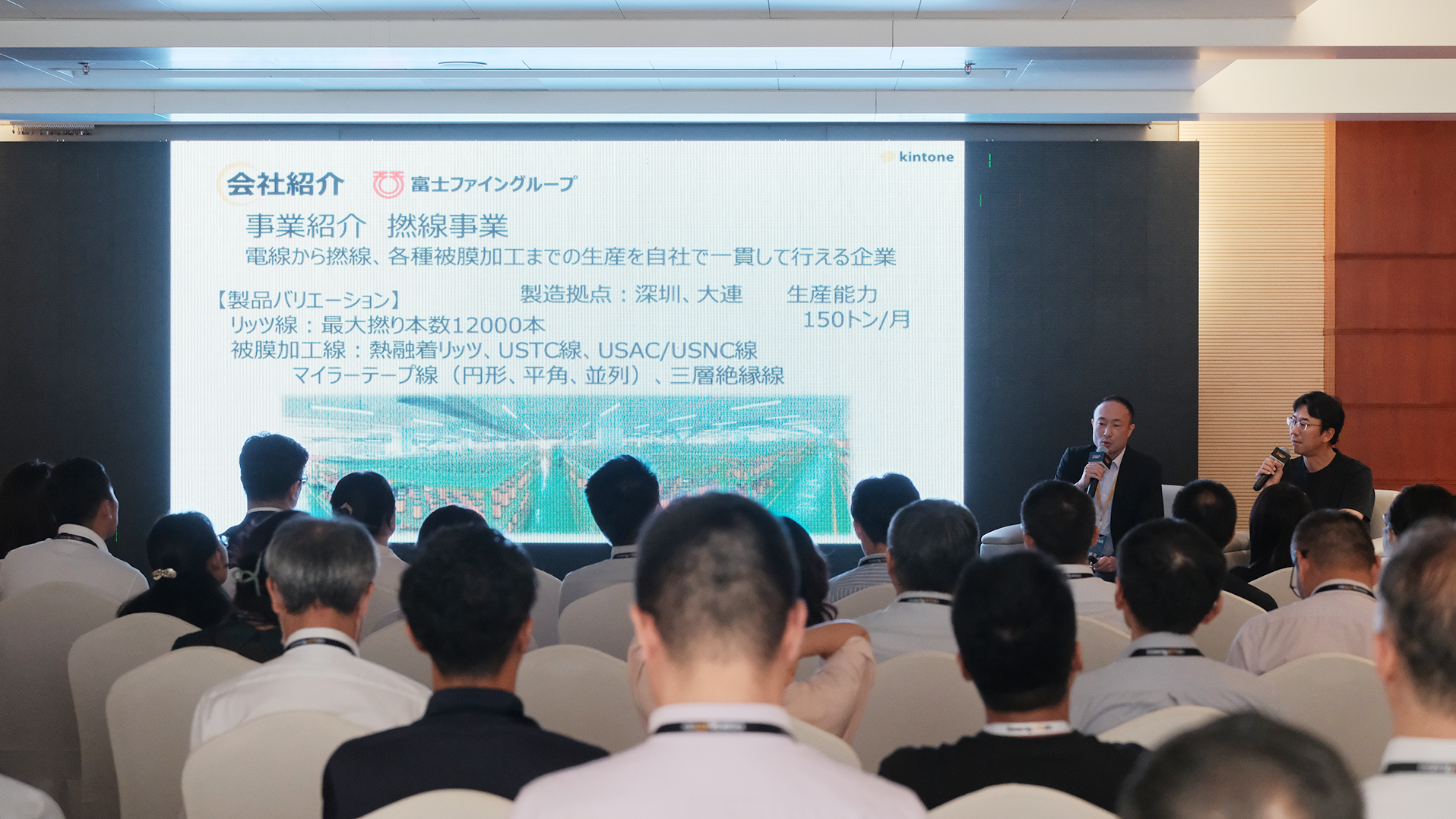
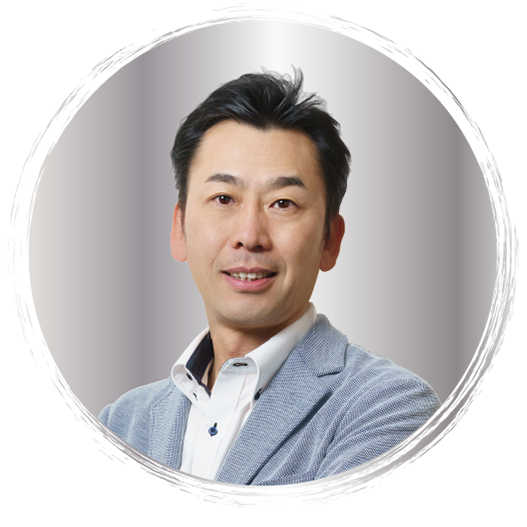
増田
ありがとうございます。私から少しお伺いしたいのですが、元々日本でソリューション営業をされていらっしゃった後、富士ファイングループに転職されたということで、工場の業務改善を役割としてご入社されたのでしょうか?
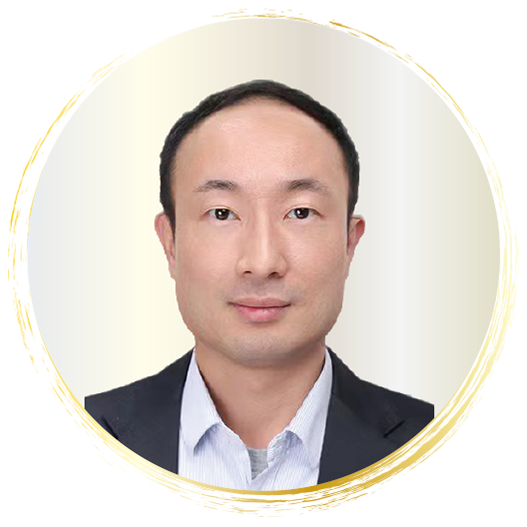
大山氏
元々は工場の管理全般という役割で入社しました。当時は製造業の業務内容に関して詳しい知見がなかったので、初めは現場で働かせてもらいながら勉強させていただくという形でやってきました。
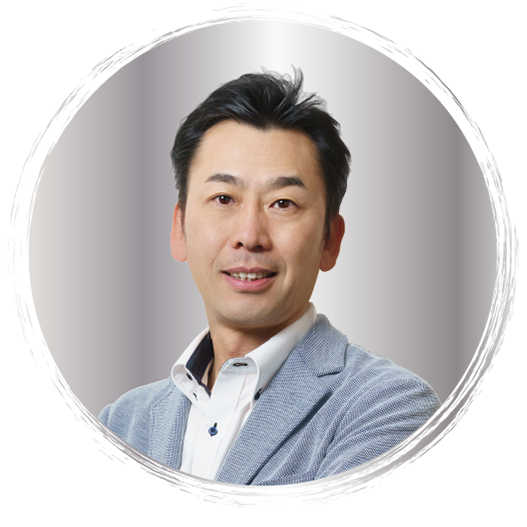
増田
工場長ということでご苦労も多くあるのではないかなと思いますがどうでしょうか。
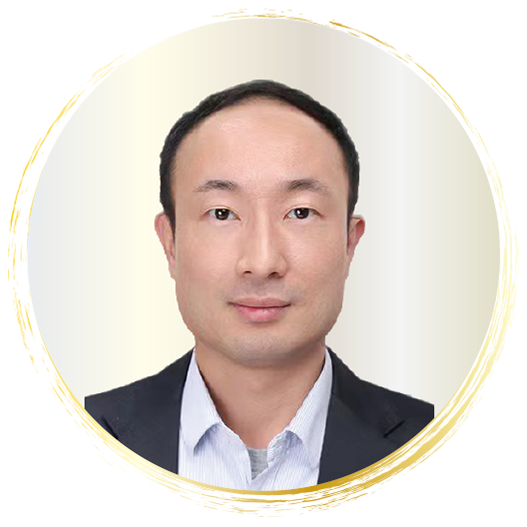
大山氏
中国ならではというところもあると思いますけれども、苦労しているところは確かに多いかもしれません。
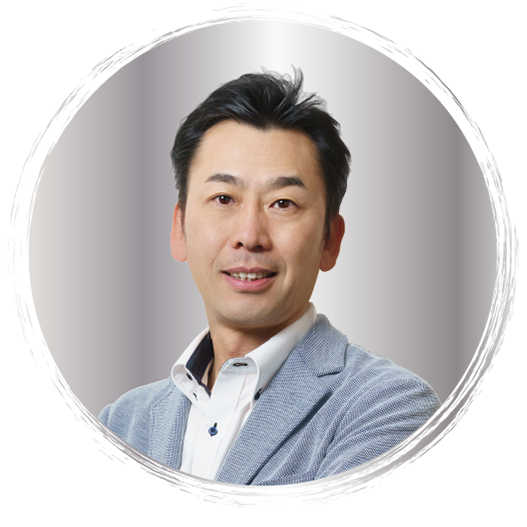
増田
なるほど、わかりました。そんな富士ファイン様ですが、ちょうど3年前にkintoneを導入いただき、大山様が旗振り役となって進めていただきました。導入前の課題を教えていただけますでしょうか。
既存システムはデータの連携性が低く、エクセル運用では作業の属人化が課題に
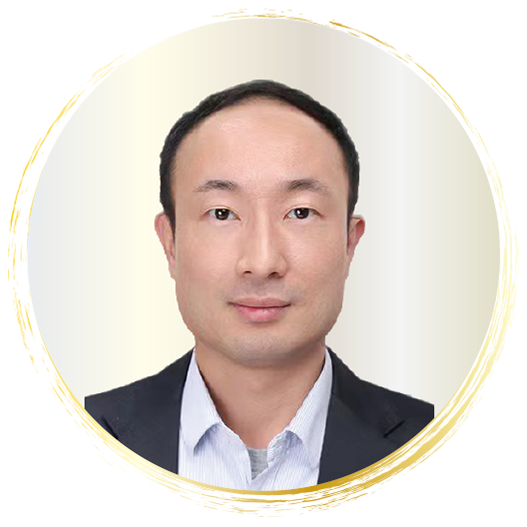
大山氏
導入前の課題は、生産系では複数の既存システムが存在しており、データの連携性が低く、拡張性に限界を感じていました。業務系ではそもそもシステムがなく、20個くらいのエクセルファイルを駆使して情報管理し、また作業方法が属人化しており、休暇時は担当者しかわからないという状況がありました。また月末の資料作成の作業では、データをコピー&ペーストして作成していたので手間と時間が非常にかかっていました。
そのような状況で、生産系と業務系を同じ環境で開発し、データ連携を行なって一つの統合されたシステムとすることが理想だと考えていました。
そのような状況で、生産系と業務系を同じ環境で開発し、データ連携を行なって一つの統合されたシステムとすることが理想だと考えていました。
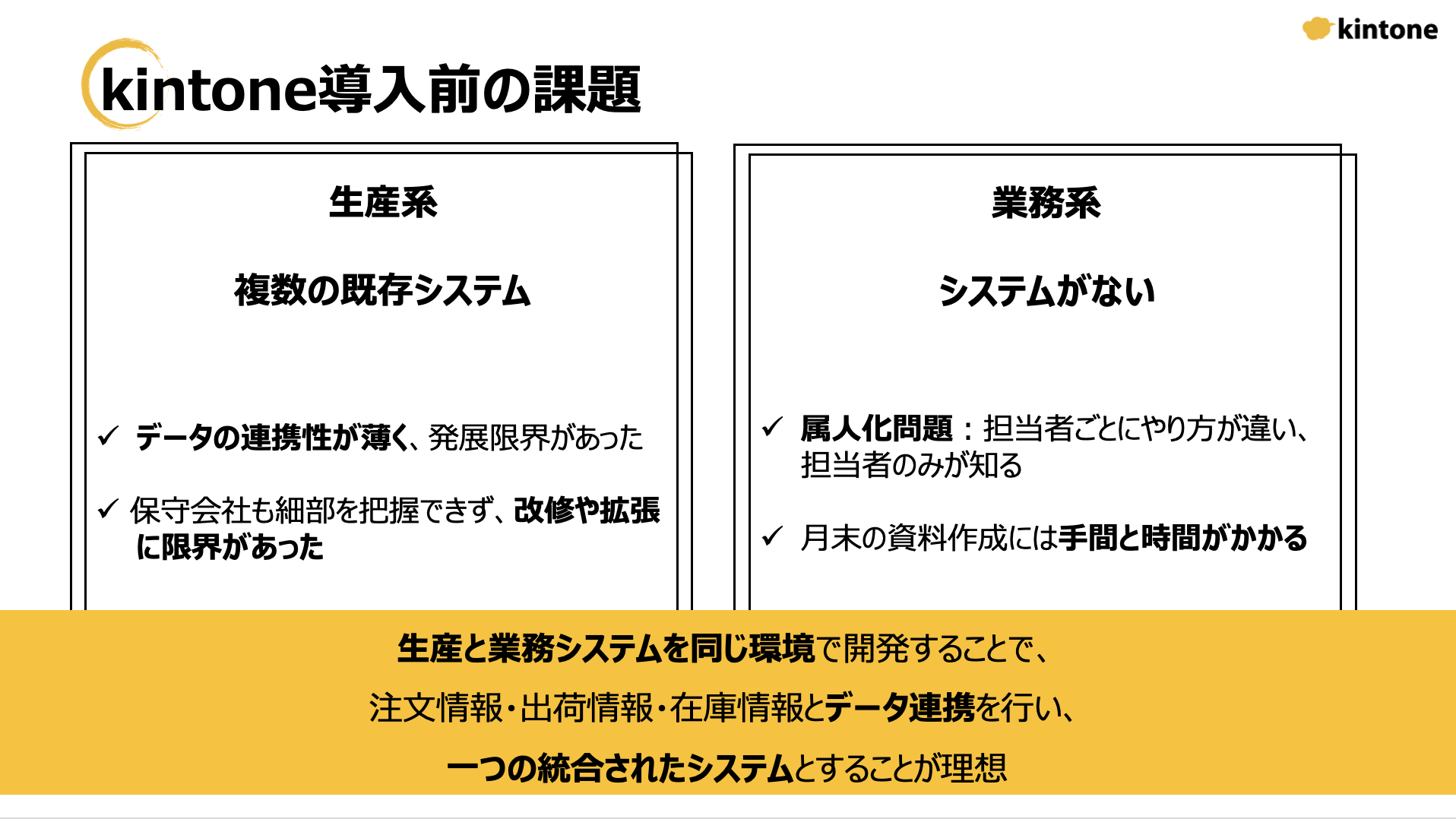
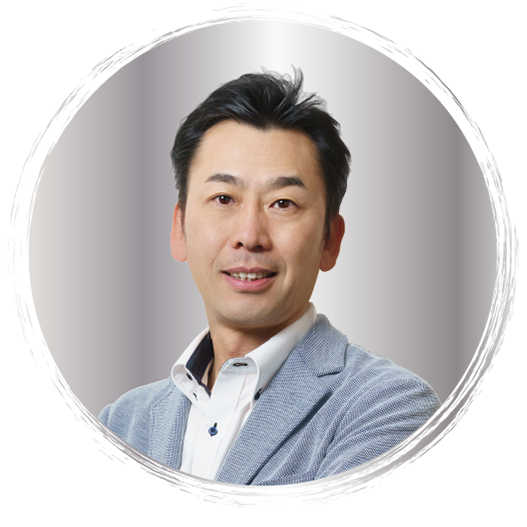
増田
私もお客様の工場にお伺いすることがあるのですが、長く工場を運営されている企業様では古いシステムを使い続けているお客様も多くいらっしゃいますので、まさにこのような課題を抱えていらっしゃる工場はあるのではないかと思います。そこでkintoneを導入いただきましたが、選定ポイントを教えていただけますでしょうか?
kintone選定の一番のポイントはパートナー企業と伴走開発ができること
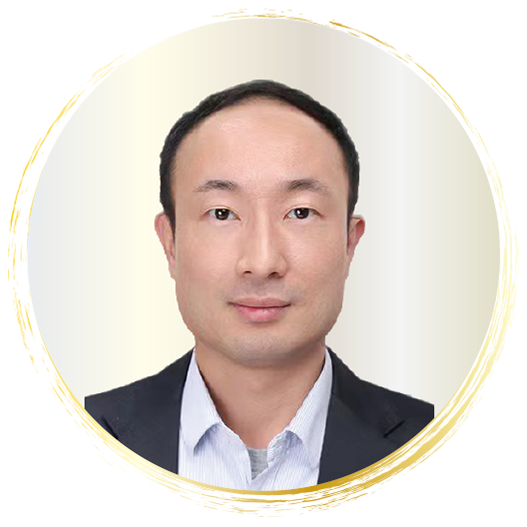
大山氏
ちょうど当時、日本本社よりITへ積極投資を行うという後押しがあり、そのタイミングでkintoneに出会いました。選定のポイントはまず、サイボウズの知名度、柔軟なアプリ設計ができるということ、ローコード開発で開発費のコストメリット、そしてあと一番はパートナー企業と伴走開発ができるところで、レンユアー社をご紹介いただけたことです。
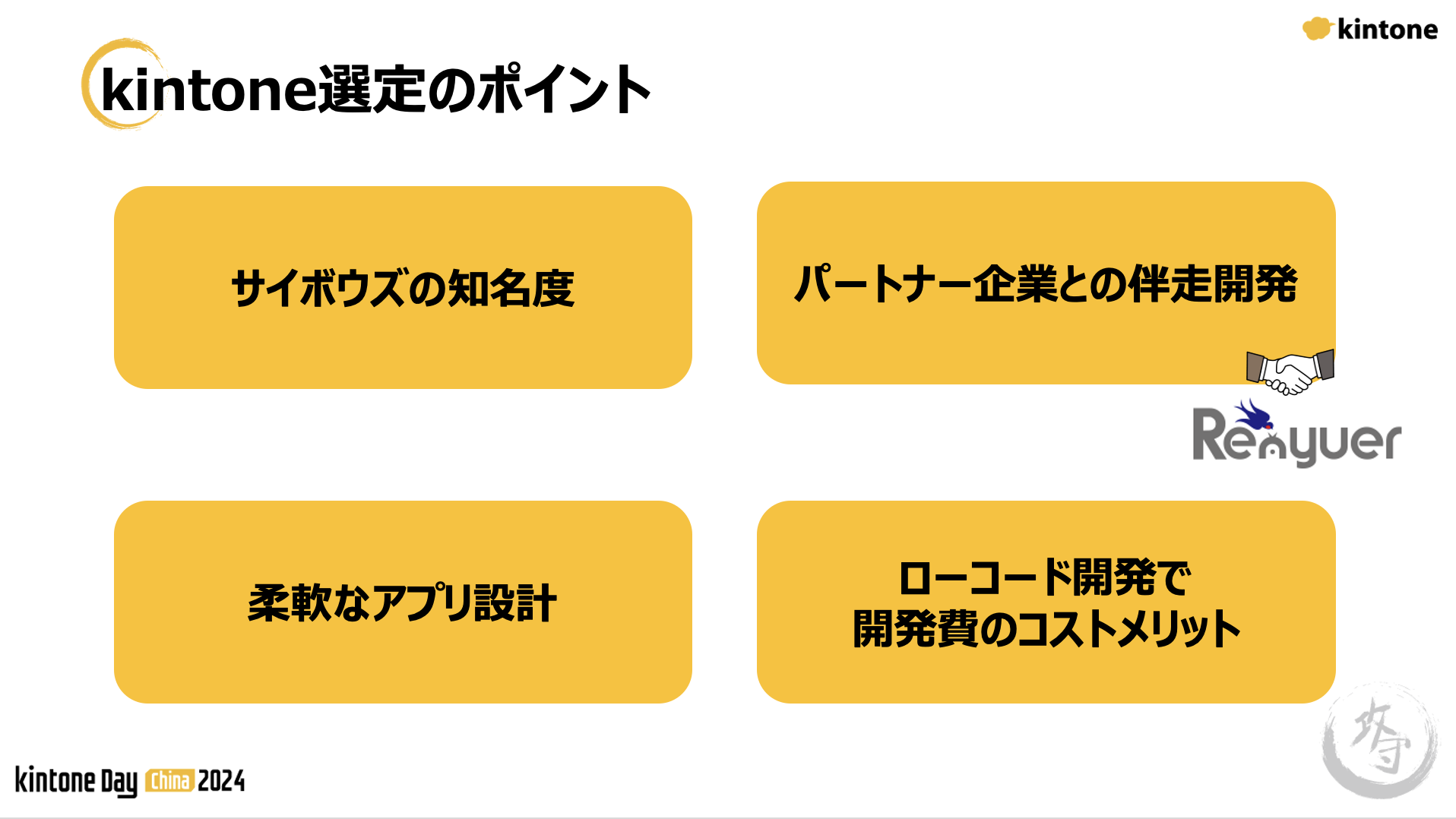
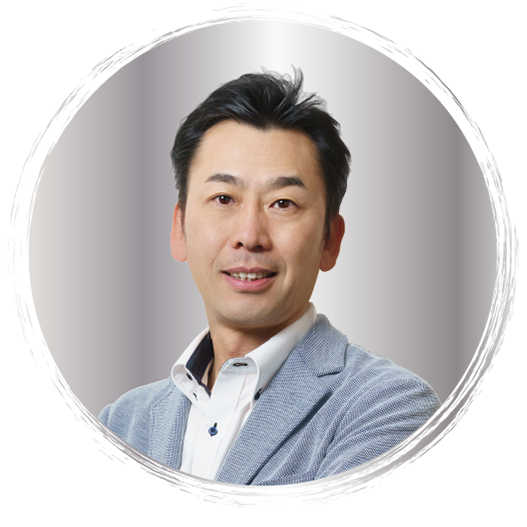
増田
実は当初我々が直接営業に伺いましたが、生産系の課題については我々としてもノウハウが少ないため、製造業で構築実績のあるレンユアー社をご紹介させていただきました。レンユアー社との役割分担はどのようにされているのでしょうか?
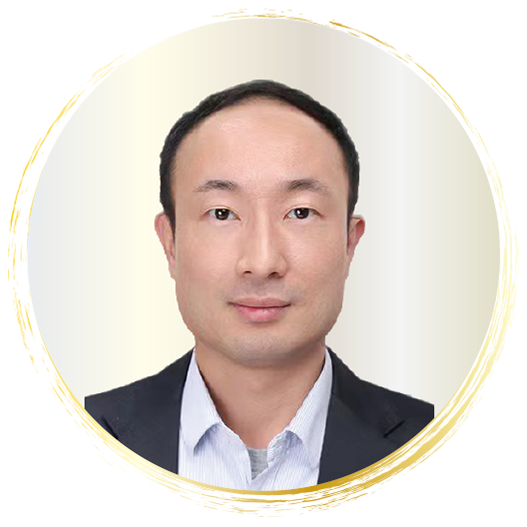
大山氏
kintoneの画面設計や社内ヒアリング、あと機能の要件定義やアプリ間の連携の部分は私が行いました。そしてカスタマイズが必要になる部分、例えばプリンターからラベルを出す仕組みや半自動で計量を行ってkintone内にデータを入れてラベルを出力するという仕組みはレンユアーさんにお願いしました。
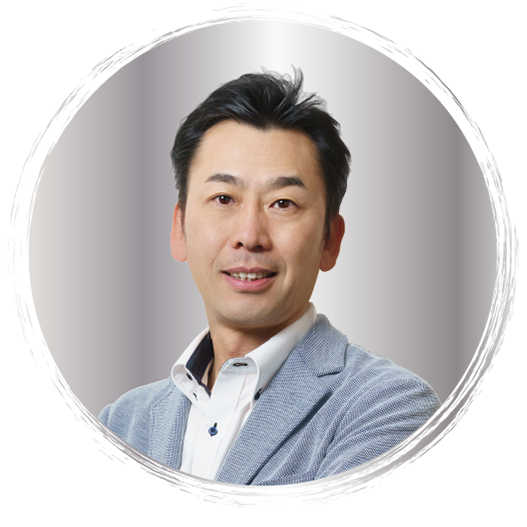
増田
なるほど、ありがとうございます。それではここからは具体的な活用についてご紹介いただきたいと思います。
作業員がミスしない仕組みを構築、製造現場の作業最適化を実現
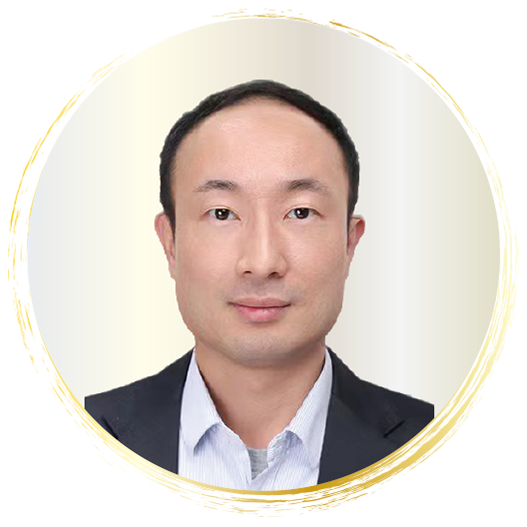
大山氏
工場での業務はおおよそ網羅しています。生産系アプリ、在庫管理アプリ、業務系アプリ(製造販売、仕入販売)、出荷系アプリ、営業系アプリ、あと営業系アプリや見積アプリなど顧客との関連性を管理するようなアプリも作っています。
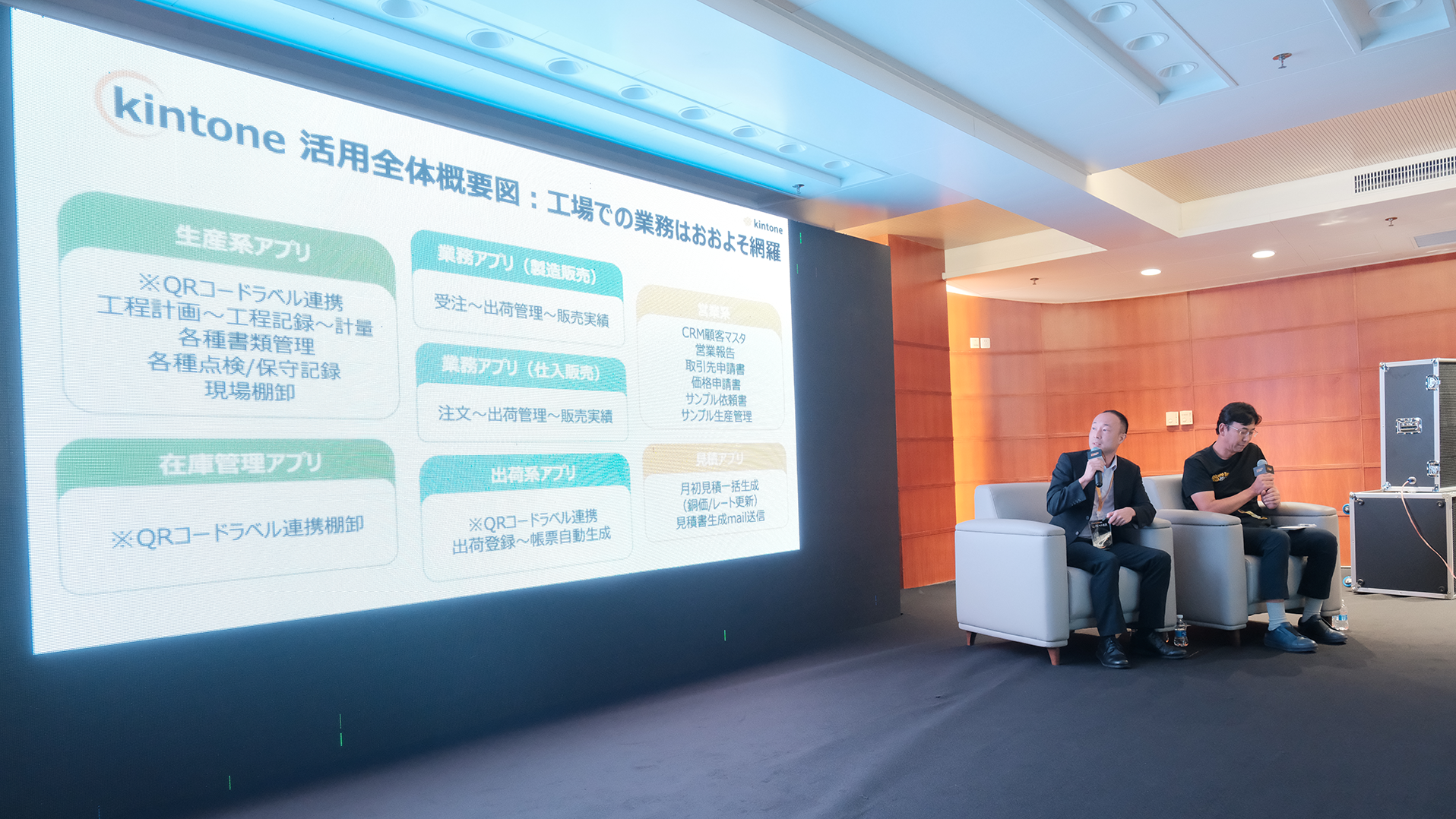
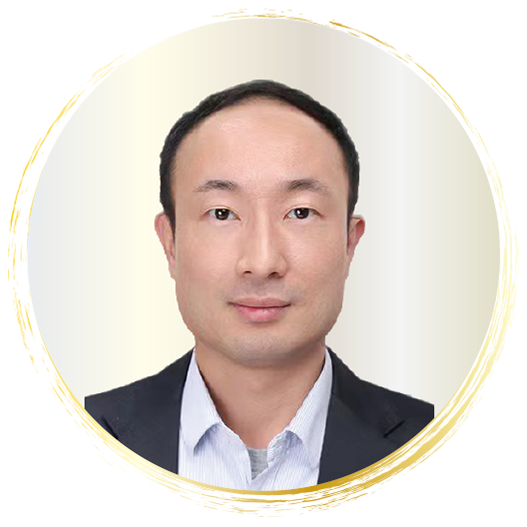
大山氏
ここからは、生産系システムのQRコード連携というところで、工程計画から計量〜梱包確認までを紹介させていただきます。
弊社撚線事業の特徴なのですが、元となる細い電線を複数回撚り合わせて皮膜加工しながら分解していきます。一つの品名で前工程を複数台で加工して後工程を確保していく流れで、色々な組み合わせパターンがあります。材料も何十種類とあり、また皮膜の有無、重さも10キロから約80キロとなかなか大きく重めの製品になっているのが特徴です。
弊社撚線事業の特徴なのですが、元となる細い電線を複数回撚り合わせて皮膜加工しながら分解していきます。一つの品名で前工程を複数台で加工して後工程を確保していく流れで、色々な組み合わせパターンがあります。材料も何十種類とあり、また皮膜の有無、重さも10キロから約80キロとなかなか大きく重めの製品になっているのが特徴です。
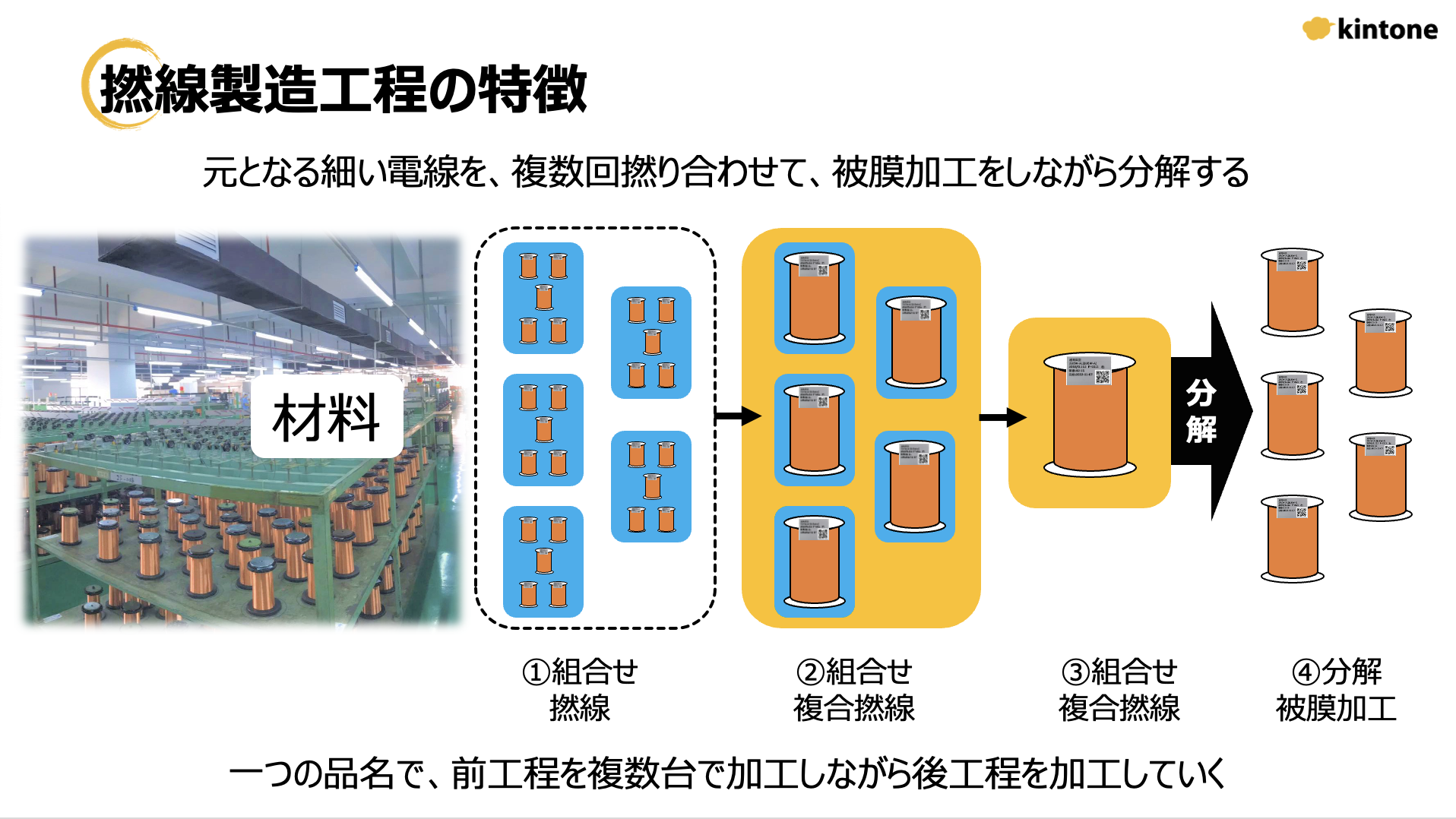
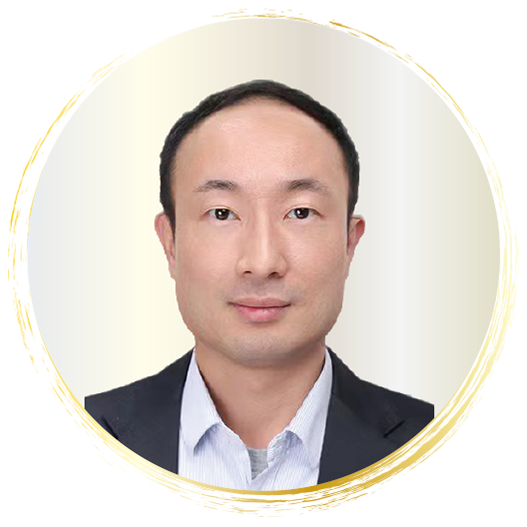
大山氏
こちらは工程計画のアプリです。現場でPDAを使って作業を行い、登録された生産重量がリアルタイムで反映されるようになります。現在機械は80台くらいあり、メインの撚線工程は全部自動的にわかるようになっています。そして特殊管理事項を含めた各工程の指示書を全て自動生成、PDAを用いて現場起点の機械変更も計画表へ自動反映行うようにしました。
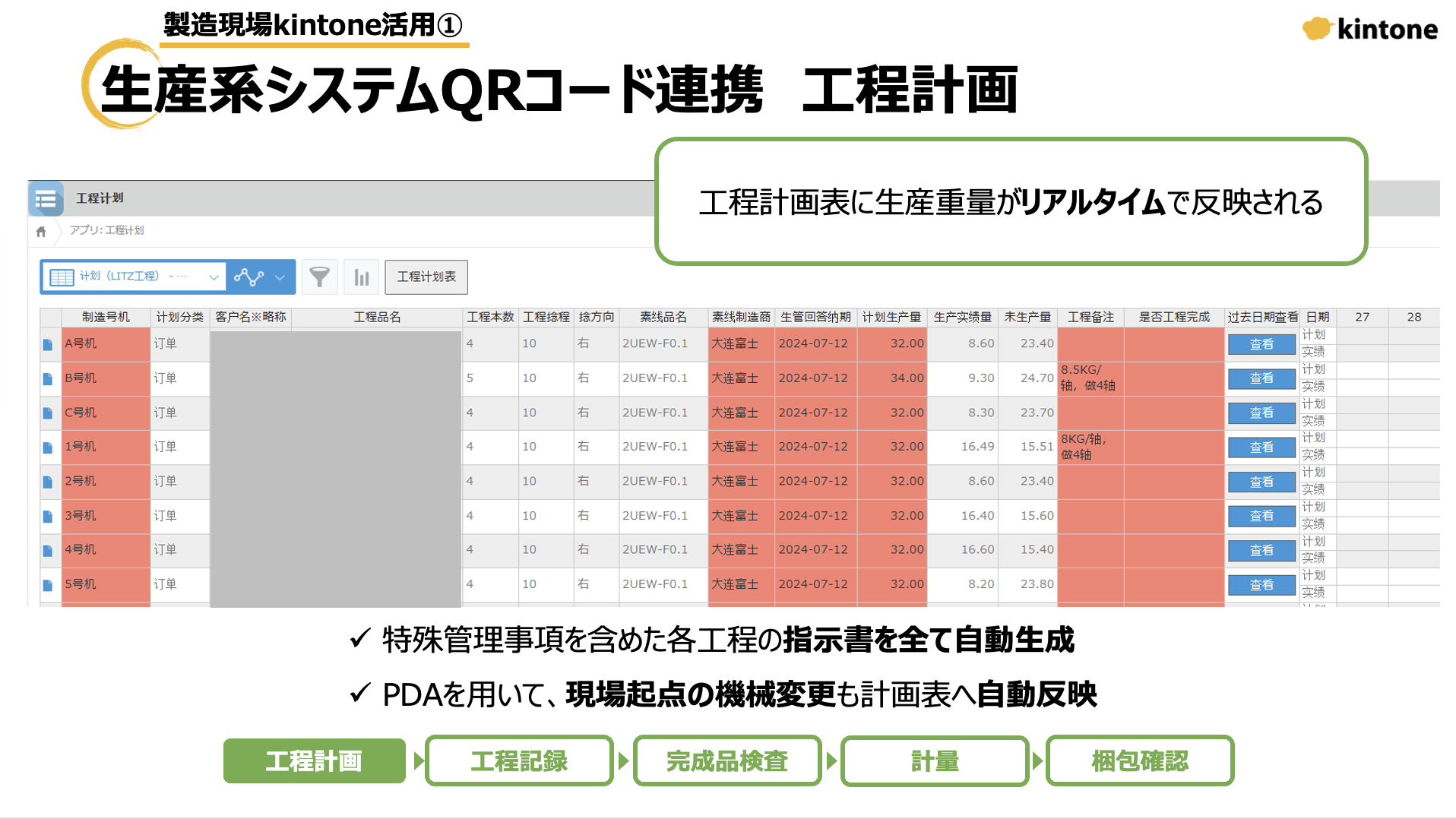
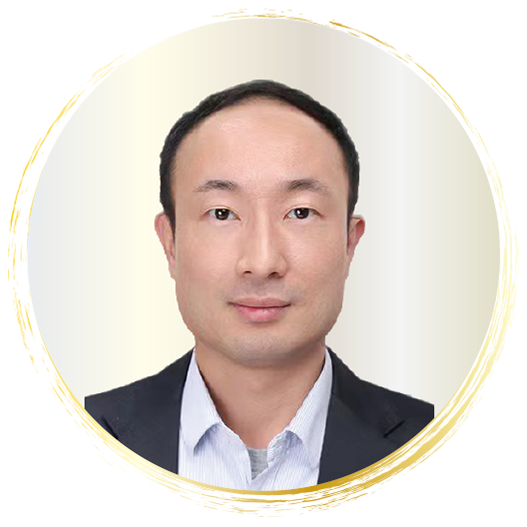
大山氏
続けて、工程記録です。PDAで指示書のQRコードを読み取って作業スタートです。ミスしない仕組みを非常に盛り込んであるのですが、工程記録を保存するとアプリ内にデータが登録されます。その場で印刷ボタンを押すと、工程ラベルQRコード付きのものが印刷されるのでその場で完成品に貼り付けを行います。
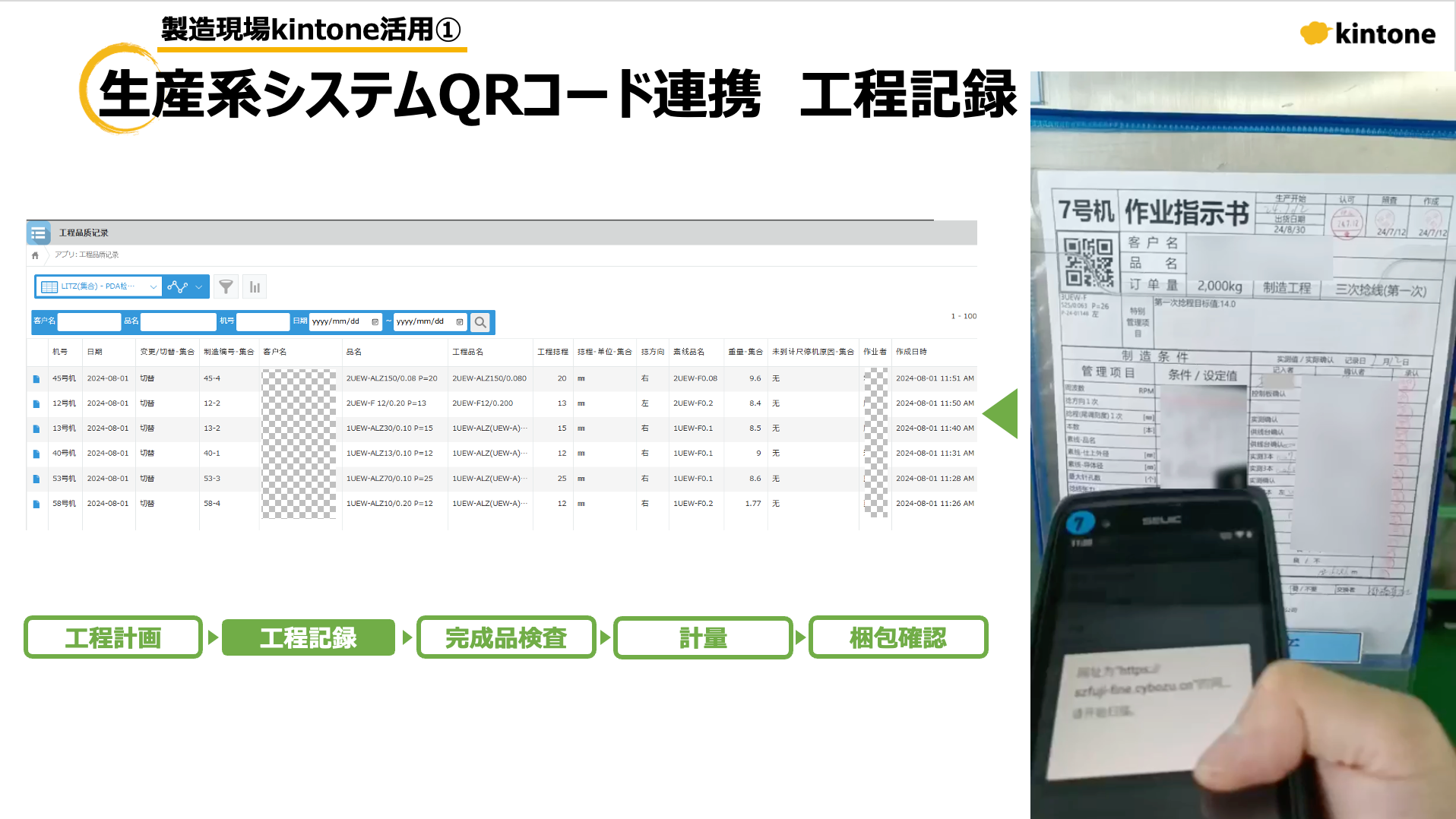
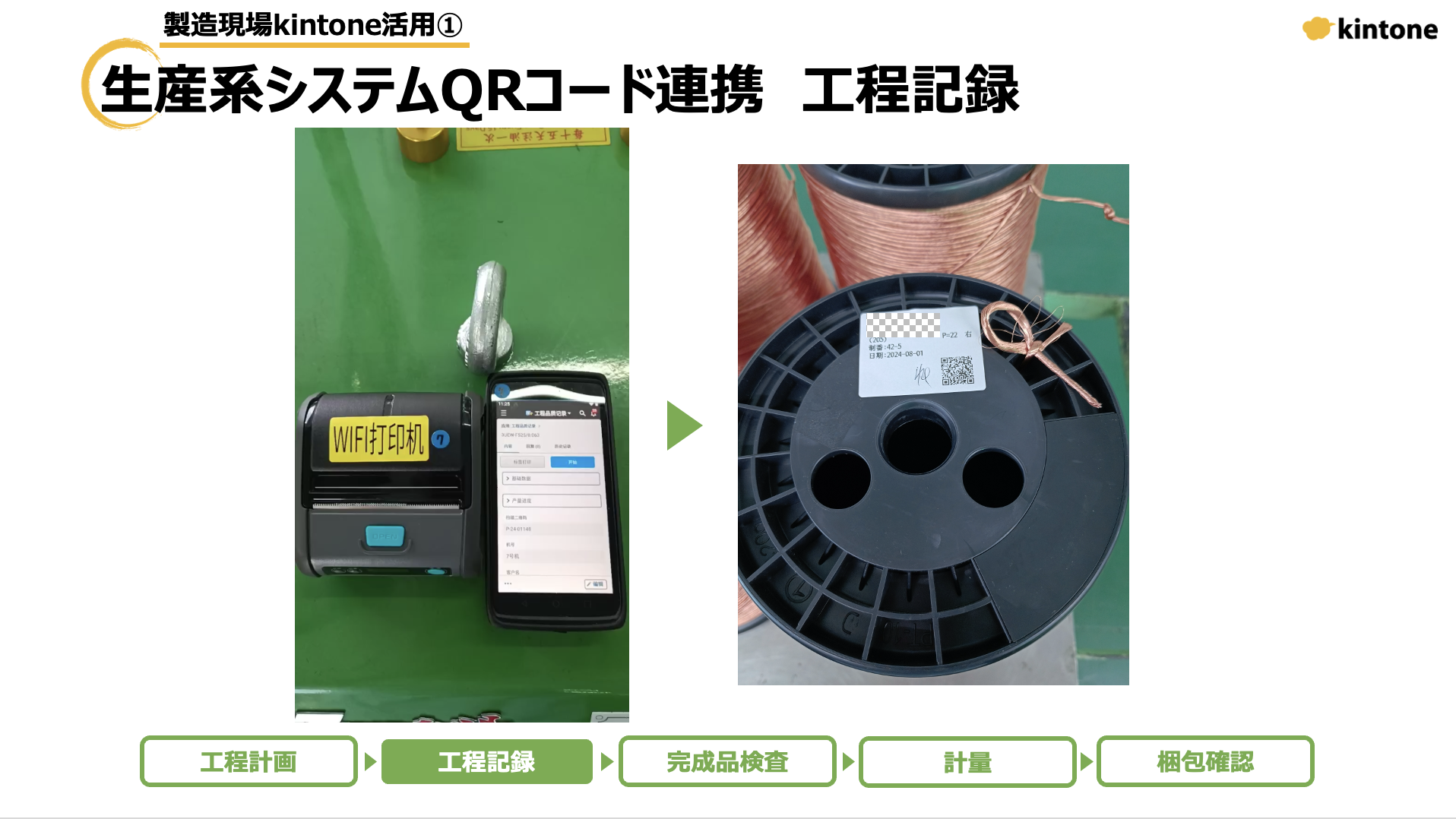
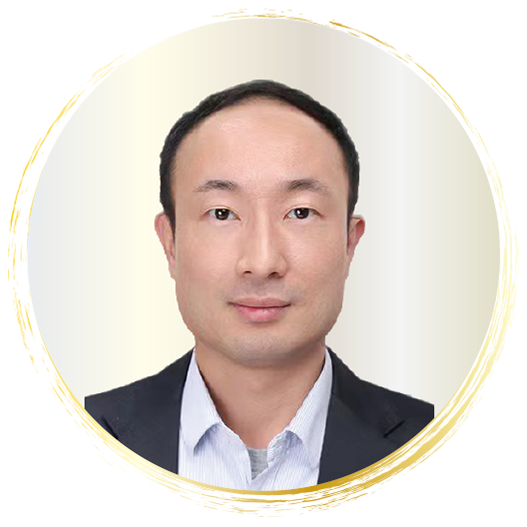
大山氏
そしてここからは完成品検査です。QRコードを読み込んで、検査データを入力します。このデータが試験成績書の元データになります。
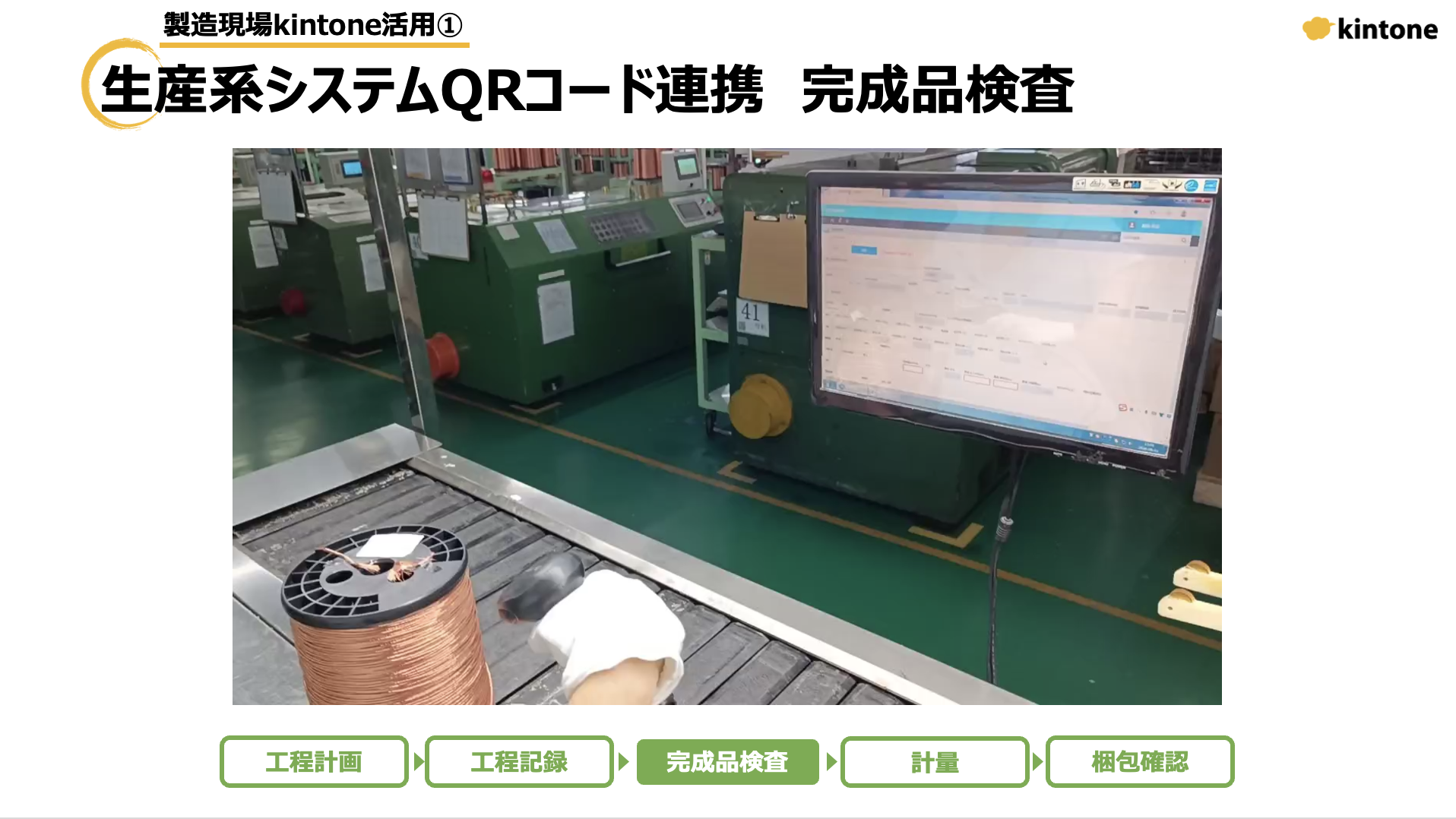
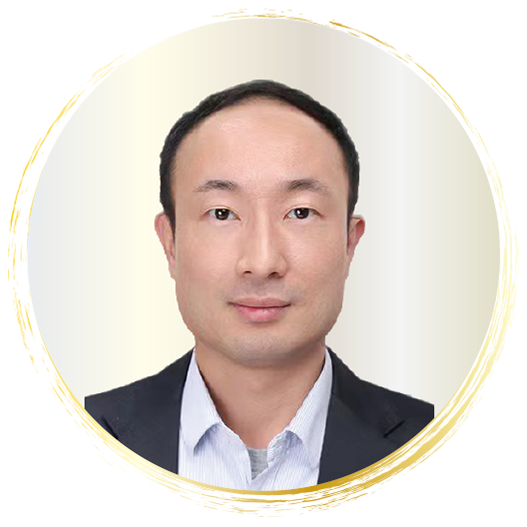
大山氏
続けて計量です。ラインに流れてきた製品についているQRコードをスキャンすると重量ラベルが出てきます。製品によって箱入り数分のラベルが出てくるようになっていますので、その場で貼り付けます。この辺りも作業員がミスをしない仕組みを構築しております。
計量が半自動で終わりましたら、自動的にkintoneにデータが入るようになります。
計量が半自動で終わりましたら、自動的にkintoneにデータが入るようになります。
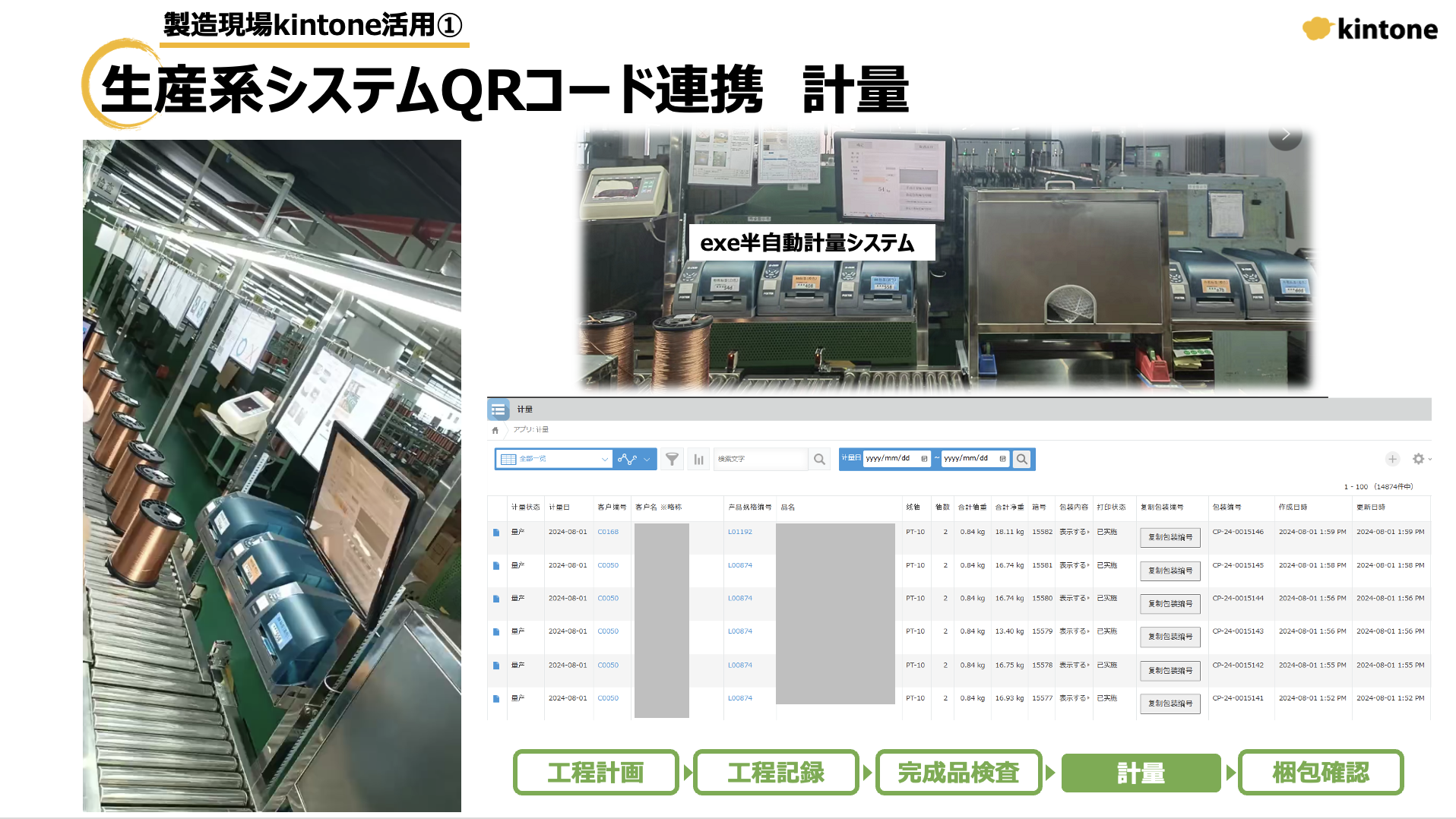
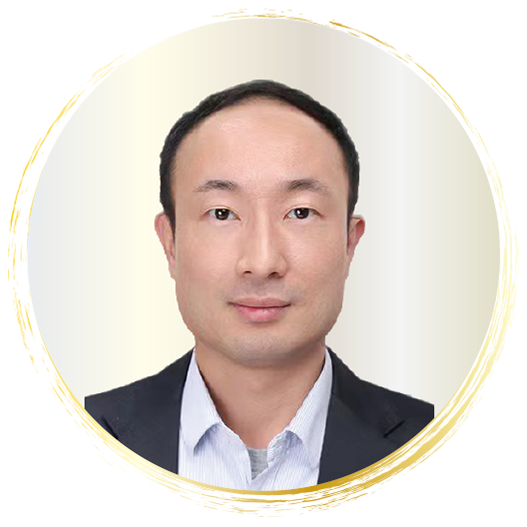
大山氏
最後に梱包確認です。製品のラベルと箱のラベルの一致確認を行なって、お客様指定のラベルがあればバーコードを追記して印字し、一致確認をできるようにしています。
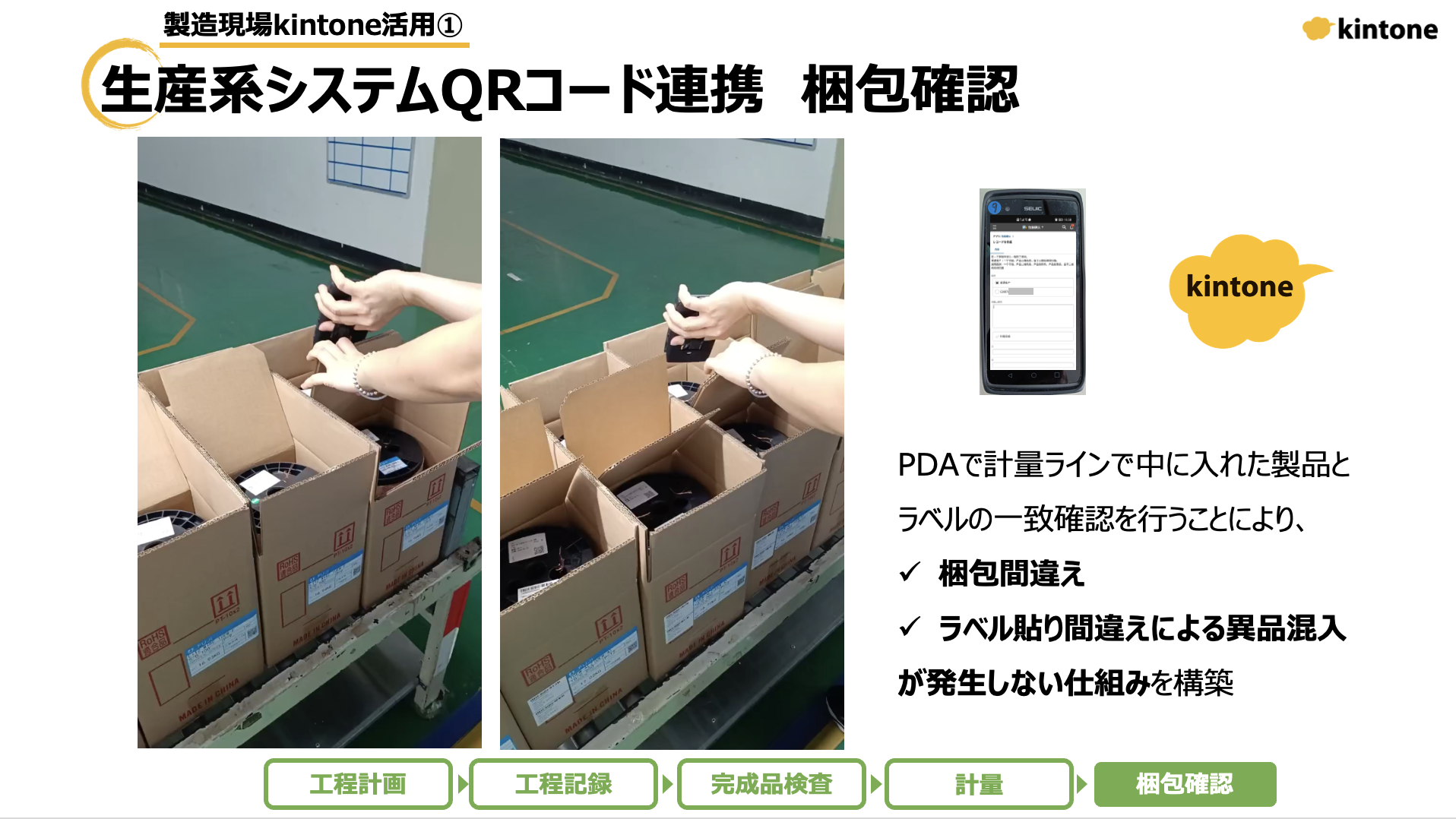
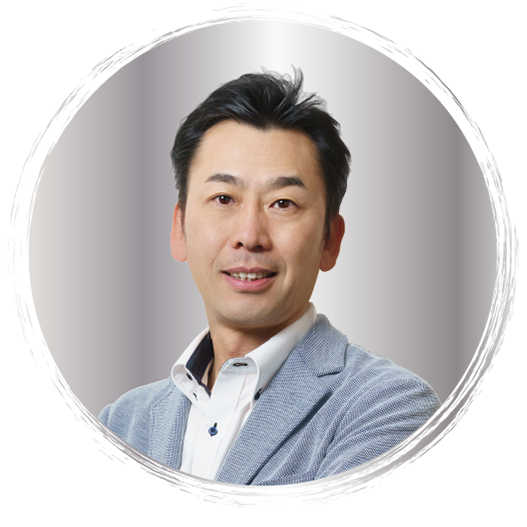
増田
我々もびっくりするくらいkintoneで工程計画から梱包確認までを構築されているのですが、実際にここまでやるのにどのくらいの期間がかかったのでしょうか?
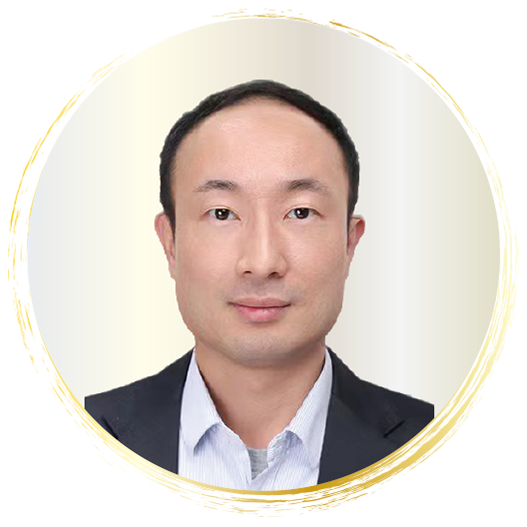
大山氏
そうですね、2年半くらいかかっています。当初はまず業務系から着手して約1年、その後製造系で約8ヶ月、そして製造系と業務系のアプリの統合やその他周辺アプリの構築に約1年です。今まで色々と最適化しながら、ここまで来たという感じです。
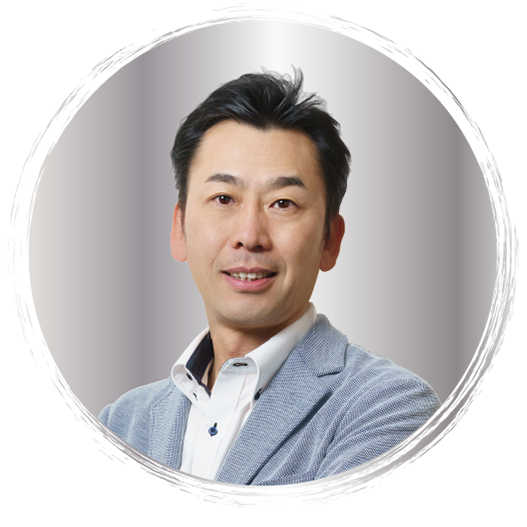
増田
なるほど。工場のラインを止めてはいけない中で、前のやり方から新しい仕組みに変える時の切り替えの時はどのような感じで切り替えていかれたのでしょうか?
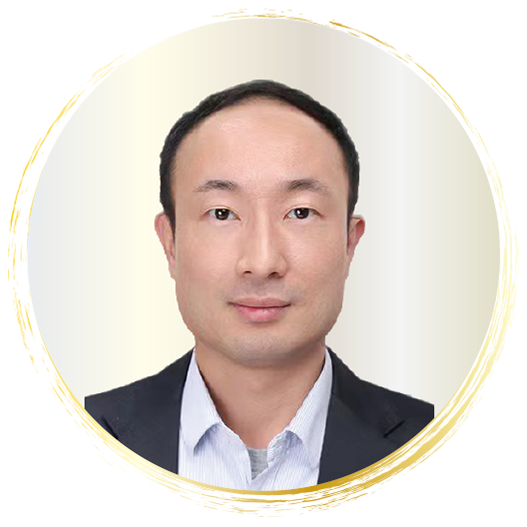
大山氏
運用できると判断した時点で、まずは以前の方法と並行して切り替え始めました。
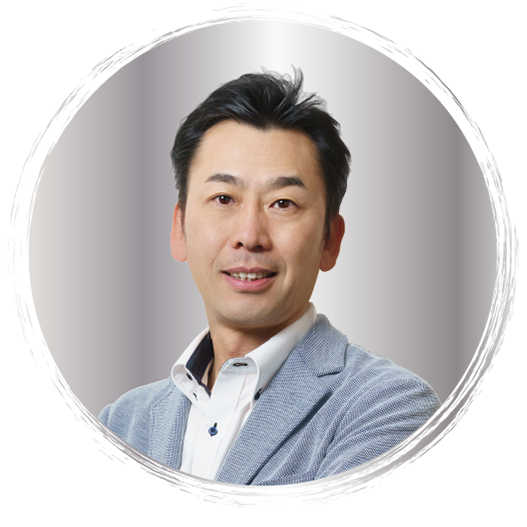
増田
わかりました。今ご紹介いただいたシステムをすぐにでも欲しいと思われた方もいらっしゃるのではないかと思いますが、まださらに活用をご紹介いただきます。
製造現場と業務側が常に最新情報を共有し、出荷スケジュールを管理
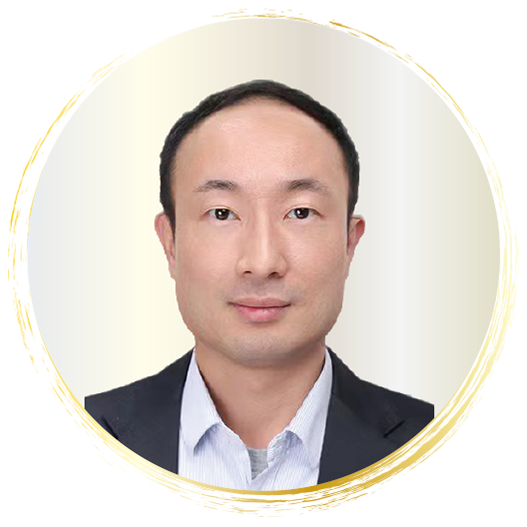
大山氏
はい、ここからは受注登録から出荷作業、出荷系帳票の自動生成までをご紹介します。
これは出荷スケジュールの管理画面です。業務側で出荷案件の進捗管理を行い、出荷指示を生成します。そして製造側と自動更新される在庫・出荷残・未生産量を共有しています。業務と製造側双方でこのアプリをよく確認しており、キーになるアプリです。
これは出荷スケジュールの管理画面です。業務側で出荷案件の進捗管理を行い、出荷指示を生成します。そして製造側と自動更新される在庫・出荷残・未生産量を共有しています。業務と製造側双方でこのアプリをよく確認しており、キーになるアプリです。
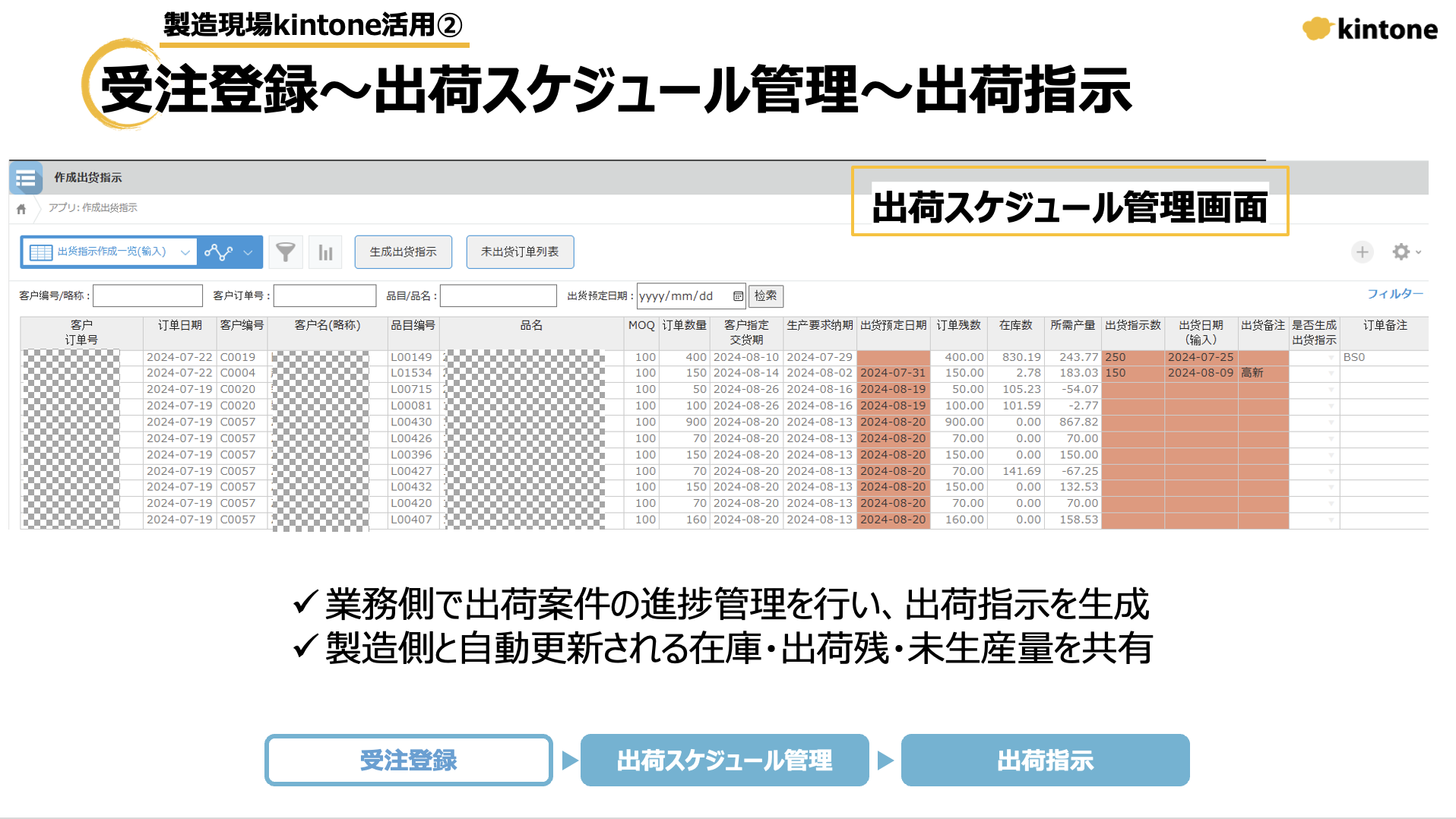
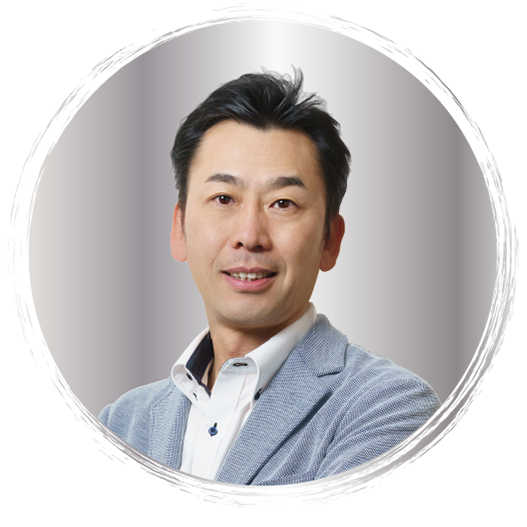
増田
この画面はエクセルの表に見た目がかなり近い画面になっていますが、開発されたのですか?
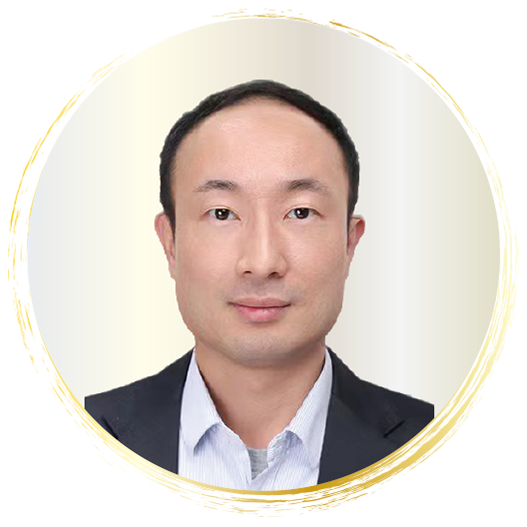
大山氏
そうですね。赤いところをクリックすると選択入力ができるようになっており、必要最低限の入力だけで済むように開発しました。
次は、出荷製品のピックアップとピックアップした後に出荷済状態に積み替えをします。パレット積み状態のスキャン登録まで行えば、例えばインボイスやパッキングリスト、出荷明細送り状でお客様指定の外装ラベルや通関データをワンプッシュで自動生成できます。
次は、出荷製品のピックアップとピックアップした後に出荷済状態に積み替えをします。パレット積み状態のスキャン登録まで行えば、例えばインボイスやパッキングリスト、出荷明細送り状でお客様指定の外装ラベルや通関データをワンプッシュで自動生成できます。
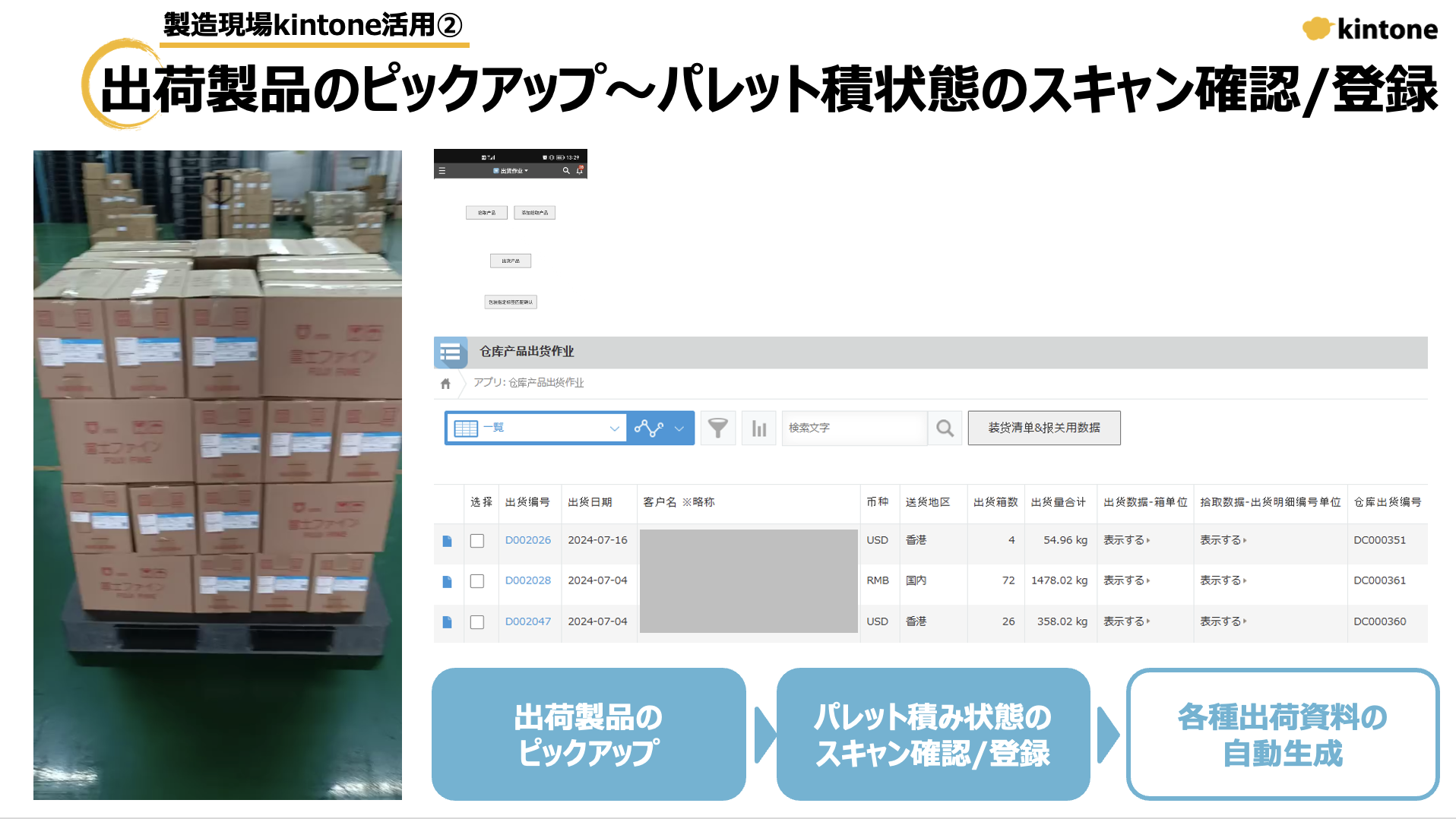
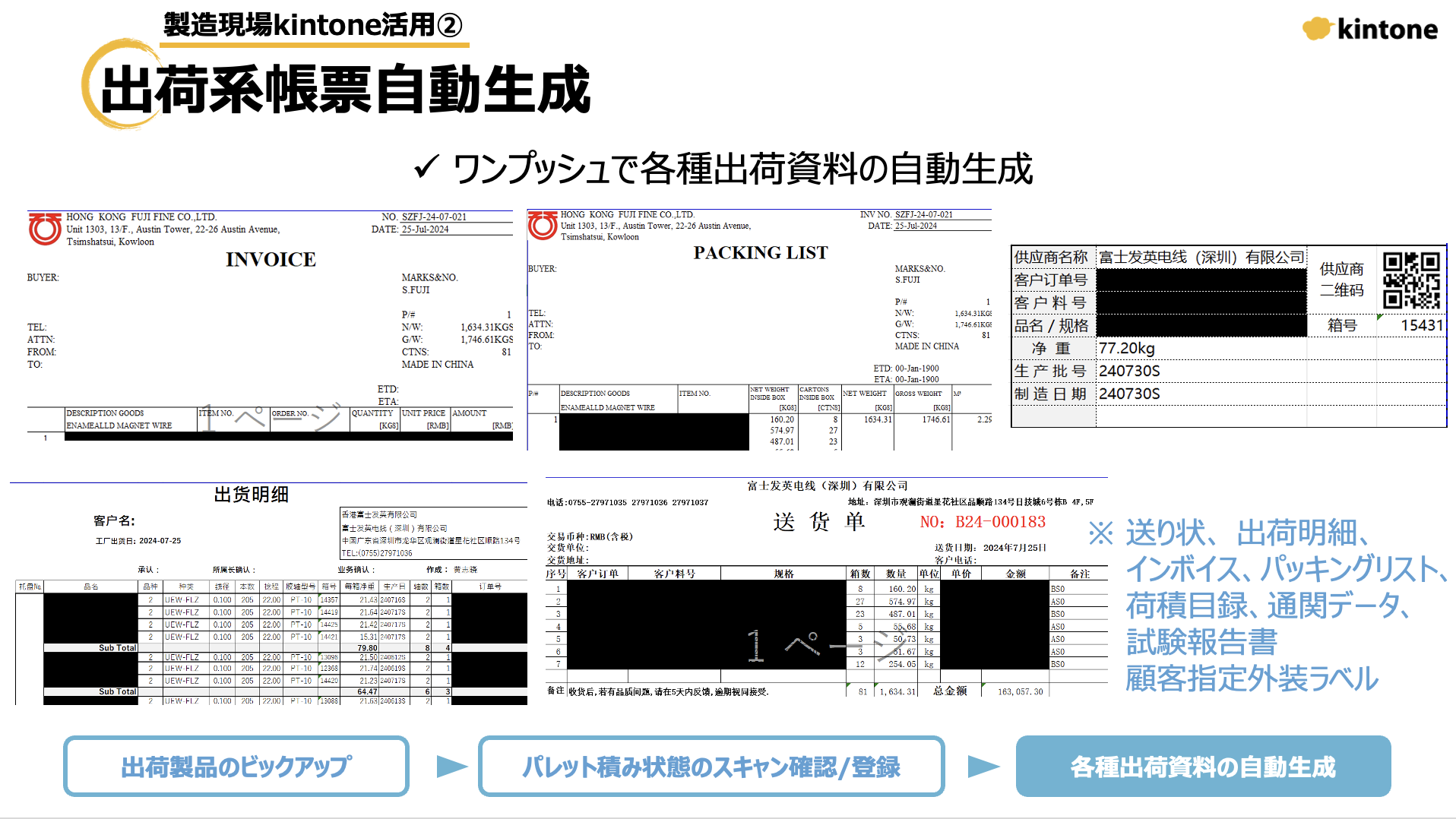
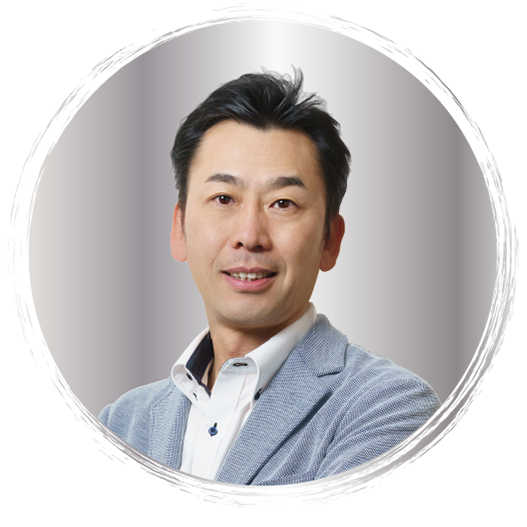
増田
以前これらはほとんど紙で対応されていたのでしょうか?
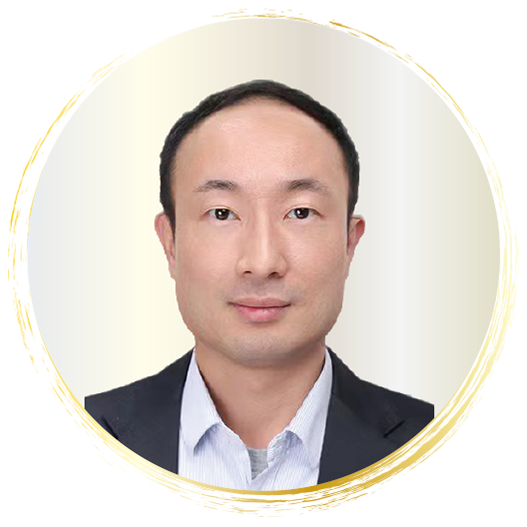
大山氏
そうです。一部システムもあったのですが、使い勝手が悪い部分があり、例えばデータをエクセルに書き出す機能はあっても一部手加工が必要な部分があったりしてミスが起こりやすい状況になっていました。
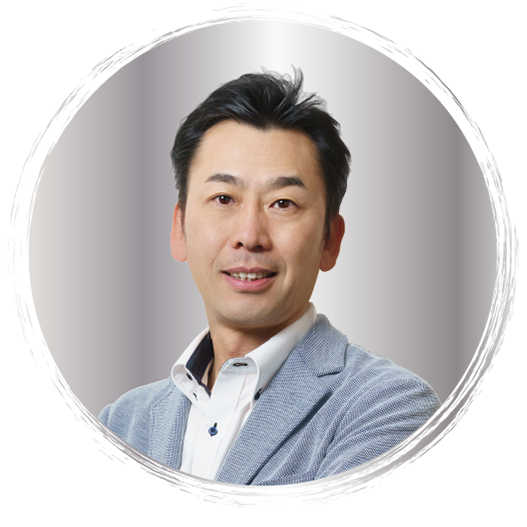
増田
実際にかなり業務改善がされていると思うのですが、現場の方達からすると以前のやり方と変わることで抵抗があったのではないかと思います。どのような工夫をして乗り越えてこられたのでしょうか?
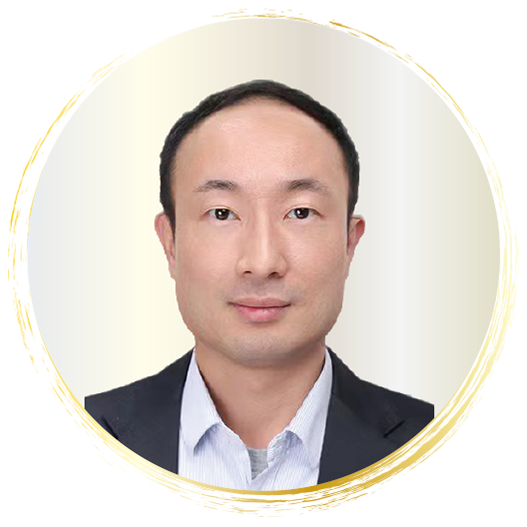
大山氏
製造現場でいえば、まず中国人スタッフと現場をよく知っている指導員の二名に教育をさせていただいて、そこから作業員に落とし込みをしていただく形で始めました。しかしそれだけではなくて、自由に発言してOKのWeChatグループを作成して、全員に入ってもらい、そこで要望や質問、良くない点などフィードバックをもらいました。
年間作業時間3,630時間の削減に成功、スモールスタートから非常に大きな成果が
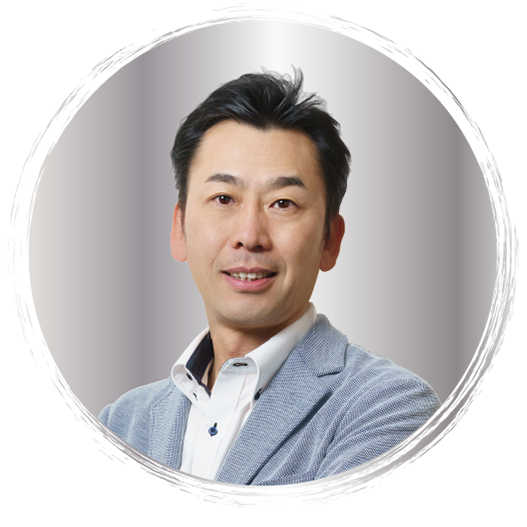
増田
なるほど、ありがとうございます。二年半かけてここまでの仕組みを構築されますと、やはり導入効果もかなりあったのではないかと思うのですが、いかがでしょうか。
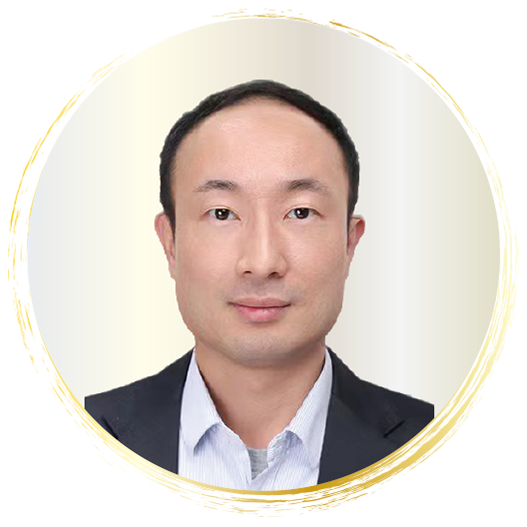
大山氏
導入効果につきましては、報告書や資料の自動生成、そして自動集計や自動印字を実現したことで、計画通りの大幅な工数削減に成功しました。作業時間で3,630時間/年削減、試算すると月当たり2万元の削減効果です。
これはあくまでミスをしなかった場合の試算で、効率的でミスが発生しない仕組みの構築により、ミスをした時の作業時間やリカバリーにかかる作業時間がなくなったことも非常に大きいです。
これはあくまでミスをしなかった場合の試算で、効率的でミスが発生しない仕組みの構築により、ミスをした時の作業時間やリカバリーにかかる作業時間がなくなったことも非常に大きいです。
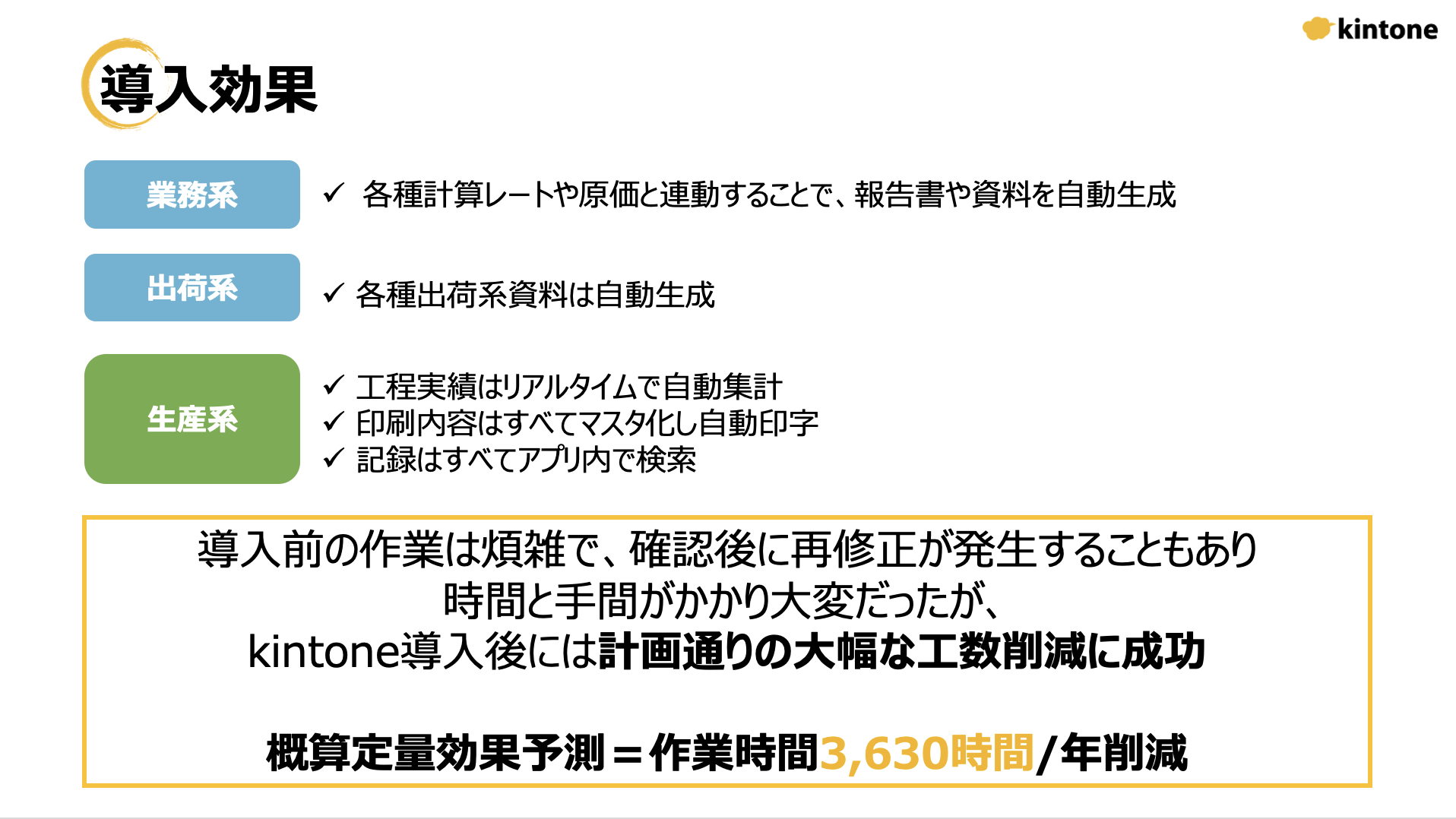
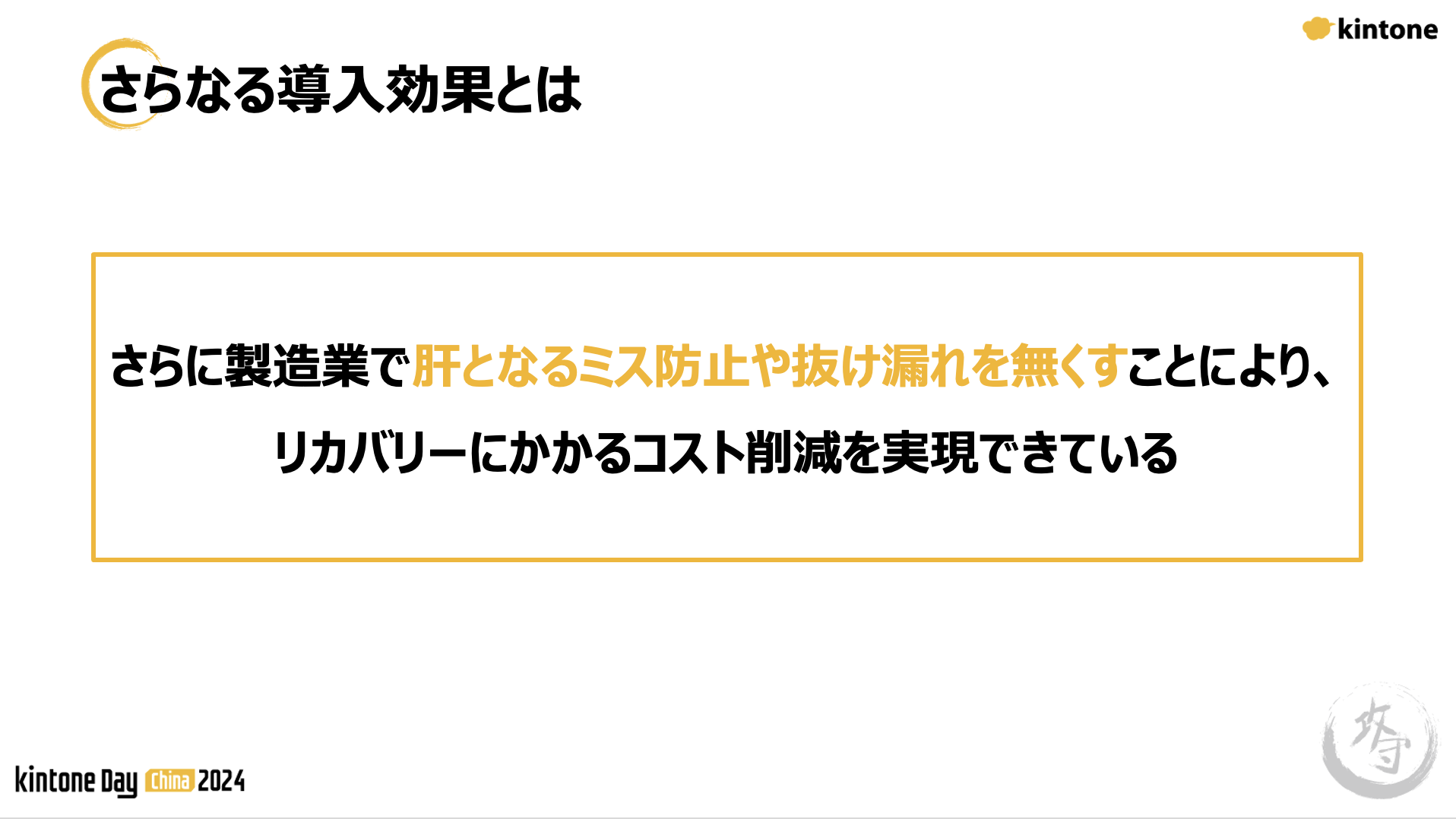
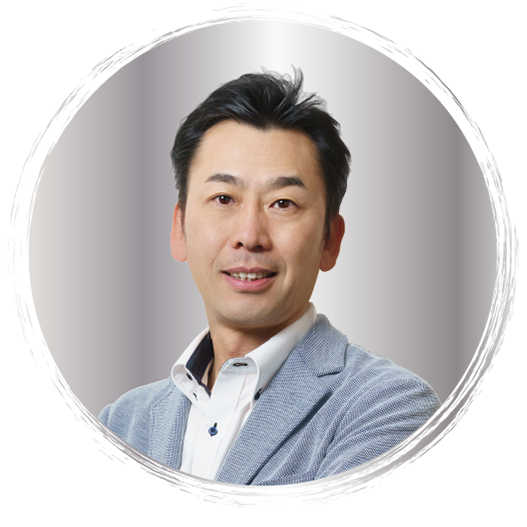
増田
なるほど、ありがとうございます。我々も製造業様にご提案する際に、スモールスタートで始めて下さいとご提案しますが、そうなると費用対効果もあまり出てこないため検討が進まないケースがあります。これについては、積み重なっていくとかなり大きな効果が生まれると考えてよろしいのでしょうか?
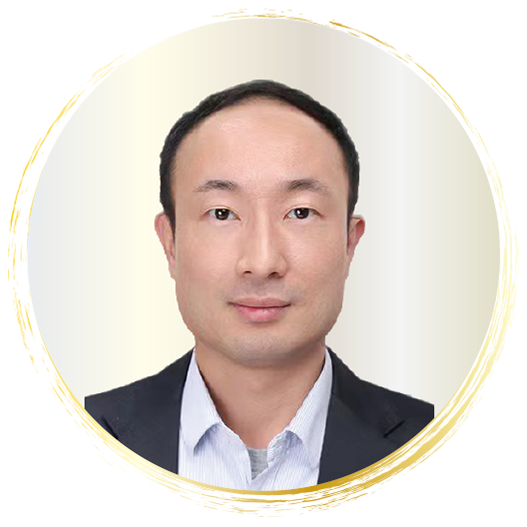
大山氏
はい、非常に大きな効果が出ていると思います。エクセルでよく起こっていたミスもぱたっとなくなりましたし、お客様からのご指摘も目に見えて減りました。
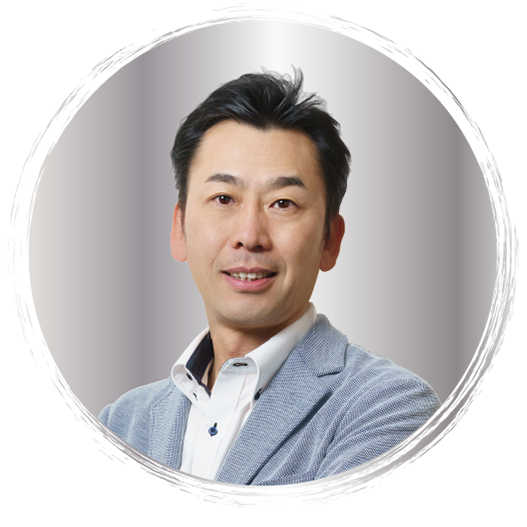
増田
御社ではスモールスタートでいうと、どの分野から着手されたのでしょうか?
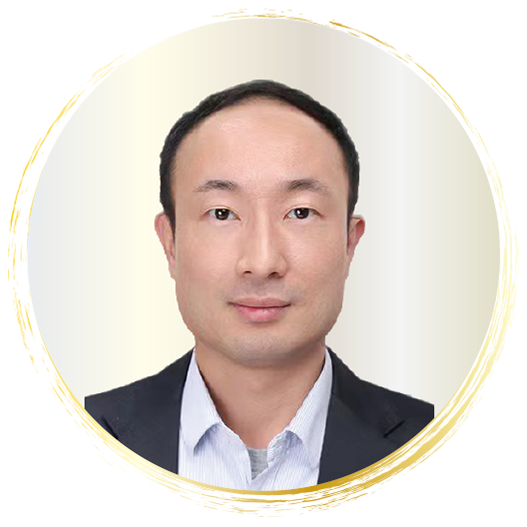
大山氏
見積アプリです。業務の流れ的にまずマスタを作った後に見積アプリを作り、その情報を使って受注管理に流すためです。
ここで満足せず、さらなる最適化を目指す。そして他拠点展開も視野に。
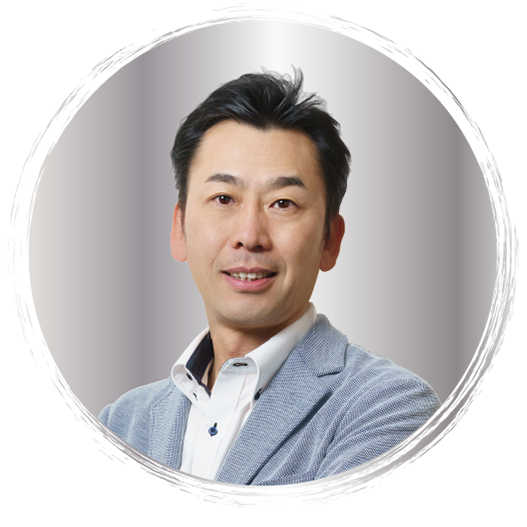
増田
今後の展望を教えてください。
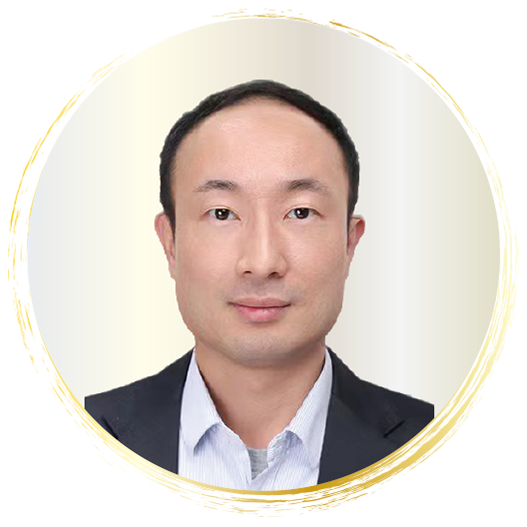
大山氏
さらなる最適化はもちろんですが、深圳モデルを他拠点、大連工場に横展開することも構想しています。
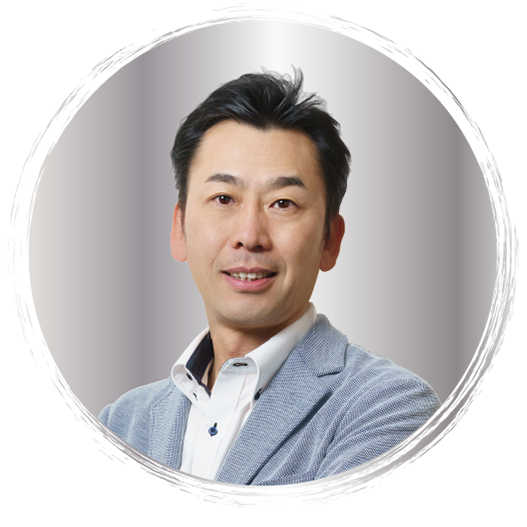
増田
ありがとうございます。ここまでのところは大山様が旗振り役で推進されてきましたが、DX人材の育成という視点では次に繋げるメンバーの育成を進められているのでしょうか?
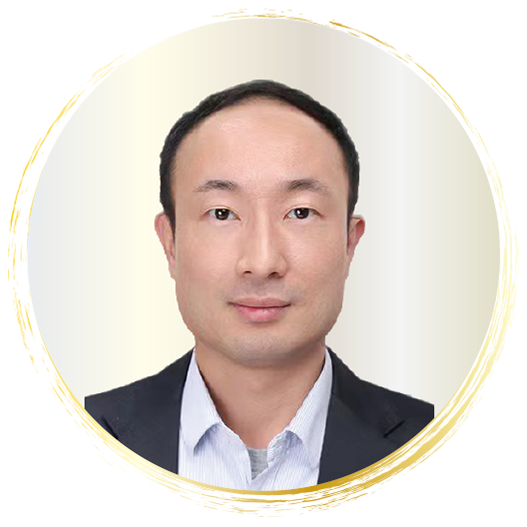
大山氏
現時点ではそのような教育はまだ具体的には行っていませんが、将来的にはやっていきたいと考えています。私も最初は使い方もプラグインもわかりませんでしたが、メモを取るように使えますので、kintoneを覚えてもらって業務改善をできるレベルの人材を育成していきたいと思います。
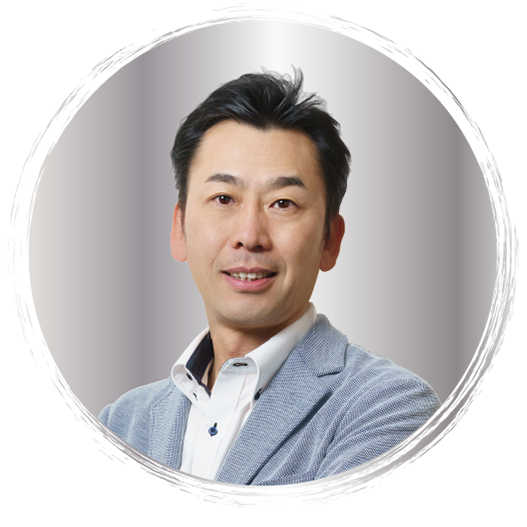
増田
本日はお忙しい中、素晴らしい事例をありがとうございました。皆さま、拍手をお願いいたします。